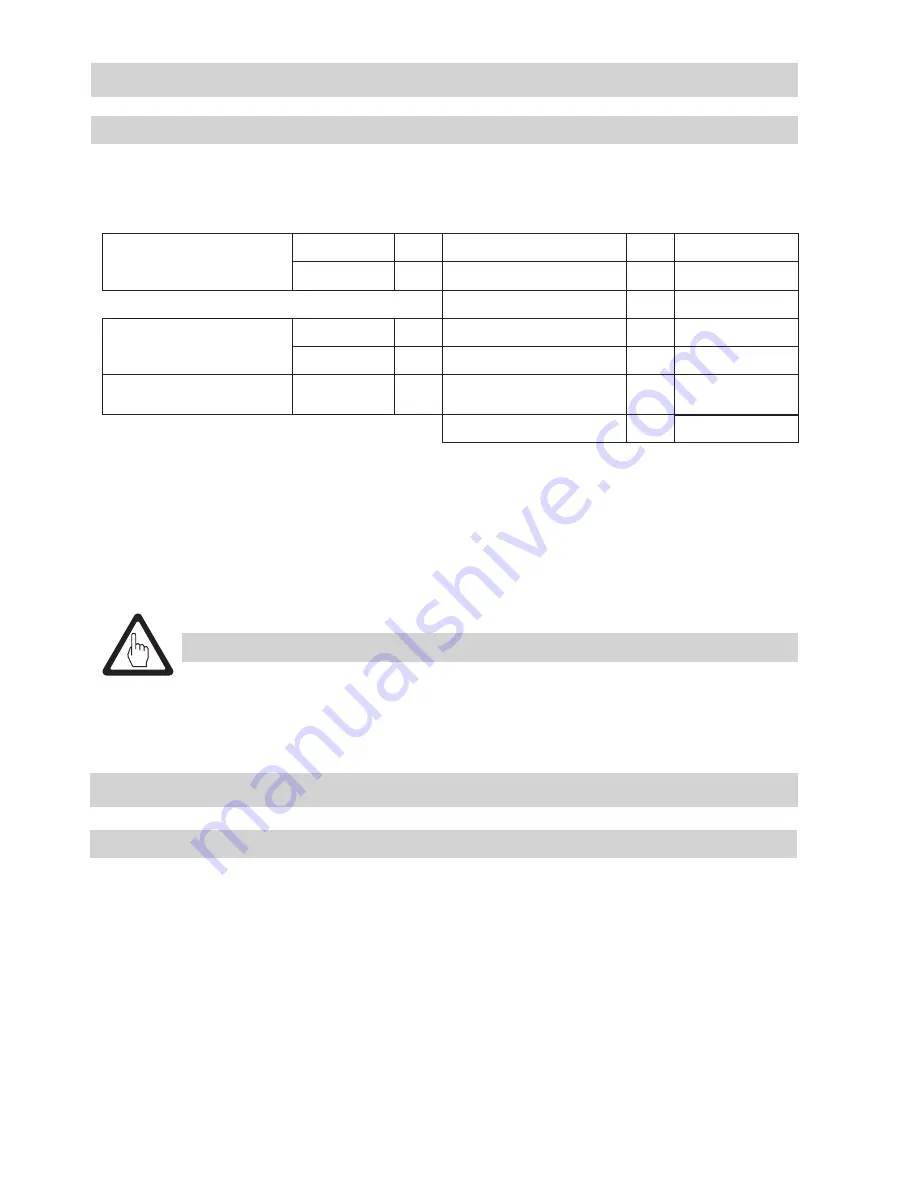
18
Electrical connection
CAN bus voltage supply
To ensure the troublefree operation of the CAN bus system make sure that the voltage supply for all bus
devices is sufficient.
Please use the following table to check the voltage supply of your bus system.
Control units with voltage
supply
Qty.
x
Power output per item
=
Sum
x
6 W
=
W
Please enter data.
Sum 1
=
W
Sensor, transmitter, control
units, operating & display unit
URB 1
Qty.
x
Power consumption per item
=
Sum
x
3 W
=
W
Operating & Display Unit
URB 2
x
5 W
=
W
Please enter data.
Sum 2
=
W
If sum 2 exceeds sum 1 supply the CAN bus with 24 V DC coming from a separate and stabilized safety
power supply unit (e. g. SITOP Smart 24 V 2.5 A) .
The power supply unit must be electrically isolated from dangerous contact voltages and must meet at
least the requirements on double or reinforced isolation acc. to DIN EN 50178 or DIN 61010-1 or
DIN EN 60730-1 or DIN EN 60950 (safe isolation).
The power supply unit must be provided with an overcurrent protective device in accordance with
EN 61010-1.
Attention
If a safety power supply unit (e. g. SITOP smart, 24 V, 2.5 A) is used for the voltage supply
of the CAN bus do not tap the supply voltage from the terminals 1 and 5 of the GESTRA
control devices.
SITOP smart is a registered trademark of Siemens AG, Munich
Bus line
All devices (level, conductivity) are interconnected via CAN bus. The CANopen protocol is used for the
data exchange between the equipment groups. All devices have an electronic address - the node ID. The
control cable serves as power supply and data highway for high-speed data exchange.
The CAN address (node ID) can be set between
1
-
123.
If several identical systems are to communicate in a CAN bus network, set a different node ID for
each system (e. g. limiter, controller, etc).
If the length of the CAN bus cable exceeds 125 m change the settings of the code switch
c
.
For more information on switch positions see
Basic Settings
/
Switch positions
.
Basic settings
- continued -