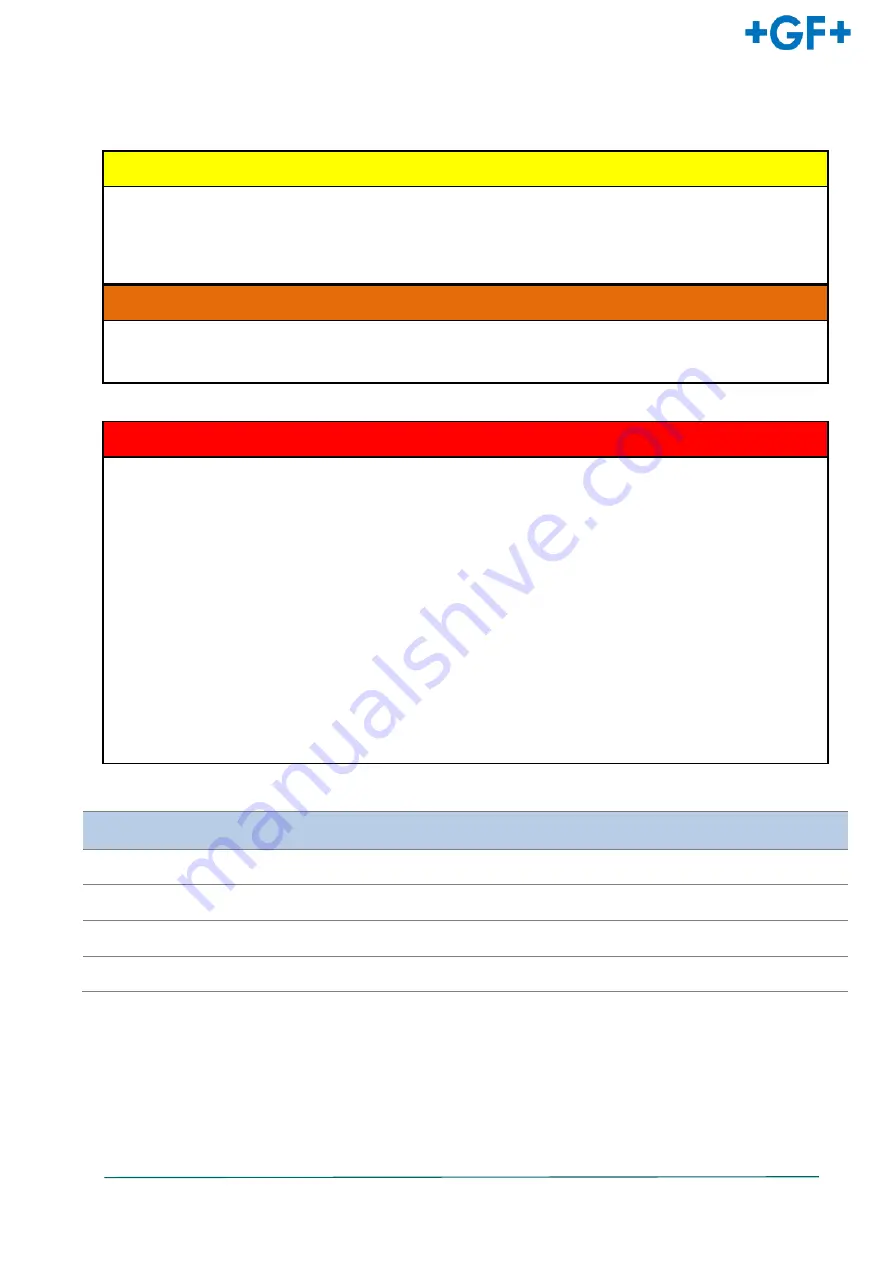
37
4 MAINTENANCE
CAUTION
Leaking due to incompatible components! Danger of injury and/or material damage due to exiting liquids
due to incompatible components.
► Ensure the compatibility of the specifications of the valve and piping system prior to installation
DANGER
Uncontrolled exit of the medium due to residual pressure! Uncontrolled exit of the medium and/or flowing
out of the medium from the open pipe and/or the valve.
► Do not use the NeoFlow pressure reducing valve as an end fitting.
► Completely relieve pressure from the pipe before dismantling.
► Open ball valves slowly!
► Do not stand in the outlet direction of the exiting medium.
► Use eye protection.
► Provide for safe collection of the medium flowing out by implementing appropriate actions.
► Allow the valve to drain in a vertical position and collect the medium during the process.
Maintenance Interval*
Maintenance Task
As required. No later than after one year
Clean/rinse the strainer and control system & Functional tests
As required. No later than after 5 years
Maintenance of the control system (pilot valve, control block)
As required. No later than after 5 years
Maintenance of the valve body (O-rings, strainer)
*Depending on the quality of the pipe and the water, other maintenance intervals may be necessary
WARNING
Maintenance by qualified personnel only! Incorrect handling can damage the NeoFlow pressure reducing
valve. ► Only allow maintenance by persons who have the required training, knowledge, or experience
Summary of Contents for NeoFlow DN200
Page 1: ...Operating instructions NeoFlow Pressure Reducing Valve DN200 DN300...
Page 10: ...10 1 7 BILL OF MATERIALS PRESSURE REDUCING ASSEMBLY...
Page 12: ...12 1 8 BILL OF MATERIALS VALVE BODY...
Page 23: ...23 2 2 2 PERMITTED VALVE ORIENTATIONS Horizontal Orientation Vertical Orientation...
Page 42: ...42...