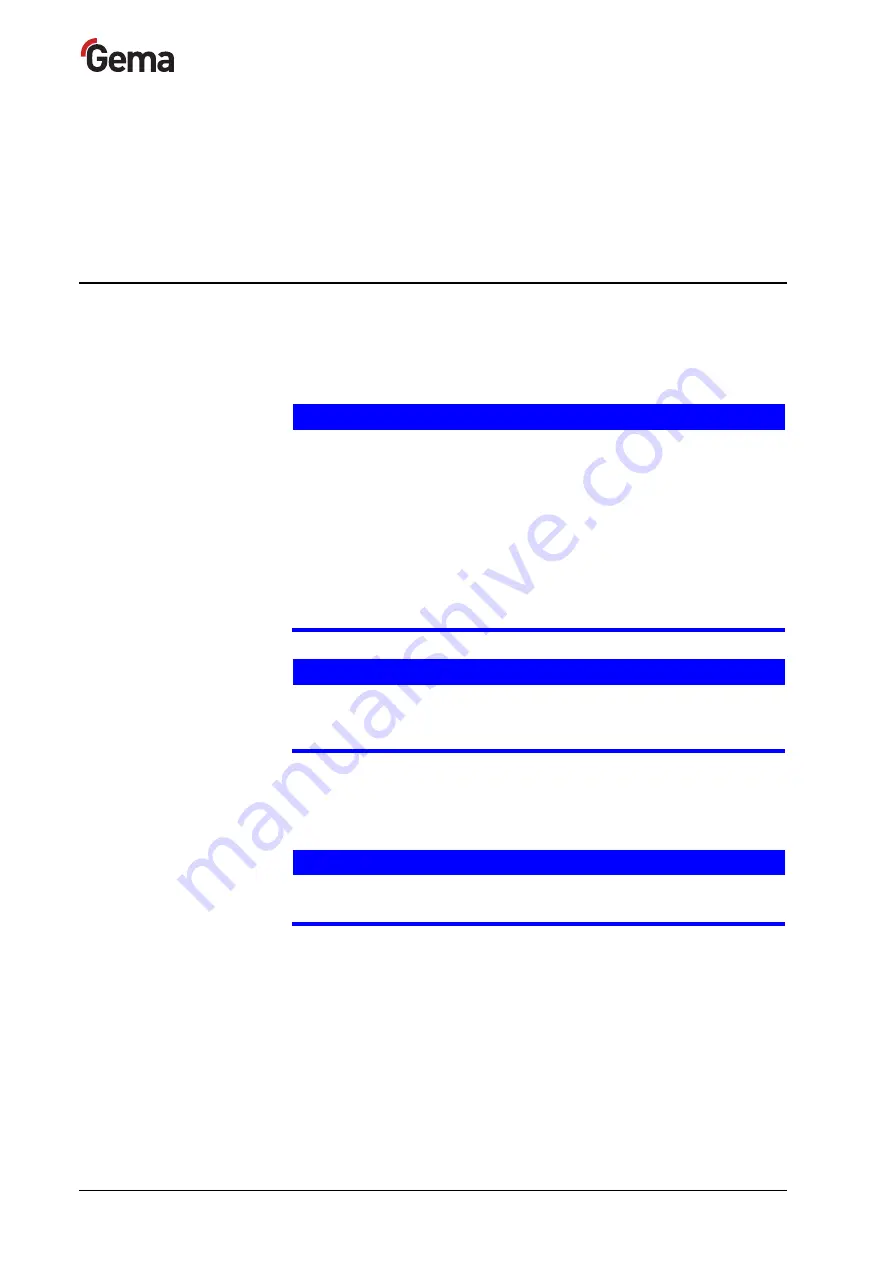
Rev. 00 02/17
24
•
Maintenance / Repairs
HFF01
Pressurized pneumatics system
The pressurized pneumatics system may trigger dangerous situations.
1.
Disconnect the compressed air supply before working on the
pneumatics system.
2.
Depressurize the pneumatics system.
3.
Secure the compressed air supply against reactivation.
Cleaning
The powder hopper and (optional) accessories must be cleaned daily.
Cleaning / Sterilization can be carried out by means of hot water or
steam.
ATTENTION
Container components may be damaged during the cleaning
process.
Observe the operating temperatures.
►
Cleaning the system with the gaskets but WITHOUT A FLUID
PLATE, the operating temperature may not exceed 125°C!
►
Remove all gaskets when cleaning/sterilizing at temperatures
above 125°C!
►
Clean individual parts with compressed air and, if required,
dissolve any sintering on metal parts with cellulose thinners.
►
Do not scratch the surfaces!
ATTENTION
Damage to O-rings when using impermissible cleaning agents
►
Only use elasto-compatible cleaning agents! Refer to chapter on
"Material declaration" on Page 39.
Cleaning intensity depends of the powder used. For optimal cleaning /
sterilization results, we recommend dismantling the entire powder hopper
into its dismantle components.
ATTENTION
Hopper components may be damaged during the cleaning process.
– Please dismantle carefully to avoid damages!
Summary of Contents for HFF01
Page 12: ...Rev 00 02 17 12 Product description HFF01 ...
Page 14: ...Rev 00 02 17 14 Assembly Connection HFF01 ...
Page 20: ...Rev 00 02 17 20 Operation HFF01 ...
Page 26: ...Rev 00 02 17 26 Maintenance Repairs HFF01 ...
Page 30: ...Rev 00 02 17 30 Disposal HFF01 ...
Page 33: ...Rev 00 02 17 HFF01 Spare parts list 33 HFF01 Spare parts Fig 3 ...
Page 35: ...Rev 00 02 17 HFF01 Spare parts list 35 Agitator unit Fig 4 ...
Page 37: ...Rev 00 02 17 HFF01 Spare parts list 37 Agitator drive ...
Page 38: ...Rev 00 02 17 38 Spare parts list HFF01 ...
Page 42: ...Rev 00 ...