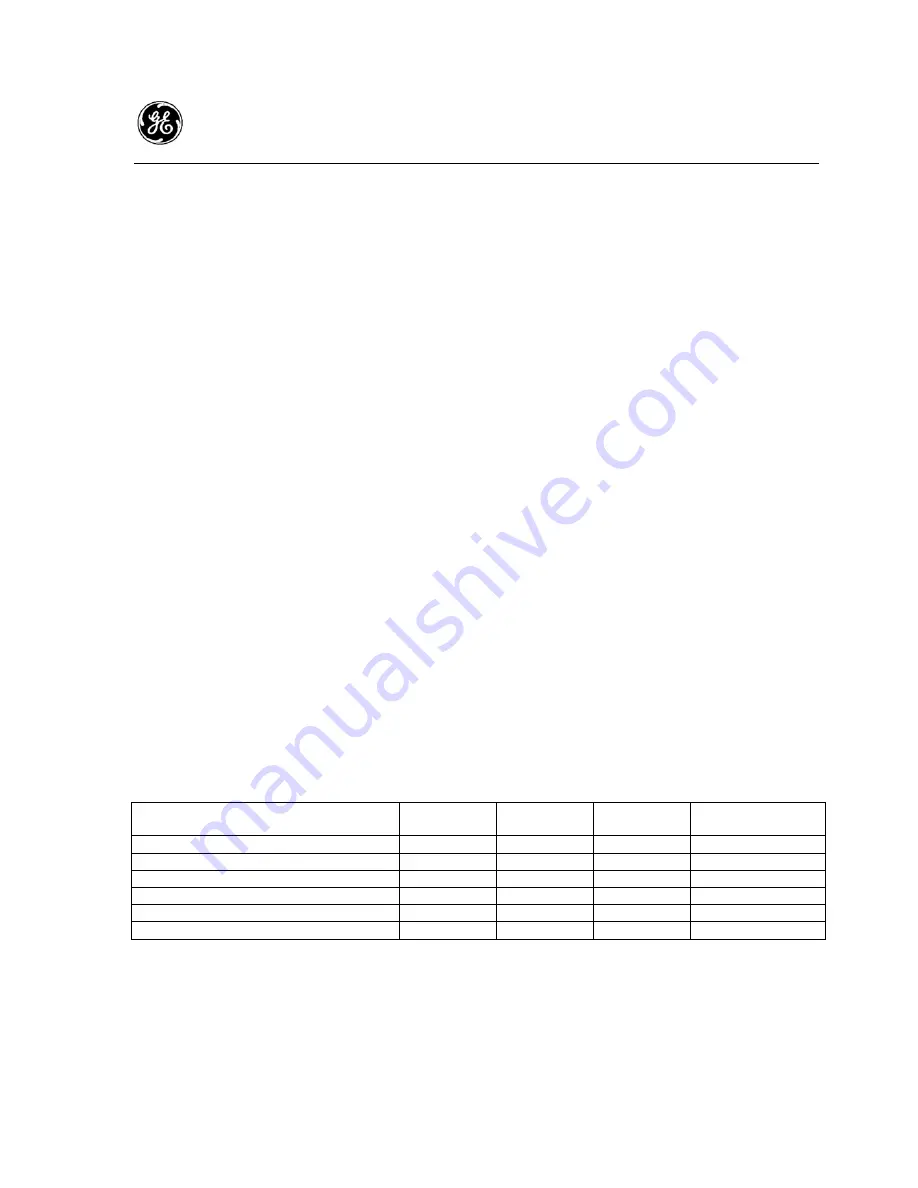
GE Energy Motors GEEP-427-I Copyright 2009, The General Electric Company, USA
25
GEEP-427-I Pegasus, Horizontal Induction Motor
TEWAC, Sleeve Bearing
Maintenance - Lube Oil Recommendation
The successful operation of electric motors and
generators is vitally dependent upon proper lubrication of
the bearings.
The oil used is the responsibility of the purchaser
of the equipment and should be a high grade mineral oil
as recommended for electric motor or generator use by a
reputable oil manufacturer.
While responsibility for recommending a suitable
oil rests with the oil vendor, our experience indicates that
oils having the characteristics as in Table 1 have been
found to be generally suitable for lubrication of both
spring thrust and journal bearings used in General
Electric machines over a wide range of service
conditions. Oils having these characteristics can be
supplied by most major oil companies (refer to Table 2
for cross reference list). The viscosity of the oil depends
on the motor operational speed, bearing type and ambient
temperature. Refer to Table 3 and 4 when specifying the
oil. Table 5 indicates the approximate oil quantity to be
used. Fill the oil reservoir to the proper oil level.
Automotive engine oils should not be used.
It is recommended that oils from different
producers should not be mixed without the approval of
the producers.
Oil change
Change oil at regular intervals.
We recommend to change the mineral oil in case
of selflubricated bearings after approximately 8000
operating hours and in case of an oil supply system
feeding the bearing after 20000 operating hours.
The time between oil changes depends upon the
severity of operating conditions.
Special conditions such as high ambient
temperature, may require more frequent changes. Avoid
operating motor with oxidized oil.
Should unusual changes in the oil (color, smell)
be apparent, the cause must be investigated.
Cleaning
The bearings housings of the motor have settling
chambers into which sediment may collect. These
chambers should be cleaned periodically.
Cleaning may be accomplished by removing the
drain plug located in the bottom of the bearing housing.
The drain oil will carry most of the settled material with
it. Under normal conditions this is the only cleaning
necessary.
Should thorough cleaning of the chamber become
necessary, use a suitable solvent with a petroleum-spirit
base. The solvent should be introduced through the oil-
filter opening at the top of the bearing housing and filled
until the level is approximately at the center of the oil-
level gage. The drain plug should then be removed to
allow the dirty solvent to drain out of the chamber.
After cleaning, reseal the oil-drain plug with an
oil-sealing compound such as alkyd resin compound, No.
3 Permatex or equivalent.
Refill the reservoir with clean oil.
TABLE 1 - TYPICAL CHARACTERISTICS
Characteristic 150
SSU
(ISO VG32)
300 SSU
(IS0 VG68)
450 SSU
(ISO VG 100)
Reference Methods
per ASTM Spec. No.
Kinematic viscosity, cSt AT 104.F
28.8 - 35.2
61.2 - 74.8
90.0 - 110.0
D445
Viscosity Index, Min.
90
90
90
D2270
Flashpoint, F Min.
350
350
360
D92
Pour Point, F Max.
20
25
30
D97
Neutralization Value, Max.
0,20
0,20
0,20
D974
Oxidation Stability Tests, Hrs (*)
2000
2000
1500
D943
*
The life of an oil oxidation test shall be the number of hours required to reach a neutralization value of 2.0
mgKOH/g.
Summary of Contents for Pegasus MHV GEEP-427-I
Page 46: ...GE Energy Motors 46 ...