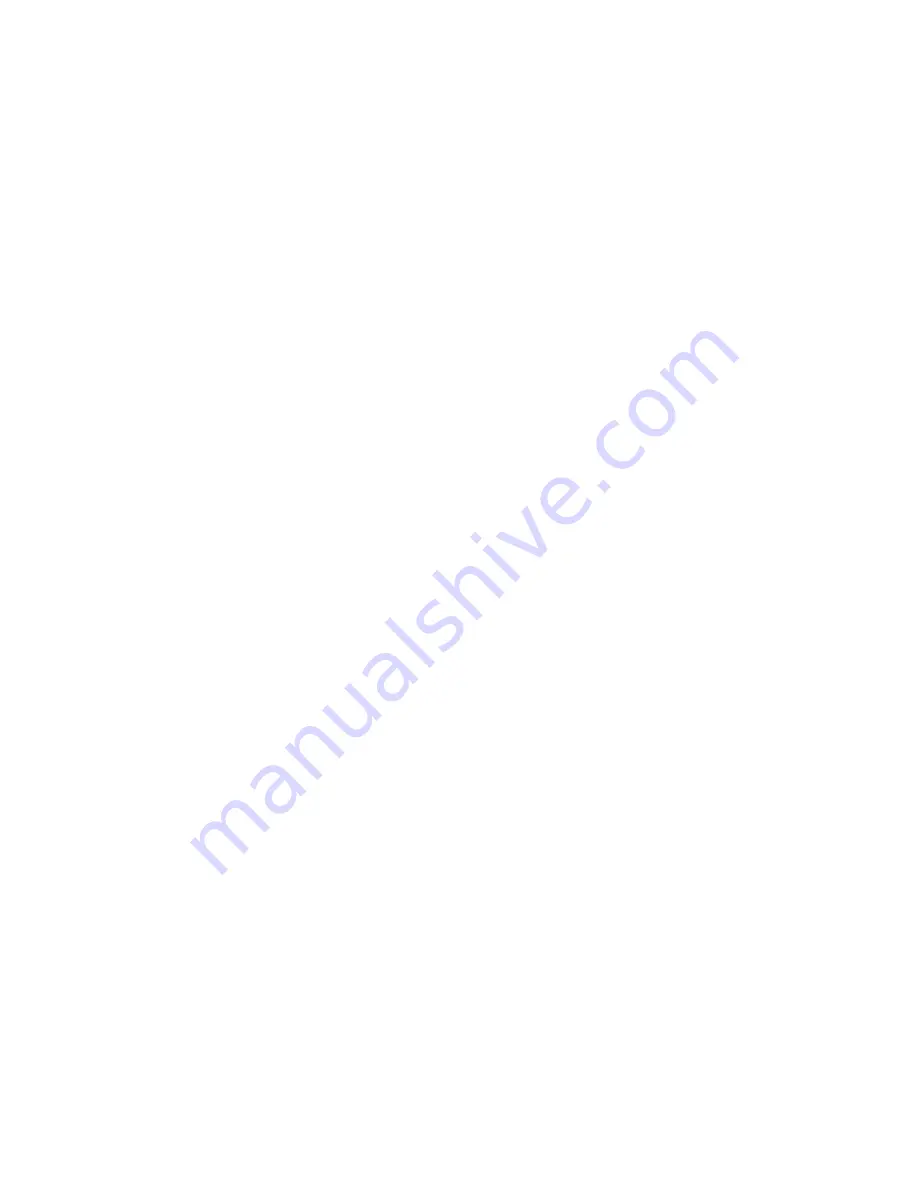
GERC_RLY Rev 2 Wiring and Usage manual
January 9, 2007
2
•
In the event of a fault, indicate which axis caused the fault.
If something bad happens to an axis, I want to know
which
axis. The Gecko gives this
information, via an LED turned on
inside
the case. I want to see it outside the case.
•
Allow an EStop input to disable both the motors (via relays) as well as disabling the
Geckos.
An external EStop
switch
should be a part of every servo system. This
switch
should be
at a minimum a Big Red Button within easy reach. Much better still is a Big Red Button
combined with limit switches on each axis.
When stepper electronics fail, typically the motor refuses to turn. The most common
form of servo electronics failure sends the motor running at maximum speed.
This is the reason for relays. Should the servo electronics fail in such a manner, simply
saying to the Gecko (via pin5) “please stop” will not work, causing extreme badness.
However, for those people who, for whatever reason, choose not to add relays, the
EStop input will also disable the Geckos via pin5.
•
Send a signal to the controlling PC should a fault occur.
The PC may have other apparatus connected to it besides just the servo motors. If
something bad happens, the PC should be informed.
The result of these ruminations were the GERC, a small PCB that did all of the above.
I feel quite strongly that relays should be part of every servo system but found that some
people were put off by the (modest) additional wiring requirements to incorporate them.
Others were somewhat discouraged by the requirement to source and wire a separate 5 volt
power supply.
So a second product was developed, the GERC_RLY. This device is an
All-In-One
version of
the original GERC with relays, protection diodes, dynamic braking resistors and power supply
built in.