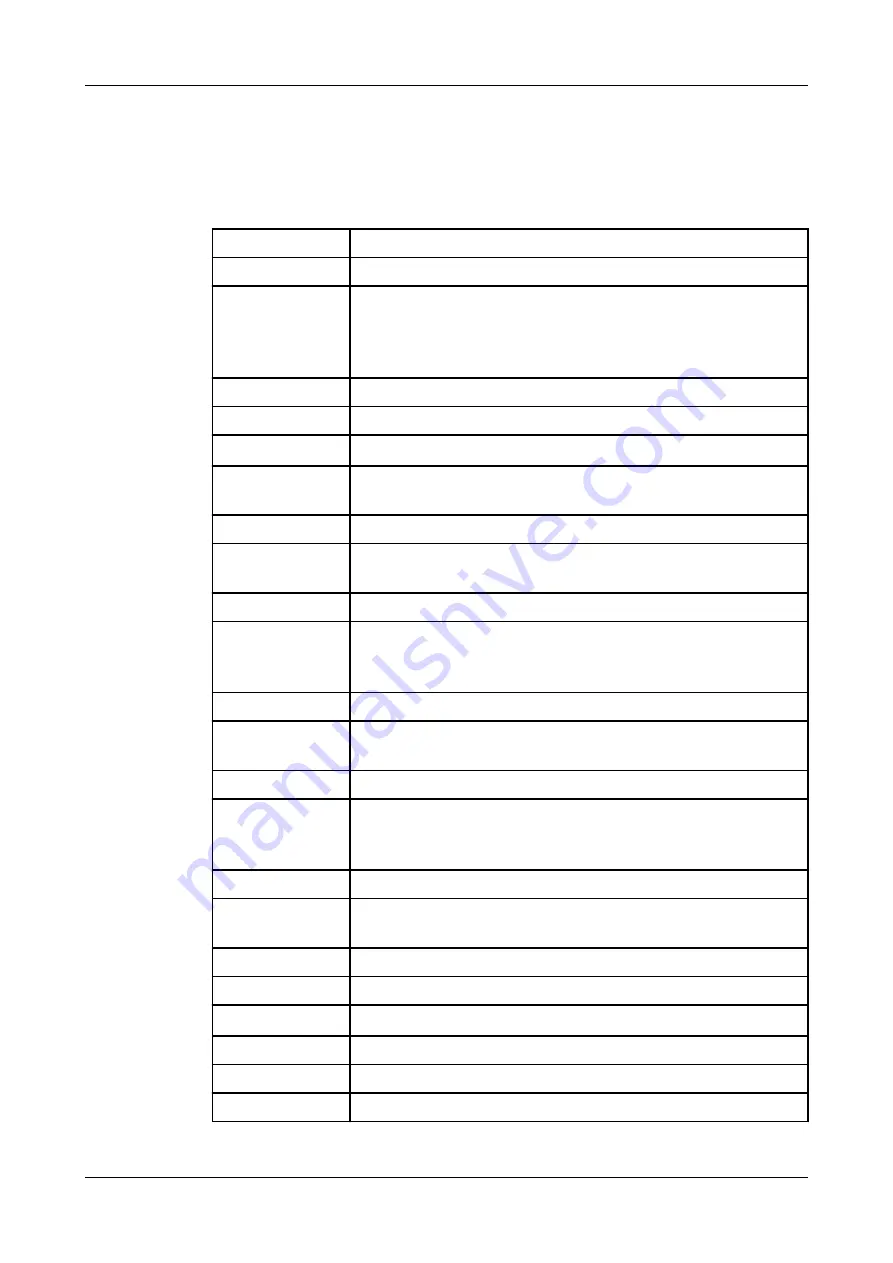
14
Appendix
14.1
Lists
14.2
Abbreviations and terms
Abbreviation
Explanation
BS
British Standard
bar
Unit of measurement of pressure [bar]
All pressure data expressed in [bar/psi] is assumed to be
gauge pressure [barg/psig] unless explicitly specified
otherwise.
approx.
approximately
°C
Unit of measurement of temperature [degree Celsius]
C
v
valve coefficient, non-metric flow coefficient, see K
v
dm
3
n
Unit of measurement of volume [cubic decimetre] standard
volume (standard litres)
DN
DIN nominal width
DIN
German standard issued by DIN (Deutsches Institut für
Normung e.V., German Institute for Standardization)
EN
European Standard
EPDM
Material designation
Short designation according to DIN/ISO 1629: Ethylene
Propylene Diene Rubber
°F
Unit of measurement of temperature [degree Fahrenheit]
FKM
Material designation, short designation according to DIN/ISO
1629: Fluorine rubber
h
Unit of measurement of time [hour]
HNBR
Material designation
Short designation according to DIN/ISO 1629: Hydrogenated
Acrylonitrile Butadiene Rubber
IP
Protection class
ISO
International Standard of the International Organization for
Standardization
kg
Unit of measurement of weight [kilogram]
kN
Unit of measurement of force [kilonewton]
K
v
value
Flow coefficient [m³/s], 1 K
v
= 0.86 × C
v
l
Unit of measurement of volume [litre]
max.
maximum
mm
Unit of measurement of length [millimetre]
Appendix
Lists
430BAL008583EN_1
12.08.2019
45
Summary of Contents for VARIVENT Series
Page 47: ...Appendix 430BAL008583EN_1 12 08 2019 47...
Page 48: ......