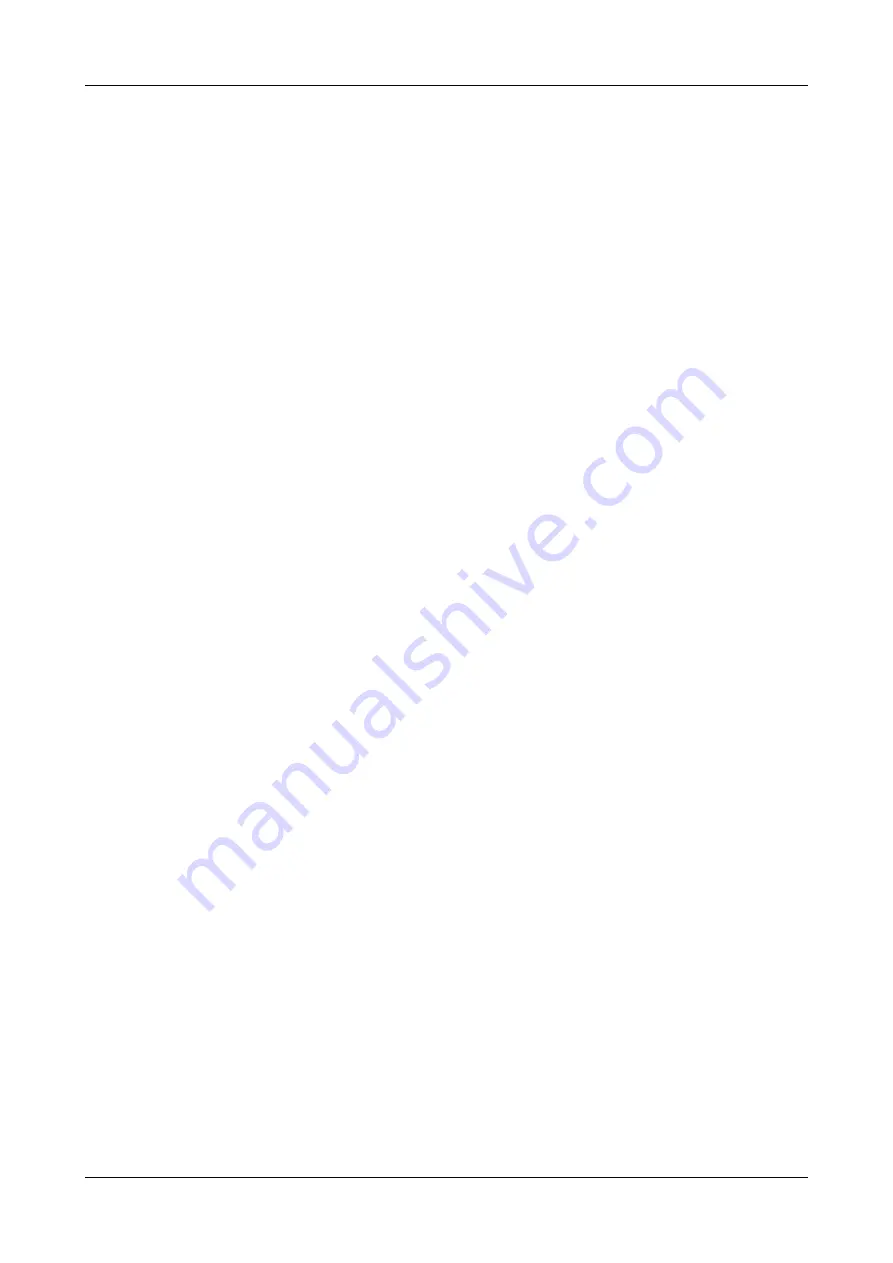
PREFACE
General
1.
All documentation can be downloaded via our web site.
2.
GEA technical manuals includes “generic paragraphs”; this means that
it can
occur
that not all data as described is relevant for the current compressor
series as mentioned in this manual. (For instance, not all compressor series
are suitable for all mentioned refrigerants or not all compressor series
includes two-stage compressors)
Directives
Equipment is based on Pressure Equipment Directive (PED 2014/68/EU)
regulations and according to Machine Directive (MD 2006/42/EG) regulations.
The applied standards are:
NEN-EN-IEC 60204, NEN-EN-ISO 12100, NEN-EN-ISO 13857, NEN-EN 378
0089288_imm_v_english_19
07.04.2021
5