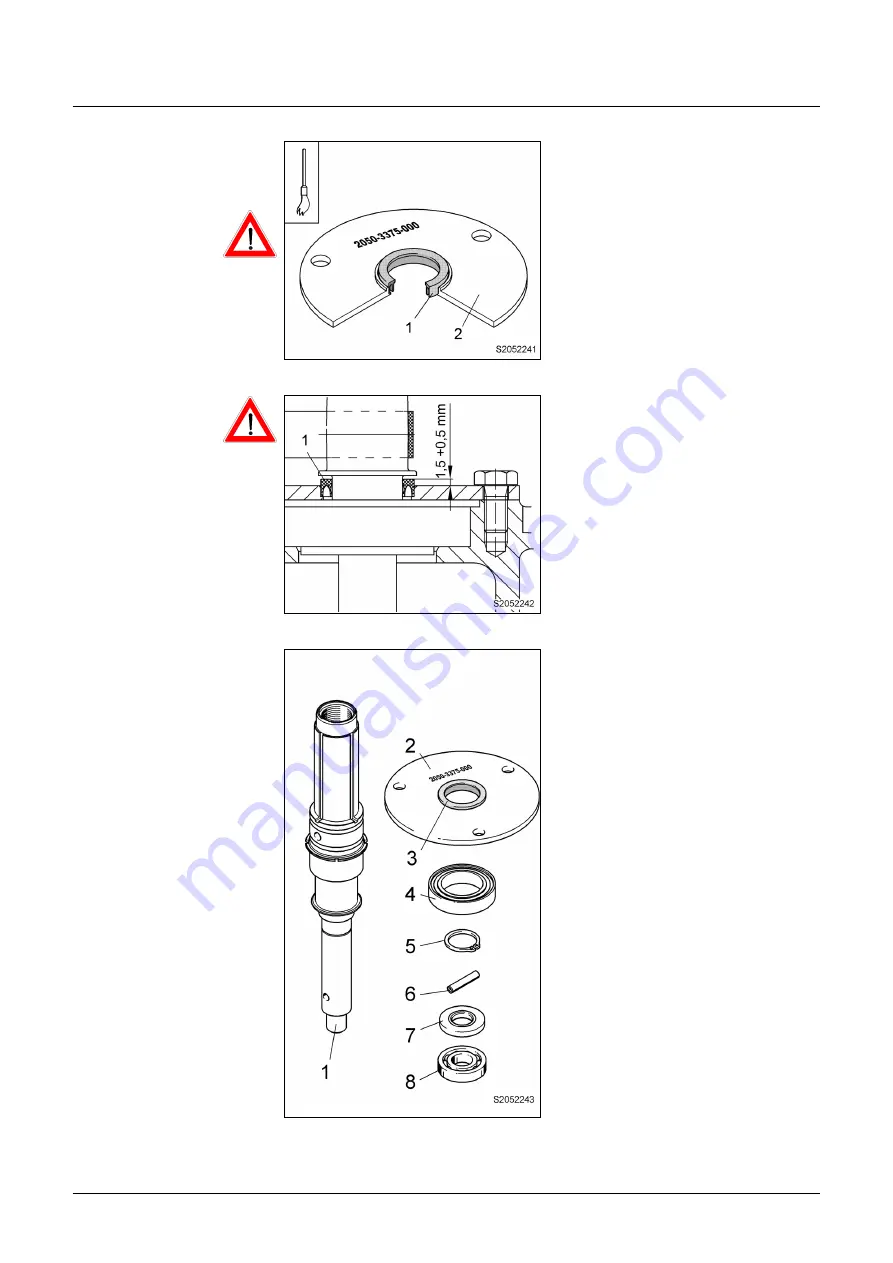
Westfalia Separator
112
Mineraloil Systems GmbH
2051-9001-010
/
1205
Fig. 196
•
Grease radial packing ring 1 as per
lubrication schedule .
•
Fit radial packing ring 1 in bearing
cover 2.
The part-no. of the bearing cover
must face upwards!
•
Drive radial packing ring 1 evenly
into bearing cover 2 by lightly ham-
mering with a mallet.
Fig. 197
•
The fitted radial packing ring 1 must
protrude above the surface of the
bearing cover by
1.5
+0.5 mm
.
Fig. 198
•
Assemble spindle 1:
–
Bearing cover 2 with radial pack-
ing ring 3
–
Grooved ball bearing 4
–
Retaining ring 5
–
Dowel pin 6
–
ball bearing protection ring 7
–
Grooved ball bearing 8
Summary of Contents for OTC 3-02-137
Page 8: ...Westfalia Separator 8 Mineraloil Systems GmbH 2051 9001 010 1205 ...
Page 38: ...Westfalia Separator 38 Mineraloil Systems GmbH 2051 9001 010 1205 ...
Page 48: ...Westfalia Separator 48 Mineraloil Systems GmbH 2051 9001 010 1205 ...
Page 136: ...Westfalia Separator 136 Mineraloil Systems GmbH 2051 9001 010 1205 ...
Page 148: ...Westfalia Separator 148 Mineraloil Systems GmbH 2051 9001 010 1205 ...
Page 150: ...Westfalia Separator 150 Mineraloil Systems GmbH 2051 9001 010 1205 Fig 278 ...
Page 152: ...Westfalia Separator 152 Mineraloil Systems GmbH 2051 9001 010 1205 Fig 279 ...
Page 154: ...Westfalia Separator 154 Mineraloil Systems GmbH 2051 9001 010 1205 Fig 280 ...
Page 157: ...Westfalia Separator Mineraloil Systems GmbH 157 2051 9001 010 1205 ...
Page 158: ...Westfalia Separator 158 Mineraloil Systems GmbH 2051 9001 010 1205 Fig 282 ...
Page 160: ...Westfalia Separator 160 Mineraloil Systems GmbH 2051 9001 010 1205 Fig 283 ...
Page 162: ...Westfalia Separator 162 Mineraloil Systems GmbH 2051 9001 010 1205 Fig 284 ...
Page 164: ...Westfalia Separator 164 Mineraloil Systems GmbH 2051 9001 010 1205 ...
Page 166: ...Westfalia Separator 166 Mineraloil Systems GmbH 2051 9001 010 1205 Fig 286 ...
Page 168: ...Westfalia Separator 168 Mineraloil Systems GmbH 2051 9001 010 1205 Fig 287 ...
Page 170: ...Westfalia Separator 170 Mineraloil Systems GmbH 2051 9001 010 1205 Fig 288 ...
Page 172: ...Westfalia Separator 172 Mineraloil Systems GmbH 2051 9001 010 1205 Fig 289 ...
Page 177: ...Westfalia Separator Mineraloil Systems GmbH 177 2051 9001 010 1205 ...
Page 180: ...Westfalia Separator 180 Mineraloil Systems GmbH 2051 9001 010 1205 ...
Page 181: ...Westfalia Separator Mineraloil Systems GmbH 181 2051 9001 010 1205 ...