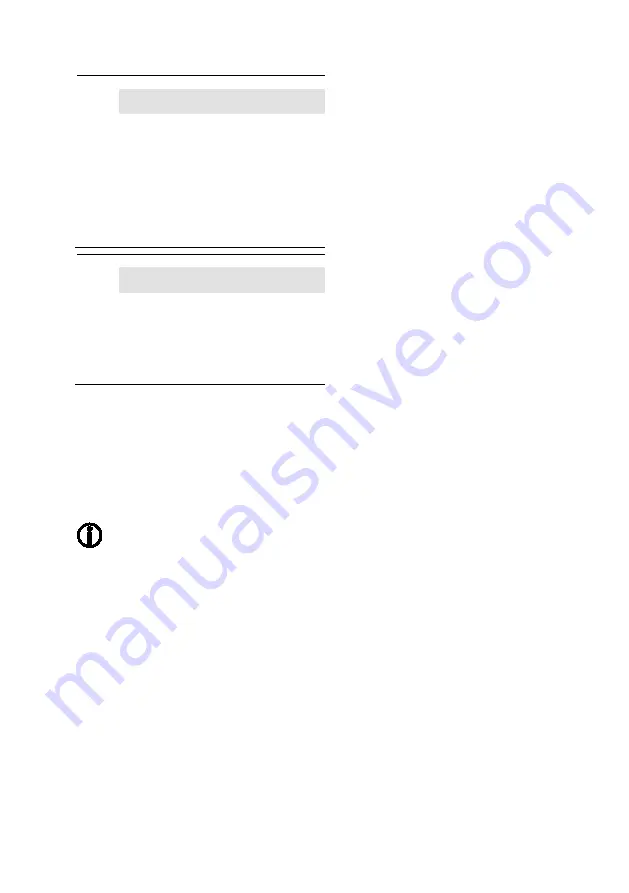
27
Installing the double cone
Attention!
Equipment may leak if the gasket is
damaged.
Replace all gaskets that you loosen
during your work.
Use only new gaskets of the same
type.
Attention!
Dirt deposits on gasket seating surfaces
may result in leaking of the equipment.
Clean seating surfaces before
inserting a new gasket.
Replace all gaskets with new ones of the same
type.
To install the double cone in the body, proceed as
follows:
Screw the adjusting key completely out of the
body.
Models with r-cone are equipped with an
additional O-ring on the double cone. You
must also replace this O-ring before
installing the double cone.
Remove the old O-ring.
Dispose of the O-ring in accordance with
regulations at the location of use.
Insert a new O-ring in the double cone from
underneath.
Push the new O-ring up until it is lying against
the collar of the double cone.
You can now install the double cone in the body.
Insert the double cone in the body with the
opening facing downwards.
Position the spring on the double cone.
Fit a new body gasket on the four setscrews on
the body opening.
Lubricate all threads and the contact surfaces of
nuts and bolts with temperature-resistant
lubricant.
The lubricant must have the same properties as
OKS
®
217.
Mount the lid on the four setscrews on the body
opening.
Press the lid down sufficiently far to allow the
hex nuts to fit onto the setscrews.
Tighten the hex nuts crosswise,
making sure that the lid and hex nuts do not
become crooked.
The torque required to secure the hex nuts varies
depending on type:
For models with DN25, DN40 and DN50, a
torque of 15 Nm is required.
For models with DN80 and DN100, a torque of
25 Nm is required.
Tighten the hex nuts crosswise to the specified
torque.
Set the cooling-water outlet temperature as
described on page 15.
Set the bleed flow as described on page 17.
Summary of Contents for Gestramat CW 41
Page 21: ...21 Spare parts for CW 41 4 ...
Page 34: ...34 MCW 41 and MCW 41 4 ...
Page 38: ...38 ...
Page 39: ...39 ...