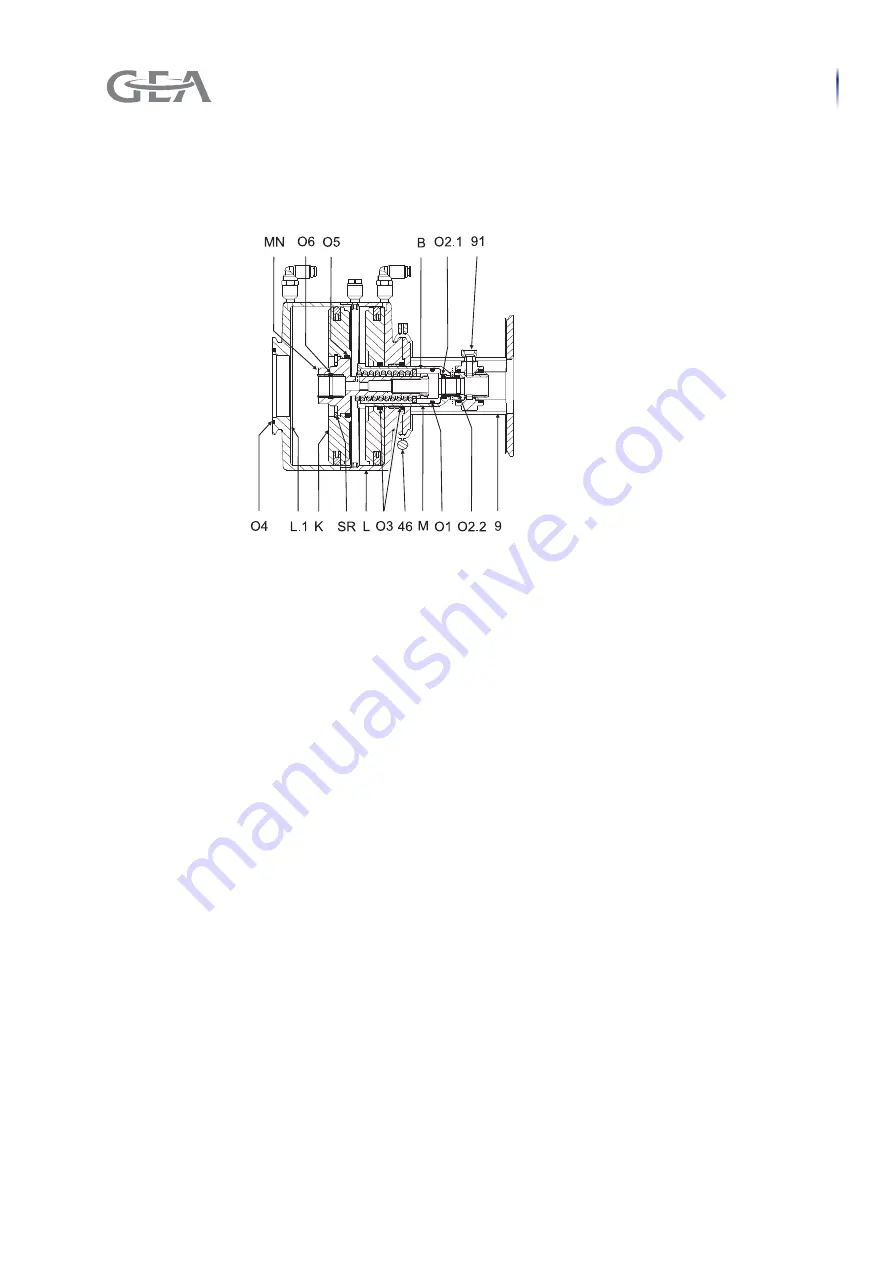
47
Maintenance
Assembling the Valve
Assembling the Valve
Assembling the Lifting Actuator
Carry out the following steps:
1.
Fit O-rings (O3, O4, O5) to the LFT-R lifting actuator (L) and fix it to the lantern (9)
using the hinged clamp (46).
2.
Provide the bushing (B) with O-rings (O1, O2.1) and fit it on the mandrel, part no.
221-105.93, 221-105.94. Place the O-ring (O2.2) on the top and push the assem-
bled parts into the driver sleeve (M).
3.
Push the driver (MN) with the O-ring (O6) into the driver sleeve (M) and pre-tension
using the mandrel (part no. 221-105.76) and a tubular hex. box spanner size 36.
4.
Insert the pre-stressed parts into the lifting actuator (L), fix to the piston (K) with the
snap ring (S) and relieve the tension.
5.
Push the cleaning connection (V9), fitted with O-rings (O1, O2), onto the driver
sleeve (M).
Done