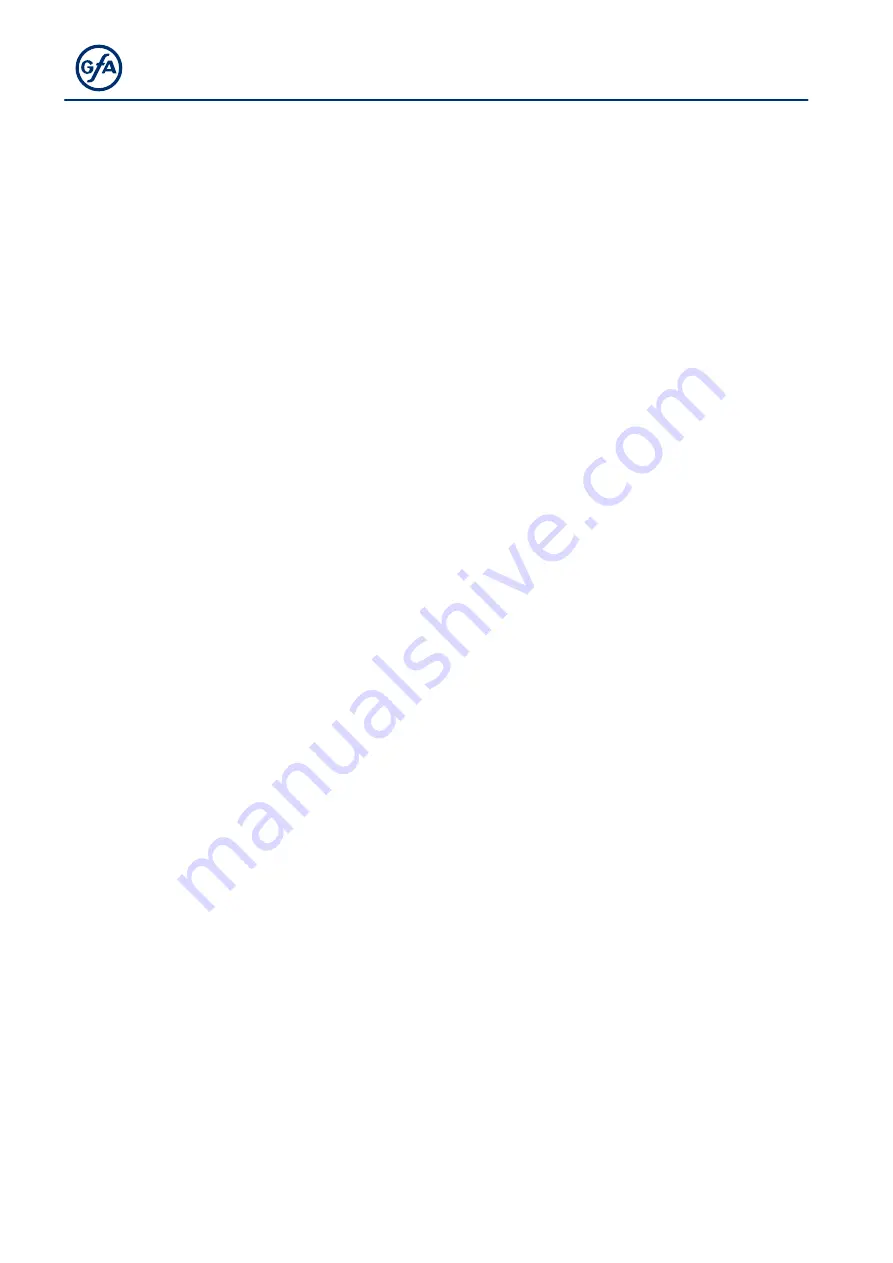
4
1
General safety information
Specified normal use
The drive unit is intended for doors, which have to be secured against falling down. A safety
brake is integrated in the gearbox. The drive unit is mounted directly onto the shaft. In
compliance with its explosion protection according to ATEX 2014/34/EU, it may be used in
explosive areas.
The safe operation is only guaranteed with specified normal use. The drive unit is to be
protected from rain, moisture and aggressive ambient conditions. No liability for damage
caused by other applications or non-observance of the information in the manual.
Modifications are only permitted with the agreement of the manufacturer. Otherwise the
Manufacturer’s Declaration shall be rendered null and void.
Safety information
Installation and initial operation tasks are to be performed by skilled personnel only.
Only trained electrical craftsmen are permitted to work on electrical equipment. They must
assess the tasks assigned to them, recognise potential danger zones and be able to take
appropriate safety measures.
Installation work is only to be carried out with the supply off and in a non-explosive
atmosphere.
Observe the applicable regulations and standards.
Documentation
The drive unit consists of components according to ATEX 2014/34/EU which are reliably
assembled. The documentation refers to the safe installation and operation of the drive unit.
It only quotes excerpts from the original documentation of the components. Should you have
any questions, please contact the manufacturer of the component.
Coverings and protective devices
Do not operate unless corresponding coverings and protective devices are installed.
Ensure that gaskets are fitted correctly and that cable glands are correctly tightened.
Spare parts
Only use original spare parts.
Summary of Contents for SI 80.12-55,00 Ex
Page 27: ...27 14 Declaration of conformity Motor...
Page 28: ...28 15 Declaration of conformity Accessories...
Page 29: ...29...
Page 31: ...31...
Page 32: ...32...