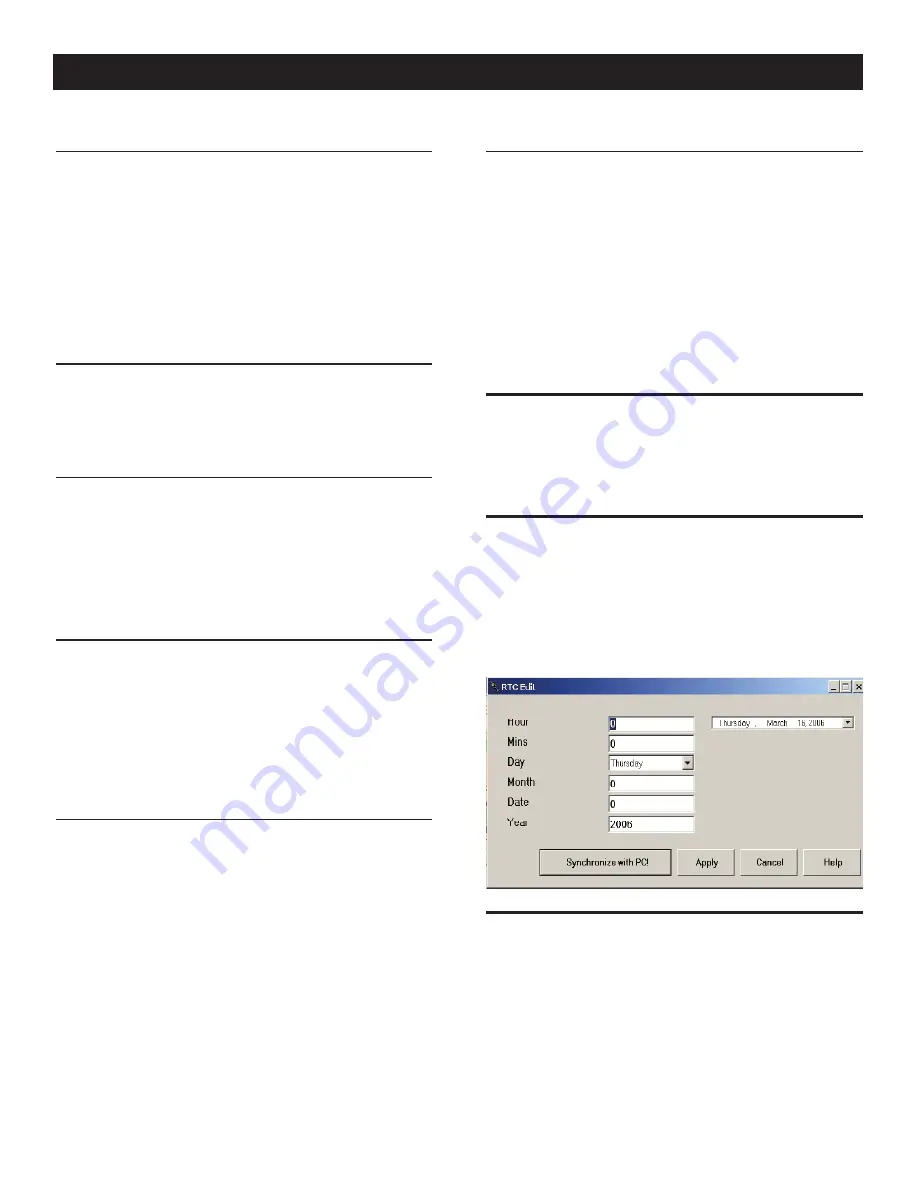
8
3.4.2 LOAD SHED 1, 2 & 3 KW
These values are only used if the Load Shed Enable box is checked.
If generators within the system go off-line, load shed contacts will
be closed (activated) based on the values entered here. The load
sheds have a priority, with load shed 1 being the highest. If the
value in load shed 1, added to the critical load value, cannot be
supported by the system, the three load sheds all activate. If criti-
cal plus load shed 1 can be supported, but not load shed 2, then
2 and 3 activate. However, because of the priority, if load shed 1
cannot be supported, but load sheds 2 and 3 can, they all still
must activate.
