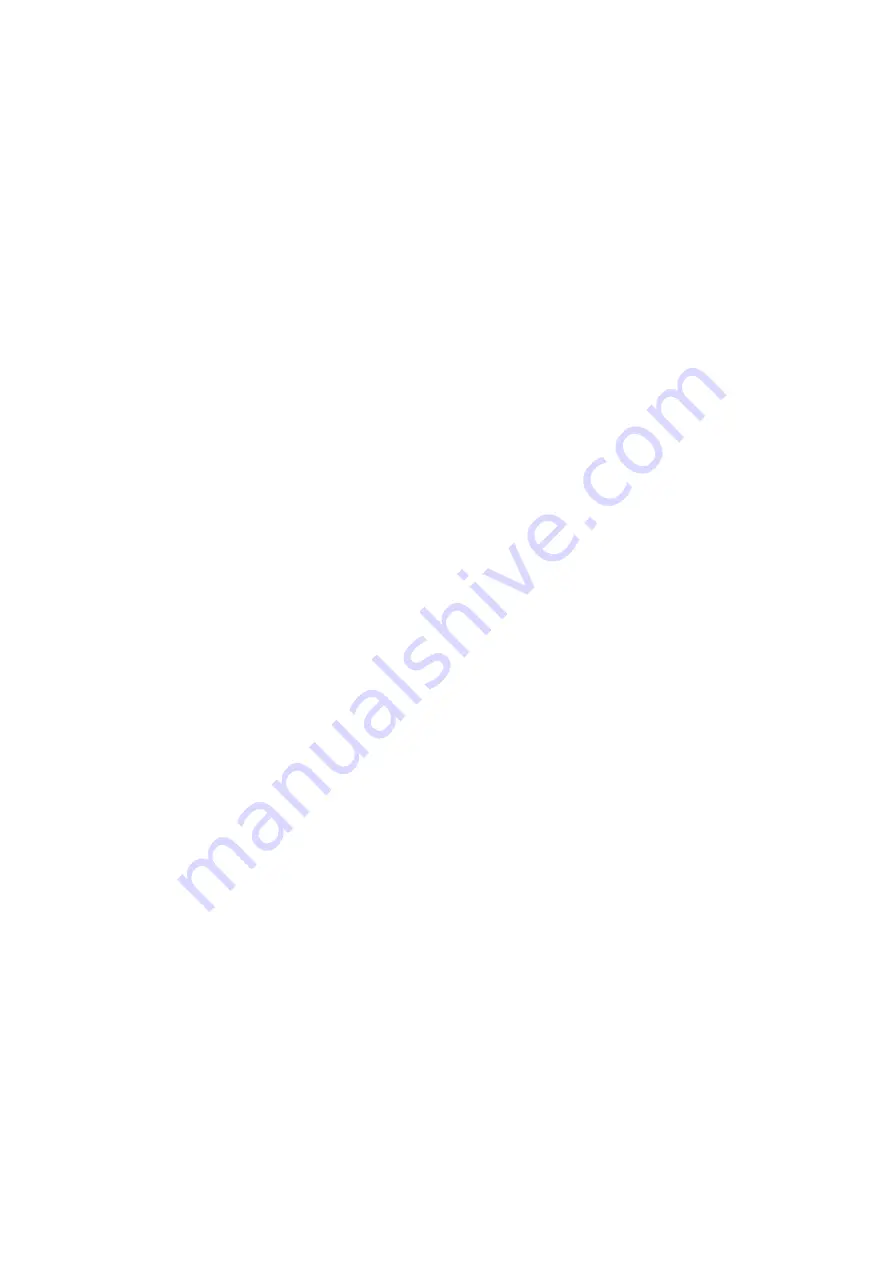
23
Troubleshooting
The following information attempts to address the most probable
mechanical and user issues with the press. Most issues with heat transfer
presses are application related. That is, they have to do with the results
of a particular transfer application.
For technical support on problems having to do with the final results
of a particular transfer paper or media, please contact the supplier of
that transfer media. Generally, the machinery manufacturer is unable
to support the myriad of different transfer papers, inks and imprintable
items on the market from other resellers.
Q.
The timer does not start when I close the heat platen, or the timer
does not reset when I open the press up.
A.
There are several probable causes for this. The timer is activated
by a micro-tilt-sensor stuck to the pressure arm. First: When the head of
the machine is opened, the tilt sensor needs to be tilted slightly upward
to signal the controller to stop/reset. When the head of the machine
is closed, the timer sensor needs to be tilted downward (towards the
floor) to signal the controller to start counting. Second: Check the wire
connection from the tilt sensor into the control panel. The timer &
pressure signals go to a small black 6-pin connector on the top of the
circuit board in the control box. Check to make sure this is firmly seated
and plugged into the board.
Q.
The control displays Err when it first comes on, and I can not set
the temperature or use the press.
A. The
Err message will display if the heating signal from the platen
has been cut off, interrupted, or the heating sensor has failed. First check
the Lime Green temperature connector that plugs into the digital control.
At the top of the controller, there is a green connector that plugs in with
2 small wires. This is the temperature sensor wire. Check to make sure
is it properly seated. If after unplugging and plugging the lime green
connector the Err message still appears. unplug the green connector and
remove the 2 tiny wires from the lime green plug. Cut them back 1/4”
and strip them so they have new connections. Reconnect them to the
lime green plug so they are screwed in tightly and can not pull out. Plug
the green plug back in and turn the press on.