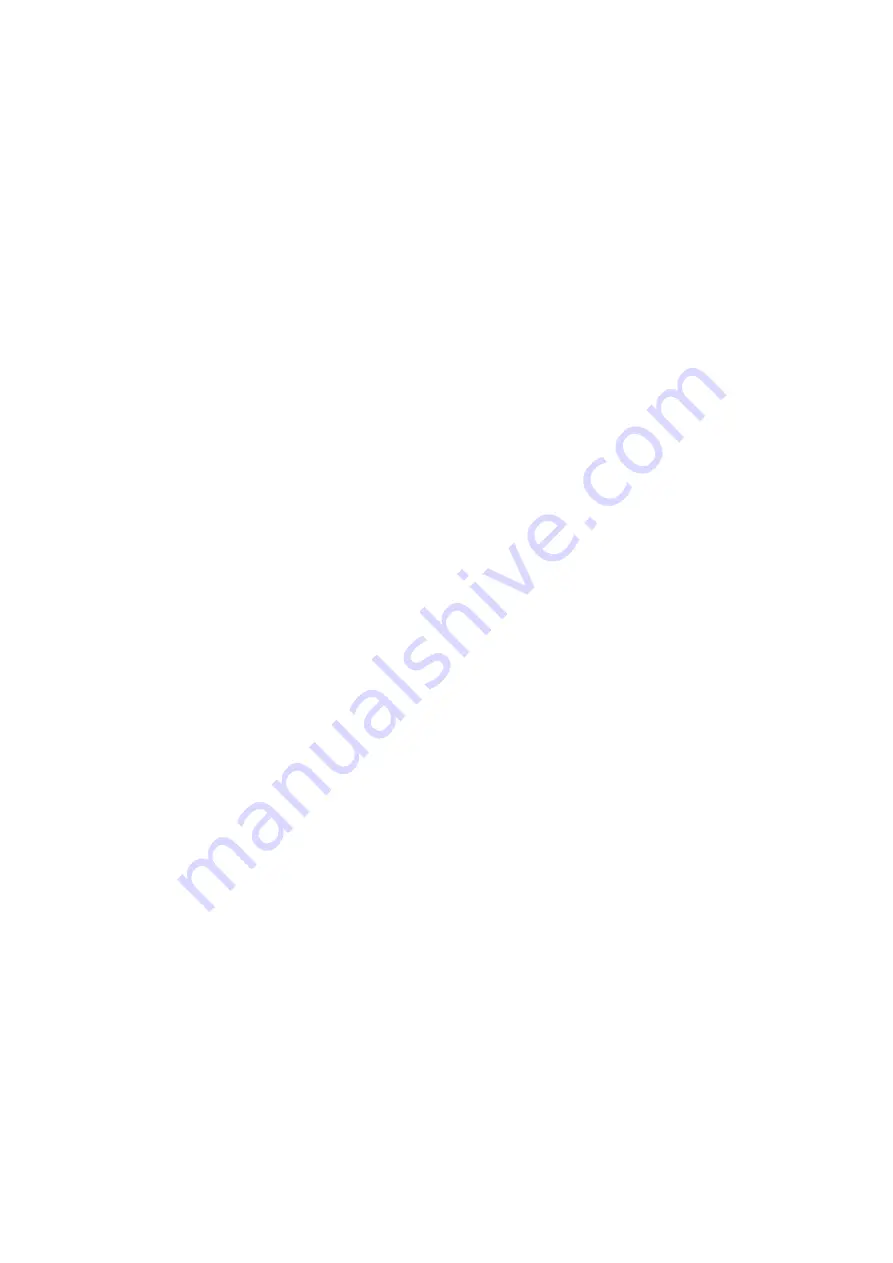
9
Guidelines & Standard Settings
The following information covers some basic guidelines for pressing,
as well as some generic parameters for basic heat transfer applications.
•
When pressing shirts, it is often recommended that the shirts be quickly
pressed for 2 to 4 seconds before transferring to remove wrinkles and water
content.
•
When pressing two sides of a garment, pull the garment over the table so
that the printed side drapes underneath the table. This will avoid reheating
previously transferred designs on opposite sides of garments. It will also
avoid any bleed-through of inks on lighter fabrics.
•
Avoid laying collars, cuffs, zippers, and other bulky parts of garments
on the lower table, as these can adversely affect pressing conditions, and
reduce the life of the silicone pad.
•
When pressing rigid substrates (plastics, metals, woods, etc.), be sure that
any protective films or laminates are removed before heating.
•
Always check that the transfer image is face down against the material, to
avoid sealing the image against the heat platen instead of the substrate.
Always follow the transfer media suppliers instructions when
pressing. The information below is for general reference only, and may
not be as accurate as the instructions provided by the transfer media &
imprintable substrate supplier.
•
Hot Split Supplier Transfers
350-375°F, 8-10 secs
•
Puff
Transfers
350-375°,
5-7
secs
(extra heavy pressure)
•
Ink-Jet Transfer Papers
360°, 15-18 secs
•
ColorCopy/Laser Transfer Papers 375°, 20-25 secs
• Sublimation
Inks
(Polyester Fabrics)
400°, 35 secs
• Sublimation
Inks
(Plastics)
400°, 1 min, 15 secs
• Sublimation
Inks
(Metals)
400°, 1 min
• Sublimation
Inks
(Woods)
400°, 1 min, 15 secs
• Sublimation
Inks
(Ceramics)
400°, 4 min