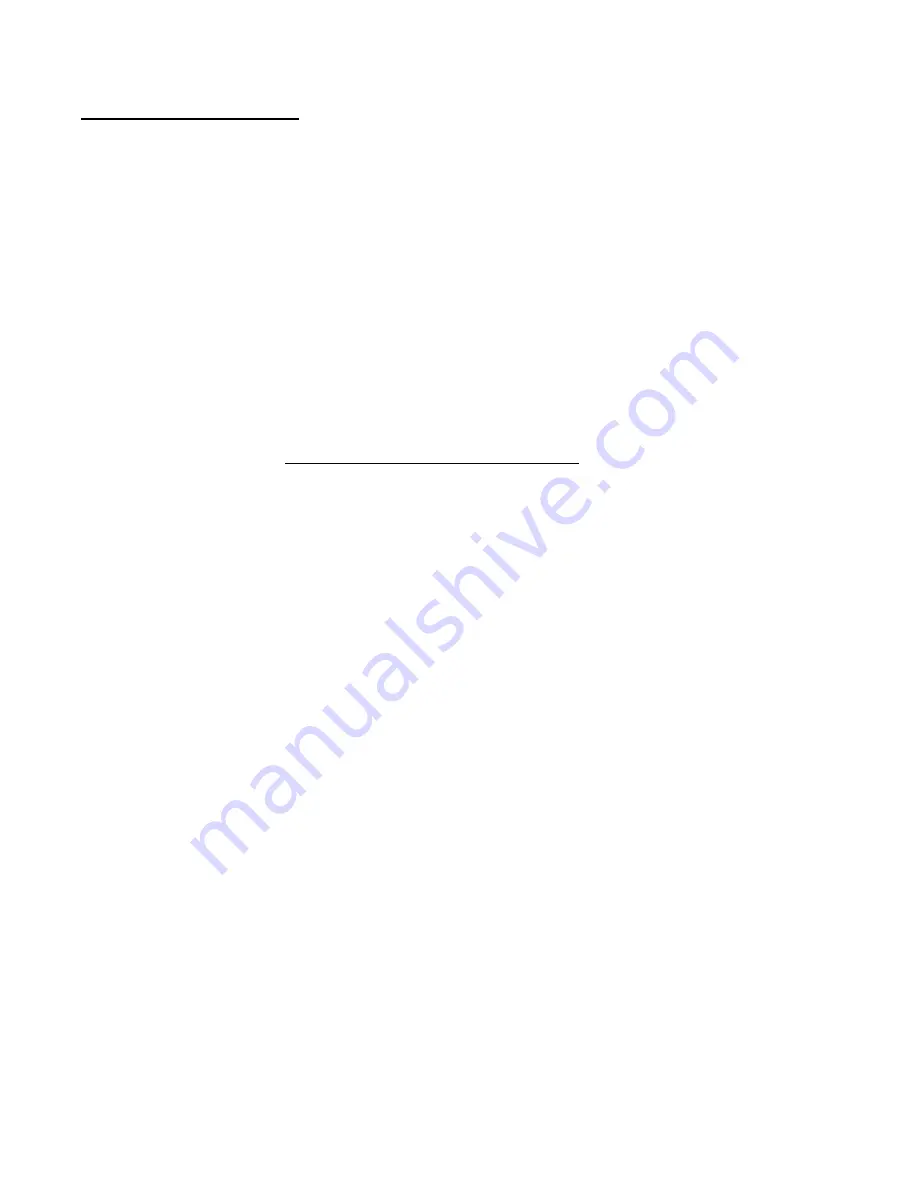
16
7. DATA INTERPRETATION
Readings on Channel C of the GK-401, GK-403 or GK-404 Readout Box are displayed
directly in microstrain based on the theoretical equation;
theory
= 4.062 (f
2
10
3
)
Where
is the microstrain and f is the resonant frequency of the vibrating wire.
7.1 Conversion of the Readings to Strain Changes
In practice the method of wire clamping effectively shortens the vibrating wire slightly
causing it to over-register the strain. This effect is removed by applying a batch gage factor
(B) supplied with the gages. (A
typical
batch gage factor for the Model 4000 strain gage is
around 0.96). The
actual
batch factor is supplied on a sheet with the gages – please refer to
that.
apparent
= (R
1
R
0
)B
Equation 5 - Apparent Strain Calculation
Where R0 is the initial reading on Channel C and R1 is a subsequent reading.
Note: when (R1
R0) is positive, the strain is tensile.
This value of the apparent strain is the one required for computing stresses in equations 2
through 4 on page 8. The stresses thus computed are the total of those caused by both
construction activity and by any temperature change that may have occurred.
7.2 Converting Strains to Stresses
Whereas strain gages measure strain or deformation of the structure, the designer is more
interested in the structural loads or stresses. This requires a conversion from the measured
strains to computed stresses.
Strain changes with time are computed from strain gage readings taken at various times,
and by comparison with some initial readings taken at time zero. This initial reading is best
taken when the structural member is under no load, i.e., the gages should be mounted while
the member is still in the steel yard or warehouse.
This is not always possible and often strain gages are installed on members that are under
some existing load so that subsequent strain changes always take off from some unknown
datum. However, a technique exists, namely the "Blind Hole Drilling Method" (Photolastic
1977), whereby residual or existing stresses can be measured. The procedure is to cement
a strain gage rosette to the surface and then to analyze the strains caused by drilling a short
blind hole in the center of the rosette. However, it is a well-known fact that strains can be
locked into the steel during its manufacture. (Often, the skin of a rolled-steel structural
member is under tension relative to the underlying steel).
Sometimes it is possible, especially where temporary supports are being monitored, to
measure the strain in the structural member after the structure has been dismantled. This
no load reading should agree with the initial no load reading if one was obtained. Any lack
of agreement would be an indication of gage zero drift although the possibility of some
permanent plastic deformation of the member should not be overlooked, particularly where
measured strains were high enough to approach the yield point.