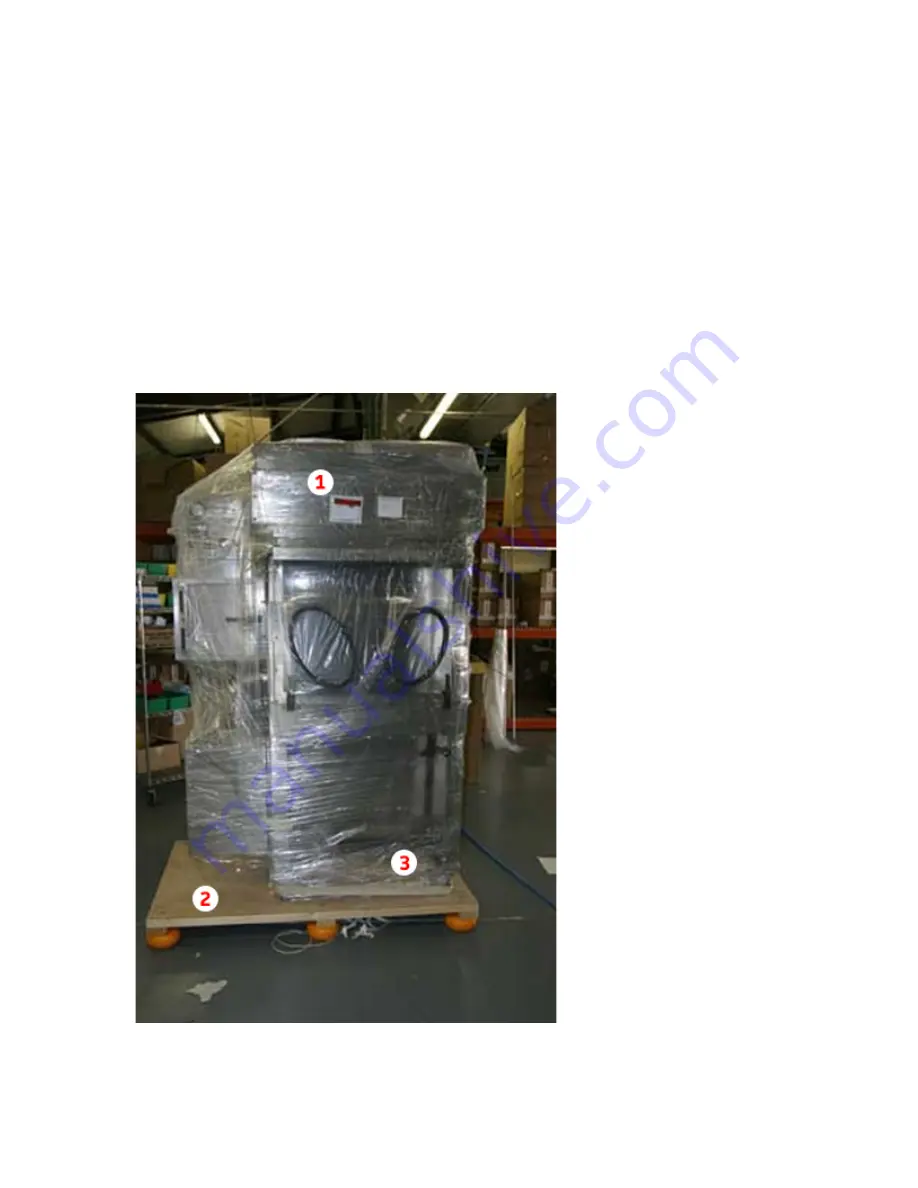
Unpacking Instructions
The Laminar Flow Glovebox is shipped fully assembled in a single crate. All equipment
must be inspected immediately upon receipt. If there is visible damage to the container or
unit it must be noted on the receiving documents by the driver. The carrier must then be
notified to arrange for an immediate inspection to verify the damage to the equipment. If
damage to the unit is found after it is uncrated (concealed damage), the receiver should
notify the delivering carrier at once. Do not move the equipment or discard any of the
shipping materials until a concealed damage inspection is performed. If the carrier will not
perform this service, please contact the factory immediately at 800- 888-5357. Without this
inspection of the equipment and packing materials, the freight company may not accept a
claim for damage or loss and take the position that the damage occurred after delivery.
Packaged LFGI
1. Packing List
2. Pallet with donut lifts for
pallet jack
3. Casters are locked for
shipping and are touching
the mounting rack.
LFGI is on a rack to
prevent movement during
shipping.
DO NOT USE A FORK
LIFT TO REMOVE LFGI
FROM THE PALLET
Extra prefilters are included
and inside the LFGI. Store
these filters for future
replacement.
14
Summary of Contents for LFGI-3USP
Page 1: ...Laminar Flow LFGI CAI or CACI User Manual ...
Page 33: ...33 ...
Page 51: ...SECTION IV UNIT DIAGRAM Made in the USA and available for purchase on the GSA 51 ...
Page 55: ...55 ...
Page 59: ...59 ...
Page 63: ...Fig 2 Air recycle plenum connection tip removed 63 ...
Page 85: ... 863 248 2800 www sensocon com 20 Installation and Operation Manual Series A3 A4 ...