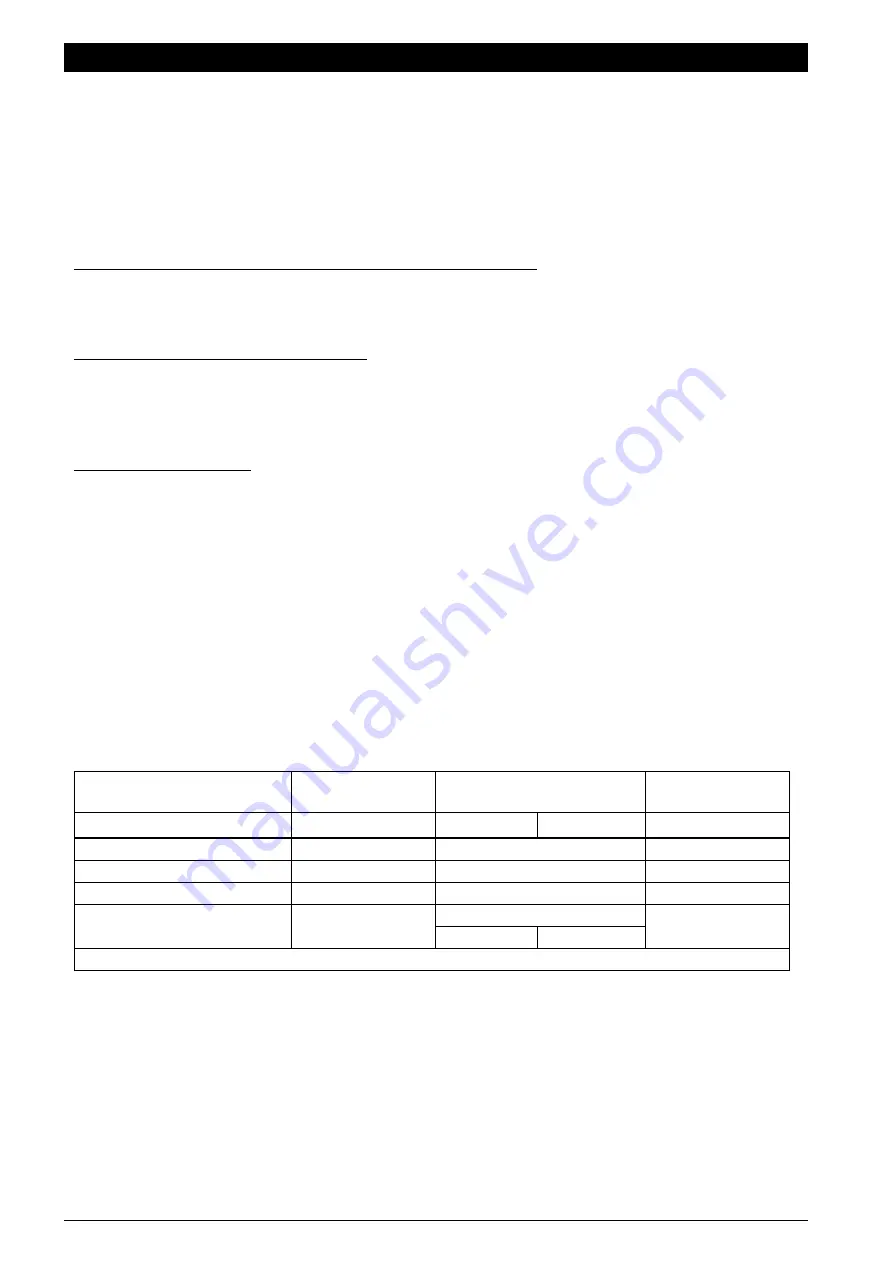
6
85198A_Manual of Electrical Installation for Pressure Probes KH-SIL2-Mobyle-series_07-2019_ENG
5. Safety (content according to IEC/EN 62061 paragraph 7)
Restrictions on use
The device in order to remain compliant with the designated category should be used only as indicated in these instruc-
tions and as required in the operating manual concerning mechanical installation, electrical connection, environmental
conditions and usage limits.
The sensors must be powered with non-distributed networks and always at lengths of less than 30 mt.
Maintenance and periodic inspections
Periodic maintenance to carry-out in order to guarantee the justified exclusion of failures are:
- Visual inspection of the status of the electrical and mechanical connections.
The maintenance is designed to evaluate possible problems due to situations of incorrect mounting endured over time
or particular aggressiveness of the material processed.
Frequency: every two years
Check obstruction of the channel under pressure
- The maintenance has the purpose to verify that there are no occlusion of the pressure channel, which would lead to
malfunctioning.
The inspection is visual, after removing the probe from the process seat.
Frequency: every year.
Testing the sensor calibration
- The test is intended to check the correctness of the transduction curve of the sensor. It’s done by applying known
pressure points to the transducer and checking the output values of the probe.
Frequency: every four years.
Indication of response time
The response time to the pressure transduction is equal to 1 ms
Indications and alarms
The KH Series pressure sensors in the case of some specific anomalies provide output saturation (positive HIGH or
negative LOW).
The table 1 indicates the detected failures, their effect on the electrical output, and the recovery mode of the device.
Table 1: failures, effects on the outputs
Failure
Current
output
Voltage
output
Ratiometric
FS<= 6V
FS > 6V
Power supply 5V
Power supply cable broken
LOW < 3.8mA
LOW < 0.05 V
LOW < 0.25 V
Sensor not connected
LOW < 3.8mA
LOW < 0.05 V
LOW < 0.25 V
Power supply broken
LOW < 3.8mA
LOW < 0.05 V
LOW < 0.25 V
Broken bridge
*LOW < 3.8mA
*LOW < 0.05 V
*LOW < 0.25 V
*HIGH > 22mA
*HIGH > 7 V
*HIGH > 11.5 V
*HIGH > 4.75 V
(*) variable according to the type of failure