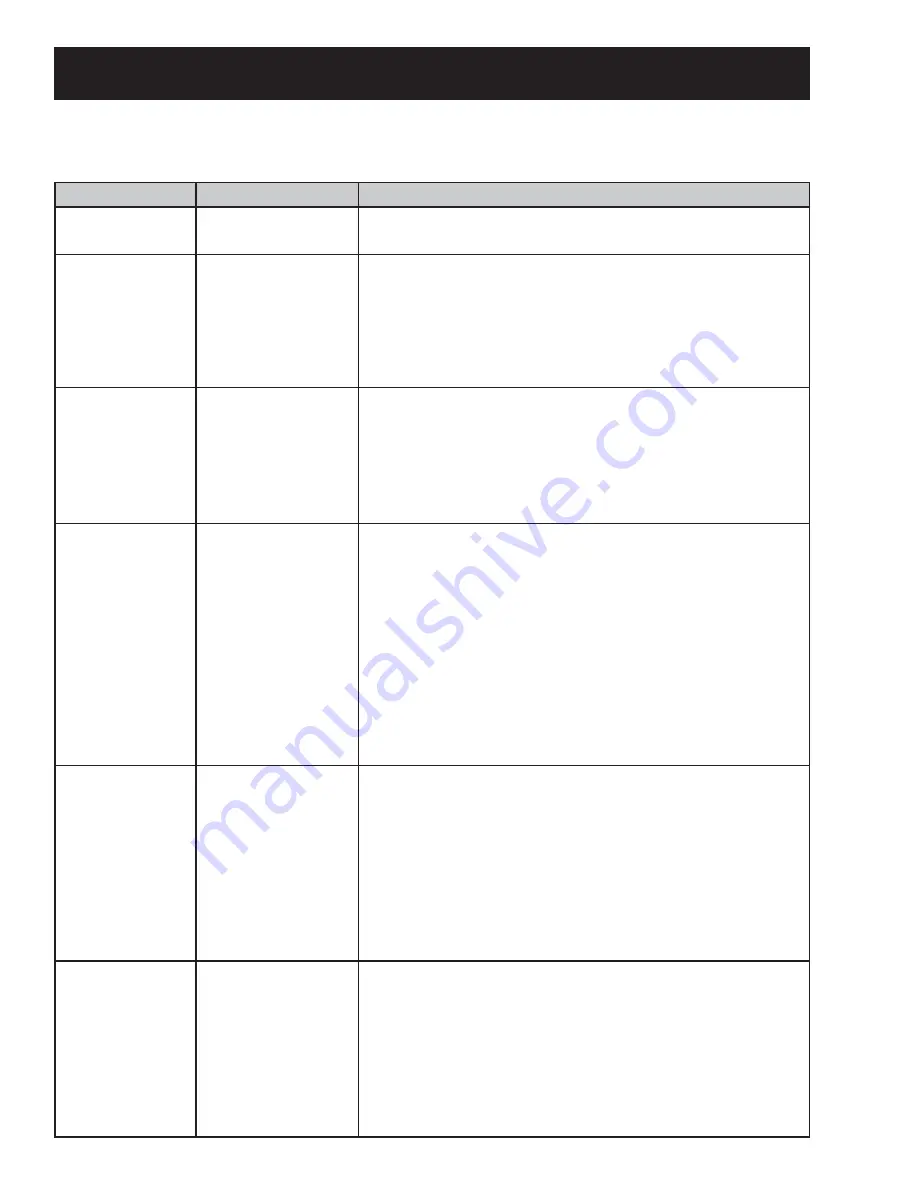
– 62 –
Error Codes
(Continued Next Page)
Error Code
Description
Action
E1 UI EEPROM
E2 Power EEPROM
Internal problem with
UI or MC board
• Replace board as necessary.
E4 Thermistor
Short
E5 Thermistor
Open
Water Temperature
Sensor Problem
• Check integrity of wiring and connections between main
control and Thermistor Assembly.
• Using ohmmeter, measure Thermistor resistance. If outside
expected range, replace Thermistor Assembly.
IF ABOVE STEPS DO NOT CLEAR THE PROBLEM:
• Replace the main control.
E6 Pressure
Switch
Water Level Sensor
Problem
• Check integrity of wiring and connections between main
control and Water Level Sensor.
• Check integrity of Water Level Sensor; replace if necessary.
• Check drain system.
IF ABOVE STEPS DO NOT CLEAR THE PROBLEM:
• Replace the main control.
E7 Slow Fill
Fill Problem
• Ensure manual water valves are fully open.
• Check if water strainers on solenoid valve assembly are
clogged.
• Check for obstructions inside inlet water hoses.
• Ensure solenoid valves do not leak when the valves are de-
energized and the washer is powered down.
• Measure coil resistance for both valves. If outside range
(1000–1250 ohms at room temp), replace solenoid valve
assembly.
IF ABOVE STEPS DO NOT CLEAR THE PROBLEM:
• Replace solenoid valve assembly.
E8 Drain System
Drain Problem
• Ensure pump strainer is clean and free of debris.
• Check for obstruction inside the drain hose.
• Check pump impeller blades and bearing; if evidence of
blade damage or seized bearings are present, replace the
pump.
• Check the electrical connections at the pump motor and
harness.
• Measure pump motor resistance. If outside range (9–14
ohms at room temp), replace the pump.
E9 Dispenser
Motor
Dispenser Problem
• Check for obstruction in dispenser mechanism and
linkages.
• Check the electrical connections at the motor feedback
switch and in the harness.
• Check the electrical connections of water valves in the
harness.
IF ABOVE STEPS DO NOT CLEAR THE PROBLEM:
• Replace dispenser motor assembly.
Note:
It’s important to note error codes should only be used to help identify components which require
testing.
Never replace a part based solely on an error code.
The control can generate a false error if the
right conditions exist. Use the code only as a reference and always check the component before replacing.
Summary of Contents for PFWS4400L0
Page 9: ... 9 Continued Next Page ...
Page 11: ... 11 Continued Next Page ...
Page 13: ... 13 Continued Next Page ...
Page 14: ... 14 Continued Next Page ...
Page 19: ... 19 ...
Page 22: ... 22 Dispenser Drawer Tub Drive Pulley Belt Motor Rear View Front View Con t ...
Page 65: ... 65 Schematics Model 4600 with Steam ...
Page 66: ... 66 Model 4400 without Steam ...