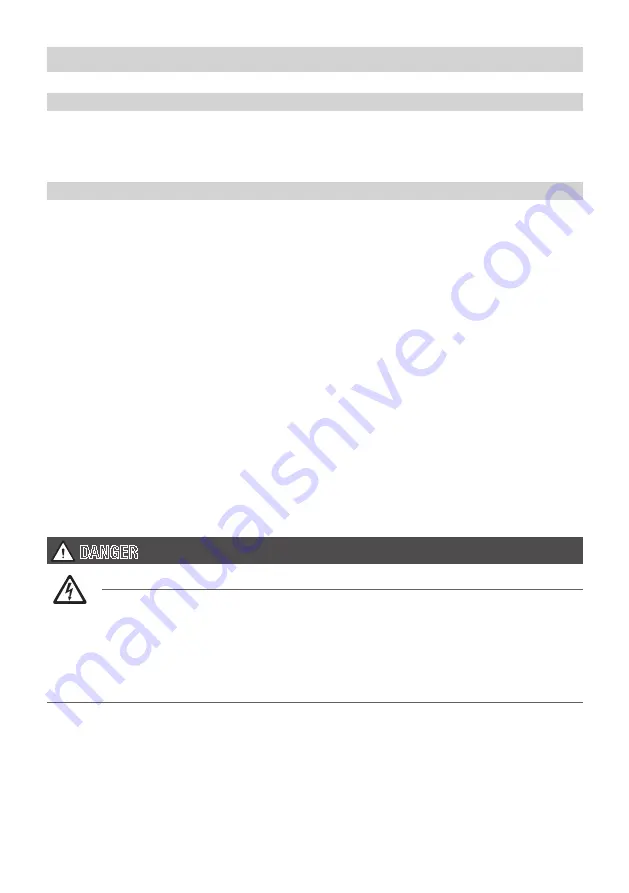
26
NRR 2-60 - Installation & Operating Manual -
819693-00
System malfunctions
Causes
System malfunctions occur if CAN bus components have been incorrectly installed or configured, if the
equipment has overheated, if there is interference in the supply network or if electronic components are
faulty.
Check the installation and configuration before systematic troubleshooting
Installation:
■
■
Check that the installation location complies with the admissible ambient conditions in terms of
temperature, vibration, interference sources, etc.
Wiring:
■
■
Does the wiring conform to the wiring diagrams?
■
■
Is the bus line polarity correct throughout?
■
■
Is a 120 Ω terminating resistor connected to the terminal devices of the CAN bus line?
Controller group and baud rate configuration on the level controller:
■
■
Are the controller group and baud rate correctly set on code switch
D
?
Configuration of electrodes:
■
■
Are the electrodes correctly set and has the measuring range been calibrated?
Baud rate:
■
■
Is the cable length correct for the set baud rate?
■
■
Is the baud rate identical for all units?
DANGER
There is a risk of electric shock during work on electrical systems.
■
■
You must always switch off the voltage to the equipment before working on the terminal
strips (installation, electrical connection, disassembly).
■
■
Disconnect all poles of the supply cable from the mains and secure so they cannot be
switched back on.
■
■
Check that the system is not carrying live voltage before commencing work.
■
■
Interrupting the CAN bus during operation triggers an alarm.