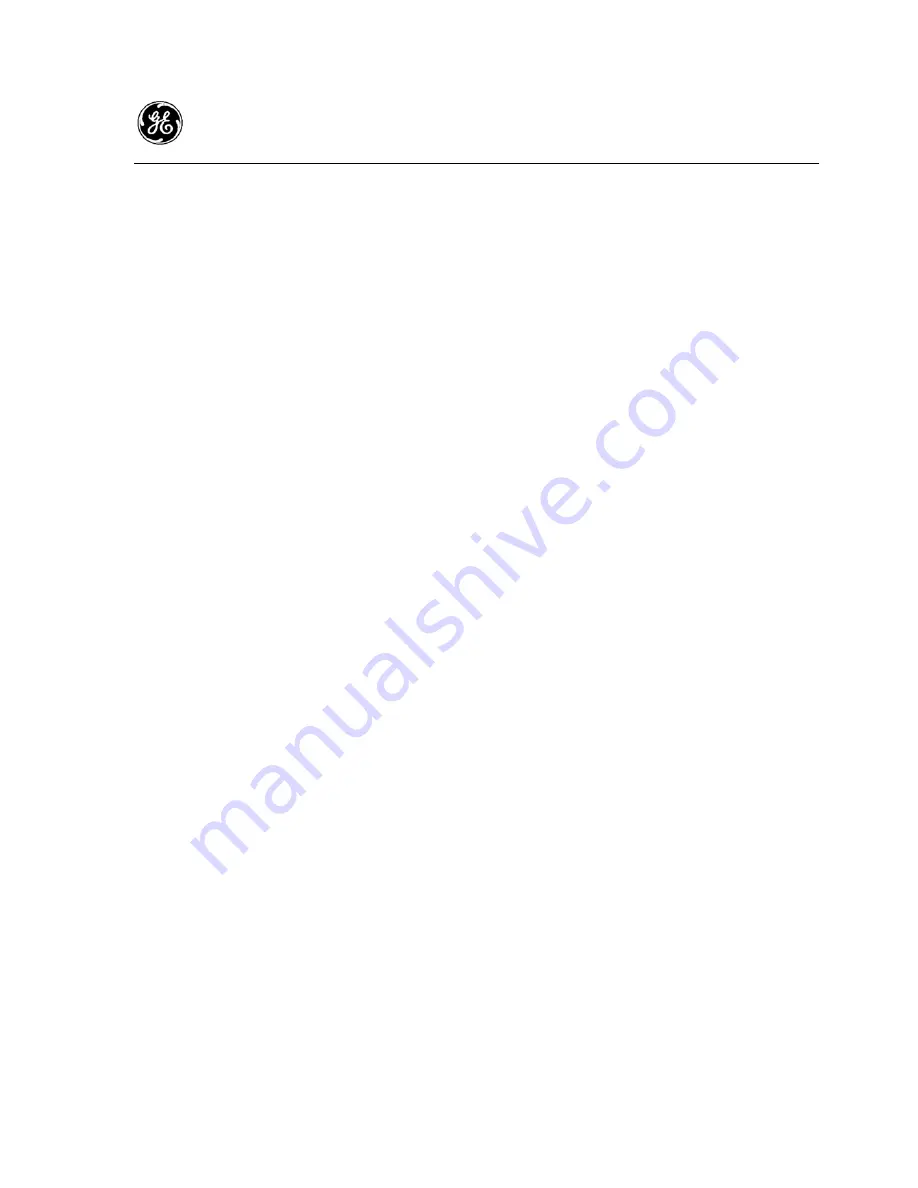
GE Energy Motors GEEP-427-I Copyright 2009, The General Electric Company, USA
41
GEEP-427-I Pegasus, Horizontal Induction Motor
TEWAC, Sleeve Bearing
Maintenance - Top Cover and Heat Exchanger
General
The top cover is described in section entitled
“Machine Description”. Important installation and
operational considerations of the heat exchanger are
covered in section entitled “Air-to-Water Heat
Exchanger” and section entitled “Installation”. It is
recommended that the information in these sections be
reviewed prior to performing top cover and heat
exchanger maintenance.
Maintenance
Maintenance of the top cover and heat exchanger
consists of keeping the inside of the water tubes free of
water contamination and corrosion, keeping the outside
of the tubes free of air contamination, preventing and
correcting any water leaks, preventing mechanical
damage, and checking cooling water pressure, flow,
temperature and quality. The design water flow rate,
maximum temperature and maximum pressure drop are
shown on the nameplate. The heat transfer efficiency of
the heat exchanger is affected by all of the above.
The cooling water entering the heat exchanger
should be at the design flow rate when the water
temperature is at the maximum design temperature on the
nameplate and it should be reasonably clean and free of
chemical contamination to achieve long tube life and
infrequent tube cleaning. If the water flow is less than
design flow at maximum water temperature of exceeds
the maximum temperature requirements on the
nameplate, the machine will operate at a higher than
temperature, which can adversely affect winding
insulation life. Physical and chemical contamination in
the cooling water can cause tube fouling and corrosion,
both of which will affect tube life and cause the unit to
operate at a higher than normal temperature.
For the above reasons, it is recommended that the
tubes be inspected after one month of operation, for
severe conditions, and after three months, for clean
conditions, This frequency of inspection should be
followed for at least two periods following startup
(unless it know that cooling water conditions have
changed). Based upon conditions observed inside the
tubes at the second inspection, the frequency of
inspection may be adjusted accordingly.
When maintaining the top cover and heat
exchanger, first make certain that the machine has been
stopped and that voltage has been removed from all
circuits. Close water valves to the cooler. Drain water
from cooler using the drains and vents provided. (This
can be pre-plumbed at installation to prevent spillage on
machine.) Make certain that all water has drained from
the heat exchanger and then remove the cover pate on
each end of the cooler (each side of the unit) by
removing the bolts which secure them to the water box.
Do not damage the gaskets between the cover and the
water box. The gaskets should be inspected and reused at
reassembly, if suitable. Spare gaskets should be on hand
before any cleaning is attempted in case gaskets are
damaged.
The interior of the tubes may be cleaned by
lancing with a high velocity water jet. For severe tube
fouling, use a rotating, non-metallic bristle brush. Each
individual tube should be inspected and cleaned. Caution
must be taken to make certain that no abrasive tool is
used which might scratch the inside tube surface.
Scratches will tend to promote more severe corrosion and
can result in subsequent tube failure at hat that point.
Inspect the outside of the tubes by removing the
heat exchanger from the top cover. To accomplish this,
remove the screws which secure the heat exchanger to
the top cover and then slide it through the rectangular
openings in the two sides of the top cover. A sling
should be used to support the heat exchanger as it is
pulled out. Inspect the outside of the tubes and fins for
contamination. Unless the environmental conditions are
clean, it is likely that much dirt has accumulated over the
tubes and fins. For any cleaning, exercise care not to
damage the finned surfaces. Use a vacuum hose with an
appropriate plastic wand or tip. Be careful to avoid
damaging fins.
Reassembly procedure is the reverse sequence of
disassembly. A leaking tube may be temporarily repaired
by sealing off at both ends with a non-ferrous plug, in an
emergency. This practice should only be utilized in
emergencies and the total number of tubes which are
plugged can be as much as five percent without seriously
affecting performance. Air-to-water heat exchangers may
be rebuilt with new cores and this should be considered
when more than 5 % of the tubes have been plugged. It is
recommended that rebuilding be done by the original
Summary of Contents for Pegasus MHV GEEP-427-I
Page 46: ...GE Energy Motors 46 ...