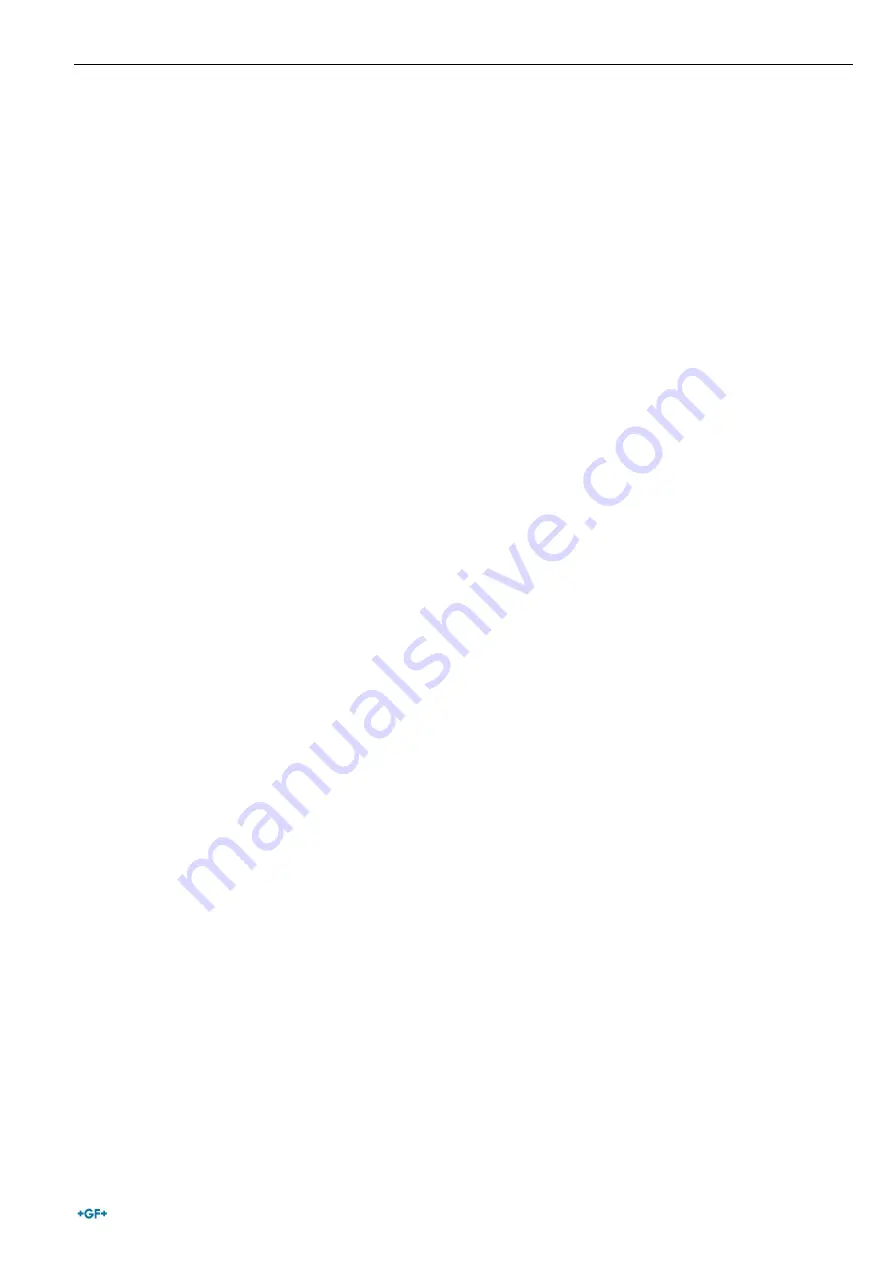
Operating instructions GF 500
8 Failure analysis
27
8
Failure analysis
1. On
cracks parallel to or across the fusion
joint, check:
–
in the joint
–
in the heat flow zone
–
in the basic material
2.
Bead notches
traversing or local notches parallel to the joint with their
roots in the basic material, due to
–
insufficient fusion pressure
–
heat soak time too short
–
cooling time too short
3.
Notches and grooves in the basic material
, running parallel to or across
the joint, due to
–
clamping tools
–
improper transport
–
faulty fusion preparation
4.
Displaced fusion surfaces
due to
–
oval shaped pipe ends (improper storage of pipes!)
–
improper fastening in the clamps
5.
Angular deflection of fused components
due to
–
machine error
–
adjustment error
6.
Fusion bead is narrow, raised, sharp-edged
, over the entire or part of the
joint circumference due to
–
incorrect fusion parameters
7.
Fusion bead is too wide or too narrow
, over the entire or part of the joint
circumference due to
–
wrong heat soak time
–
wrong heater temperature
–
wrong fusion pressure
8.
Fusion bead is uneven
over the entire or part of the joint
circumference due to
–
non-angular fusion surfaces