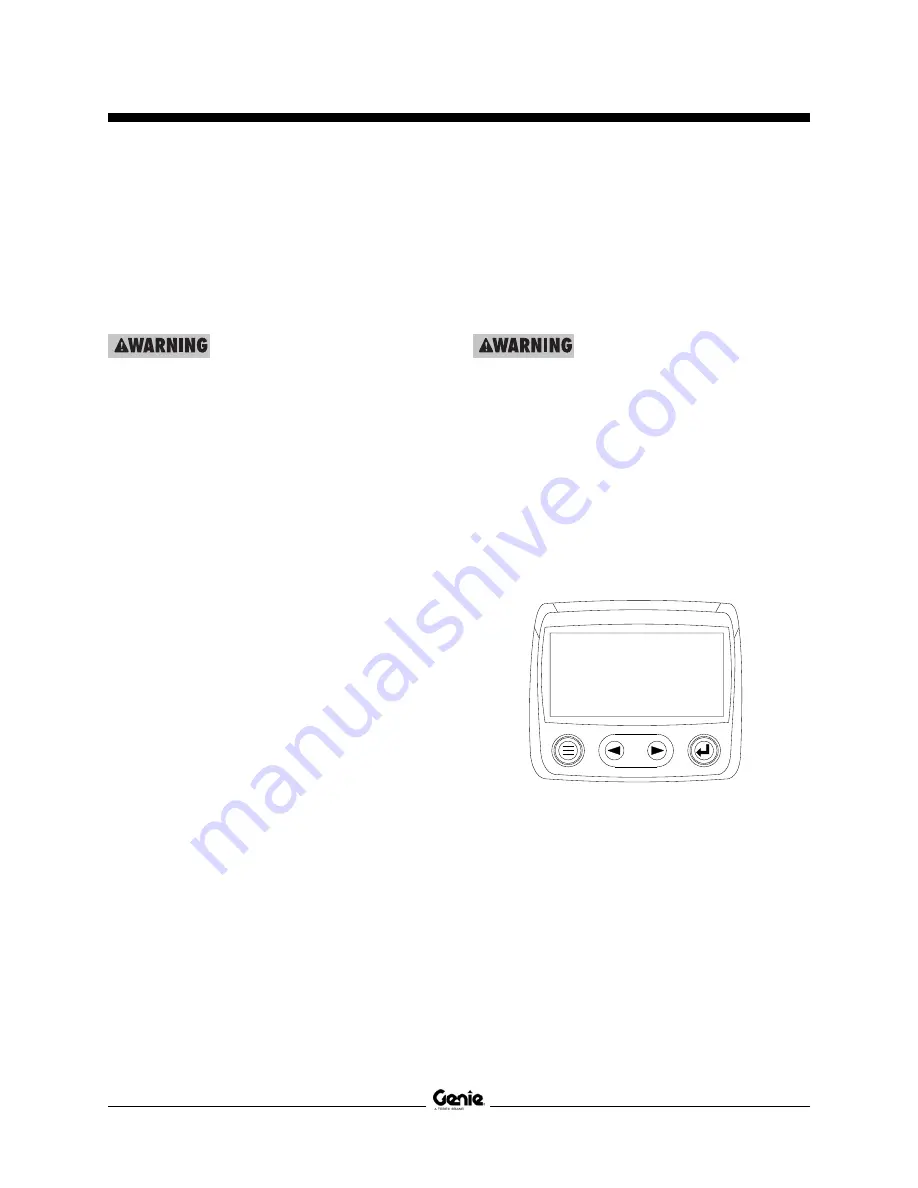
Section 4 • Repair Procedures
March 2015
4 - 28
GTH-1048 • GTH-1056
Part No. 123701
How to Remove the Dash Cluster
Assembly
1 Open the access door above the hydraulic tank.
2 Disconnect the battery from the machine.
Electrocution hazard. Contact with
electrically charged circuits could
result in death or serious injury.
Remove all rings, watches and
other jewelry.
3 Remove the fasteners securing the
transmission control lever to the column.
Carefully separate the lever from the column.
4 Reach under the dashboard and gently push
the dash cluster through the opening in the
dashboard.
5 Tag and disconnect the wire harness from the
dash cluster. Remove the dash cluster from the
machine.
How to Remove the Diagnostic
Display
1 Open the access door above the hydraulic tank.
2 Disconnect the battery from the machine.
Electrocution hazard. Contact with
electrically charged circuits could
result in death or serious injury.
Remove all rings, watches and
other jewelry.
3 Reach under the dashboard and gently loosen
and remove the locknut securing the diagnostic
display to the dashboard. Gently push the
diagnostic display through the opening in the
dashboard.
4 Tag and disconnect the wire harness from the
diagnostic display. Remove the diagnostic
display from the machine.
OPERATOR'S COMPARTMENT
Summary of Contents for GTH-1048
Page 6: ...May 2015 GTH 1048 GTH 1056 Part No 123701 vi This page intentionally left blank ...
Page 174: ...Section 6 Schematics May 2015 6 11 Harness Map Control System Power Single Joystick 6 12 ...
Page 177: ...May 2015 Section 6 Schematics 6 14 Harness Map Control System Ground Single Joystick 6 13 ...
Page 178: ...Section 6 Schematics May 2015 6 15 Harness Map Control System Power Dual Joystick 6 16 ...
Page 181: ...May 2015 Section 6 Schematics 6 18 Harness Map Control System Ground Dual Joystick 6 17 ...
Page 190: ...Section 6 Schematics May 2015 6 27 Harness Map Options Work Lights 6 28 ...
Page 193: ...May 2015 Section 6 Schematics 6 30 Harness Map Options Road Lights 6 29 ...
Page 194: ...Section 6 Schematics May 2015 6 31 Harness Map Options Enclosed Cab with Heater 6 32 ...
Page 197: ...May 2015 Section 6 Schematics 6 34 Harness Map Options Enclosed Cab with HVAC 6 33 ...
Page 210: ...Section 6 Schematics May 2015 6 47 Hydraulic Schematic Models with Single Joystick 6 48 ...
Page 213: ...May 2015 Section 6 Schematics 6 50 Hydraulic Schematic Models with Dual Joystick 6 49 ...
Page 214: ......