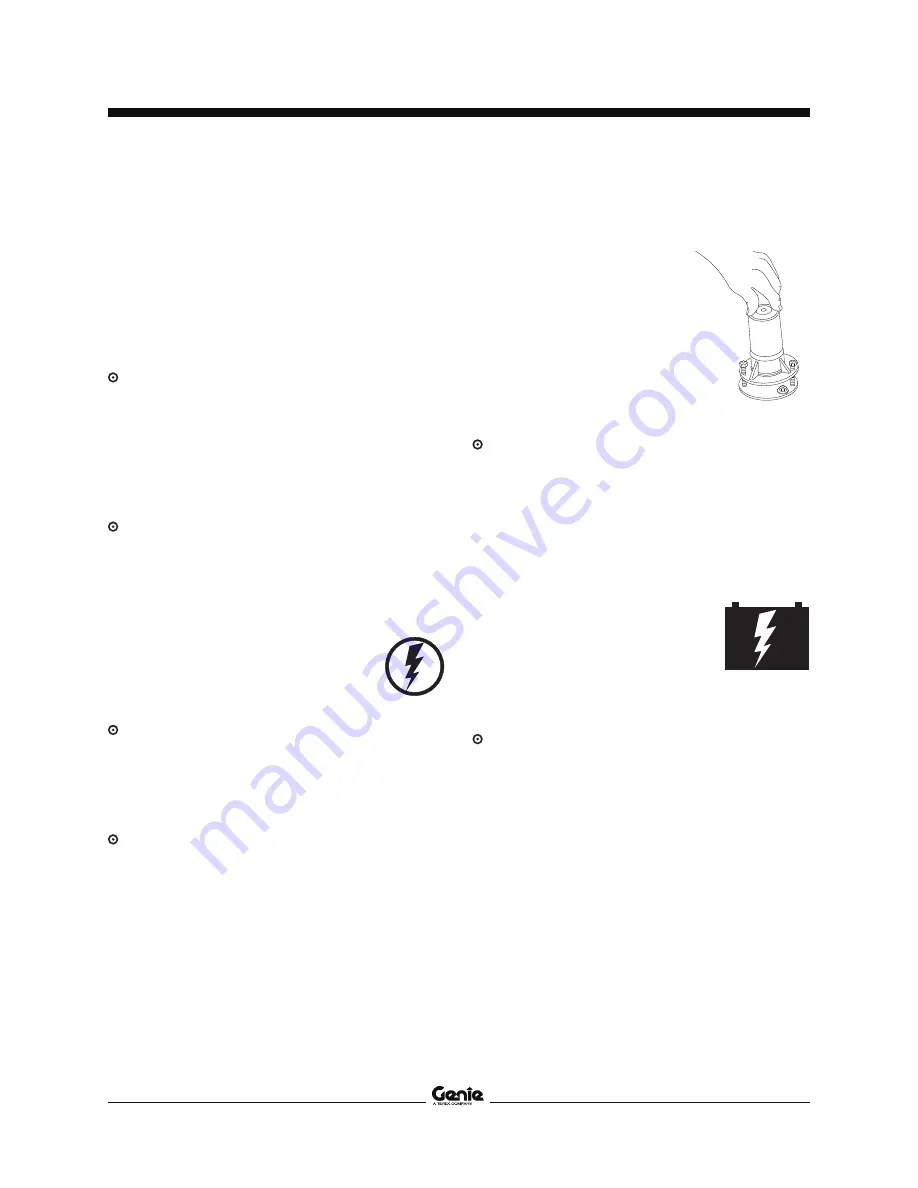
Operator's Manual
Seventh Edition · First Printing
28
Z-60/34
Part No. 133083
Inspections
Test the Tilt Sensor
9 Turn the key switch to
platform control. Pull out the
platform red Emergency Stop
button to the on position.
10 Open the control panel side
turntable cover and locate the
tilt sensor next to the control
box.
11 Press down one side of the tilt sensor.
Result: The alarm, located in the platform,
should sound.
Test Auxiliary Controls
12 Turn the key switch to ground control and shut
the engine off.
13 Pull out the red Emergency Stop button to the
on position.
14 Simultaneously hold the
auxiliary power switch on and
activate each boom function
toggle switch.
Note: To conserve battery power, test each
function through a partial cycle.
Result: All boom functions should operate.
1 Select a test area that is firm, level and free of
obstruction.
At the Ground Controls
2 Turn the key switch to ground control.
3 Pull out the red Emergency Stop button to
the on position.
Result: The beacon (if equipped) should flash.
4 Start the engine. See Operating Instructions
section.
Test Emergency Stop
5 Push in the red Emergency Stop button to the
off position.
Result: The engine will shut off after 2 to 3
seconds.
6 Pull out the red Emergency Stop button to
the on position and restart the engine.
Test the Machine Functions
7 Do not hold the function enable
switch to either side. Attempt to
activate each boom and platform
function toggle switch.
Result: All boom and platform functions should
not operate.
8 Hold the function enable switch to either side
and activate each boom and platform function
toggle switch.
Result: All boom and platform functions should
operate through a full cycle. The descent alarm
should sound while the boom is lowering.