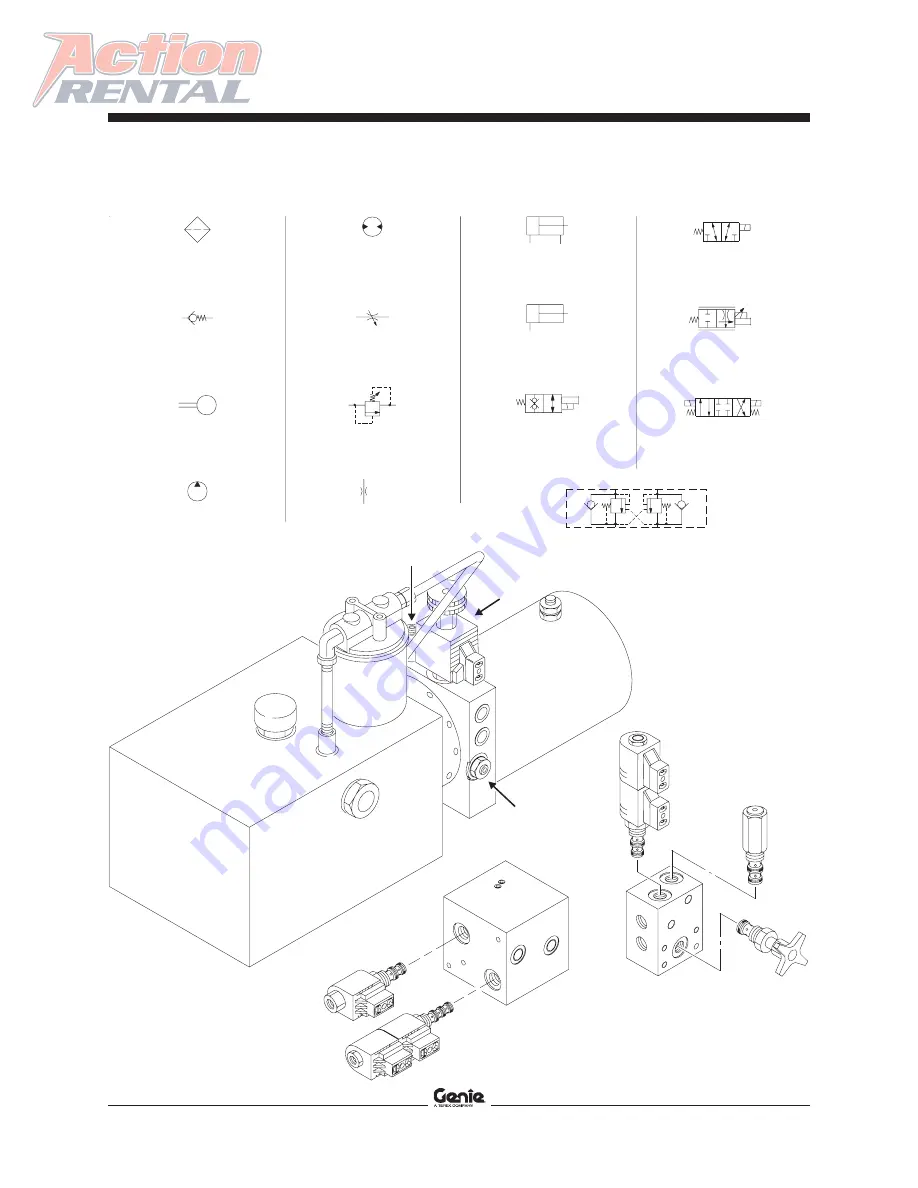
REV A
Section 6 • Schematics
June 2005
Part No. 52075
TMZ-34/19
6 - 13
Hydraulic Symbols Legend and
Component Reference
0.037 in
9.4 mm
Y45
Y9
M
Y24
Y23
Y41
4000 psi
275.8 bar
3:1
2000 psi
137.9 bar
3:1
I
J
H
Y23
Y24
K
L
Y41
Y39
Y48
D
E
Y9
F
Filter
Check valve
Motor
Fixed displacement pump
Bi-directional motor
Shut off valve
Relief valve
Orifice with size
Dual acting cylinder
Single acting cylinder
Solenoid operated
2 position 2 way
directional valve
Solenoid operated
2 position 3 way
directional valve
Proportional valve
Solenoid operated
3 position 4 way
directional valve
Counterbalance valve
Hydraulic power unit
components
Outrigger manifold
components
Turntable manifold
components
800-610-4101
ActionRental.com