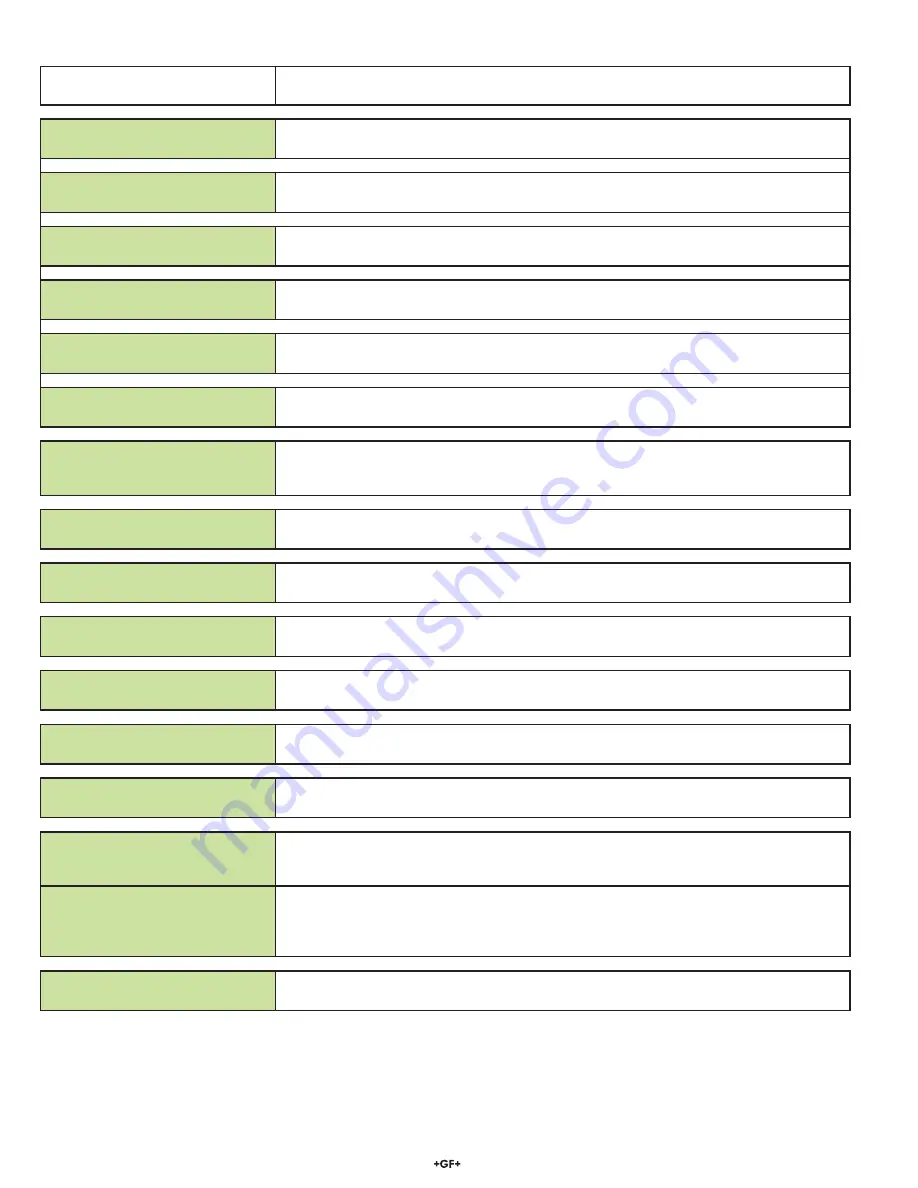
6
8850-2 Conductivity/Resistivity Transmitter
Calibrate Menu
Display
(Factory settings shown)
Description
Cell Constant
Standard >
Select CUSTOM only if you are connecting a certi
fi
ed conductivity sensor. Select STANDARD
for all other systems.
Cell: Standard
1 >
For STANDARD sensors: Select from these options: 0.01, 0.1, 1.0, 10.0 or 20.0.
Cell: Custom
1.0000 >
For CUSTOM sensors: Enter the precise cell constant from the certi
fi
cate provided with your
sensor, or from the information label on the sensor.
Cond Units
μ
S >
Select from these options:
μ
S, mS, k
Ω
, M
Ω
or PPM.
PPM Factor
2.00 >
If the Units selection is PPM, set the ratio of Total Dissolved Solids to
μ
S. The maximum
allowable is 3
μ
S = 1 PPM. The TDS factor can only be set in PPM. See page 9.
Set:
Temperature >
Provides a maximum 25 ºC offset to match temperature measurement to external reference.
Set:
Conductivity >
For use with STANDARD sensors: Perform this single-point wet calibration for most accurate
results. Not required for CUSTOM sensors except for periodic system accuracy con
fi
rmation.
Enter all zeroes to restore factory calibration to TEMP and COND settings.
Loop Source:
Cond >
Select the input (Conductivity or Temperature) source to be associated with the current
loop output.
Loop Range:
μ
S
0.0000 › 100.00 >
Select the minimum and maximum values for the 4 to 20 mA current loop output. Be sure to
modify this setting if you change the Cond. Units.
Relay1 Source:
Cond >
Select Conductivity or Temperature as the source for relay 1.
Relay1 Mode:
Low >
Select the mode of operation for relay 1: High, Low or Proportional Pulse.
The relay may be disabled (Off) if not in use.
Relay1 Setpnt:
10.0000
μ
S >
In Low or High Mode, the relay will be energized when the Conductivity reaches this value. Be
sure to modify this setting if you change the Cond. Units.
Relay1 Hys:
0.5000
μ
S >
In Low or High mode, the relay will be de-energized at Setpoint ± Hysteresis, depending on
High or Low Setpoint selection.
Relay1 Range:
μ
S
10.0000 › 40.0000 >
If Relay 1 is in PULSE mode, set the start and end point of the range and also set the
maximum pulse rate. (The maximum PULSE rate setting is 400 pulses per minute.) Be sure to
modify this setting if you change the Cond. Units.
Relay1 PlsRate:
120 Pulses/min
>
The combined Relay1 Range and Relay1 Pulse Rate settings shown here indicate:
"Start pulsing when the Conductivity value is 10
μ
S and increase the pulse rate up to the
maximum of 120 pulses per minute when the Conductivity value reaches 40
μ
S." The 8850
will accept any value from 0 to 400.
Last CAL:
02-10-09 >
Use this “note pad” to record important dates, such as annual recerti
fi
cation or scheduled
maintenance.
Settings repeat for Relay 2.