3.4.3 ATS CRITICAL LOAD
The number entered here tells the PM-SC the critical standby load.
This value is typically set to be equal to the size of the smallest
generator in the system. This value typically represents the size of
the “critical load 10 second start” transfer switch as well.
3.4.4 PERMISSIVE (ATS LOAD) 1, 2, 3
These values are used to control the permissive outputs of the
PM-SC. Each one represents a permissive relay (two contacts).
ATS 1 load has a higher priority than ATS 2, which is higher than
ATS 3. Therefore, when closing permissive contacts, the system
will wait until the generators can support ATS critical load plus ATS
1 load before any permissive will close, even if the generators can
support the settings of ATS 2 or ATS 3 loads.
3.4.5 ATS TRANSFER DELAY
The number of seconds entered in this box represents the delay
time before a permissive will activate. This delay acts on all
permissive outputs, ATS 1, ATS 2 and ATS 3. For example, if the
value is set to 15 seconds, then as soon as the PM-SC determines
it should activate the permissive 1 output, it starts the timer and
waits 15 seconds before activation. Then, when ready to activate
permissive 2, it waits another 15 seconds, etc. If no delay is
wanted set the delay time to zero.
3.4.6 GENERATORS OUT OF SERVICE
Checking any box Gen1 through 10 tells the system that the
checked generator(s) has been intentionally taken out of service
(for example, for maintenance). The PM-SC will then not expect
that generator to start during a two-wire start sequence.
3.4.7 SPECIAL ATS OPERATION
This box will enable the special operation to allow an MPS system
to run with one ATS load transfer switch. When the box is checked,
load shed is automatically enabled by Genlink. The ATS Transfer
Delay field will be set to 1 second if it is set to 0 before selecting
the special ATS mode. The delay must be 1 second or greater in
the special mode. The ATS Load fields will display 0. This should
not be changed. Select Load sheds as you would normally do for
MPS. In this mode, if 1 or more units fails to start, the load sheds
will activate after the ATS transfer delay timer expires followed by
the ATS permissive 5 seconds later. Then the ATS permissive will
stay active allowing the generator to connect to the bus after being
restarted once the fault is cleared. The load sheds can be manually
reset after the unit is back online.
3.5
PRODUCING AND PRINTING
REPORTS
A report screen is displayed when the “REPORT” button is clicked.
Clicking on the printer icon can print this, or it can be printed to
disk via the envelope icon.
3.6 SETTING THE TIME & DATE
To change the time and date stored in the PM-SC, click on the time
and date displayed on the main screen. The screen in Figure 3.6
allows setting the time and date into the PM-SC. It displays the
unit’s currently set time and date. This is the same as the time and
date displayed on the front panel of the PM-SC control box.
Figure 3.6 — Setting Time & Date
3.7
COMMUNICATIONS – PM-SC
TO GENERATORS
The PM-SC communicates to the generators via a dedicated
RS485 port using the industry standard Modbus RTU protocol.
Up to ten generators can be connected to the PM-SC using the
same two wire serial bus. The PM-SC uses this bus to monitor
the status of the generators and to start and stop the units. The
PM-SC module will also relay requests from GenLink to individual
generators via this bus.
Operation
Summary of Contents for PowerManager 004975-2
Page 25: ...23 Notes...
Page 26: ...24 Notes...
Page 27: ...25 Notes...
Page 28: ...26 Installation Diagrams NEMA 1 Drawing No 0E7619 C...
Page 29: ...27 NEMA 1 Drawing No 0E7619 C Installation Diagrams...
Page 30: ...28 Installation Diagrams NEMA 3R Drawing No 0H3175 A...
Page 31: ...29 NEMA 3R Drawing No 0H3175 A Installation Diagrams...
Page 33: ......
Page 34: ......
Page 35: ......
Page 36: ......
Page 37: ......
Page 38: ......
Page 39: ......
Page 40: ......
Page 41: ......
Page 42: ......
Page 43: ......
Page 44: ......
Page 45: ......
Page 47: ......
Page 48: ......