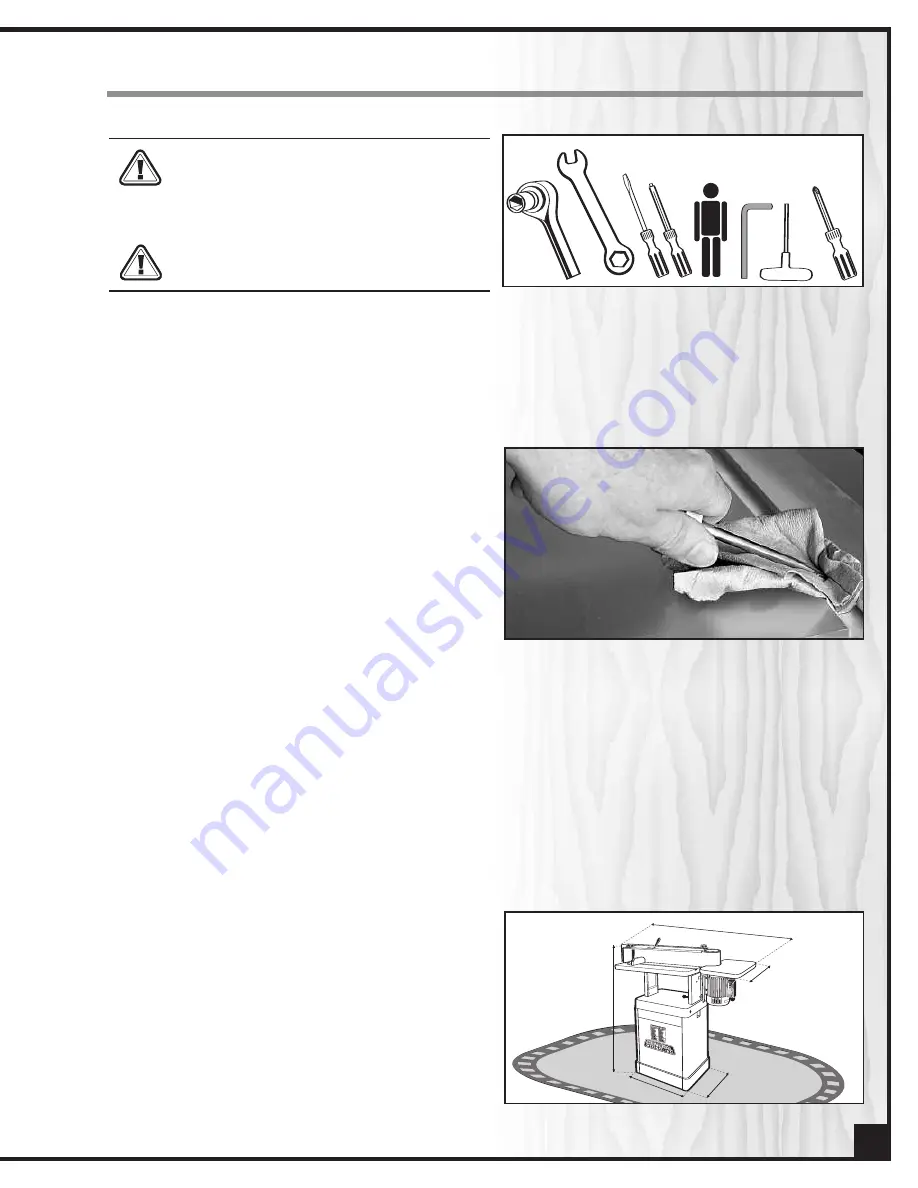
PREPARATION AND PLACEMENT WITHIN THE SHOP
SET UP SAFETY
ADDITIONAL REQUIREMENTS FOR SET UP
•
12 mm Hex socket or 12 mm Open end wrench
• Flat head screwdriver
• Small square head screwdriver
• Extra person for help with lifting
• 4 mm Allen key or 4 mm T-handle hex wrench
• Phillips screwdriver
Serious personal injury could occur if you connect
the machine to the power source before you have
completed the set up process. DO NOT connect
the machine to the power source until instructed to
do so.
The MODEL 15-005S is a heavy machine (277 LBS -
126 kg). Do not over-exert. Arrange to have help
nearby and ready for unpacking and set- up.
HEX SO
CLEAN UP
The unpainted cast-iron surface of the tables are covered
with a protective coating that helps prevent rust from
forming during shipping and storage. Remove this protec-
tive coating by rubbing with a rag dipped in kerosene,
mineral spirits or paint thinner.
(Handle and dispose of poten-
tially flammable solvent soaked rags according to manufactur-
ers’ safety recommendations.)
A putty knife, held flat to avoid
scratching the surface, may also be used to scrape off the
coating followed by clean-up with solvent. Avoid rubbing
the painted surfaces, as many solvent based products will
remove paint.
To prevent rust, apply a light coating of paste wax or use
regular applications of any after-market surface protec-
tant or rust inhibitor such as General International “Top
Saver” item #GC-010.
Tip/Hint: With a screw driver, push a solvent-saturated rag into the
T-slot to remove the grease so the miter gauge will slide freely.
PLACEMENT WITHIN THE SHOP
This model 10-005S MI should be installed and operated only on a solid, flat and stable floor that is able to support
the weight of the sander (277 LBS -126 kg) and the operator. Using the dimensions shown as a guideline, plan for
placement within your shop that will allow the operator to work unencumbered and unobstructed by foot traffic
(either passing shop visitors or other shop workers) or other tools or machinery.
ESTABLISHING A SAFETY ZONE
For shops with frequent visitors or multiple operators, it is
advisable to establish a Safety Zone around shop
machinery. A clearly defined “no-go” zone on the floor
around each machine can help avoid accidents that
could cause injury to either the operator or the shop visi-
tor. It is advisable to take a few moments to either paint
(using non-slip paint) or using tape, define on the floor the
limits or perimeter of each machines safety zone. Take
steps to ensure that all operators and shop visitors are
aware that these areas are off limits whenever a machine
is running for everyone but the individual operating the
unit.
50”
21 1/2”
17”
21”
49”
7
OR
OR
Summary of Contents for 15-005S
Page 18: ...18...