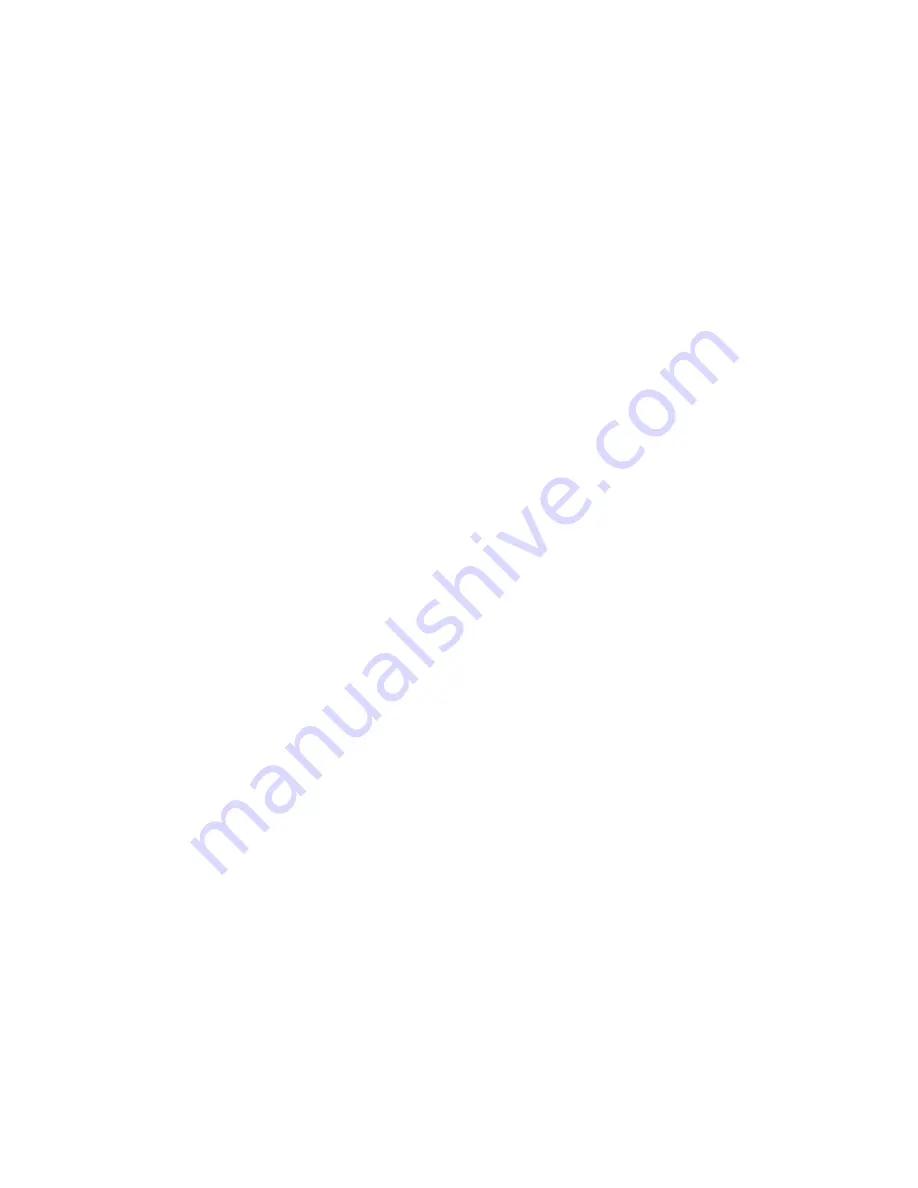
GERC_RLY Rev 2 Wiring and Usage manual
January 9, 2007
1
All the standard legal disclaimers that have ever been written apply to this document.
If you are not completely proficient in electrical wiring and familiar with local
ordinances, you should not proceed.
Design Theory
The Gecko G320 and G340 controllers are fabulous devices, but have one minor little
annoyance - the Error/Reset pin. The operation of this pin is somewhat confusing, and the
usage even more so.
The newest version of the Gecko 3x0 devices ease the use of this pin by allowing a person to
wire all the pins in a system together, but this is still, in my opinion, an incomplete and
inflexible solution.
Looking at the various circuits available from a number of sources, I decided that none of them
precisely suited my needs and so decided to create yet another design. Considering that the
problem was mostly one of
logic
and only partly electronics, I decided to use a microcontroller.
My design goals were these.
•
Automatically provide the 5 second reset required at powerup.
I don’t think, in this day and age of electronics, I should have to stand around and wait
for a light to go off.
•
Fault all the axes should a single
active
axis fault.
If something bad happens such that an axis faults, it’s obviously important to turn
everything off. The part may still be rescued and possible damage to the machine or
tooling is eliminated.
•
Provide a means to disable all the motors without having to resort to a poweroff.
Turning on big power supplies, like those found in servo supplies, puts a strain on many
of the components in the supply. I wanted a means of resetting/disabling things without
the “shock” of simply turning it off.
•
Provide a means to disable a single axis without disturbing the fault detection logic.
Sometimes I like to combine CNC movement with manual adjustment. For example, on
a piece of material of unknown composition, I may manually adjust the Z axis until I’m
confident of the depth of cut.