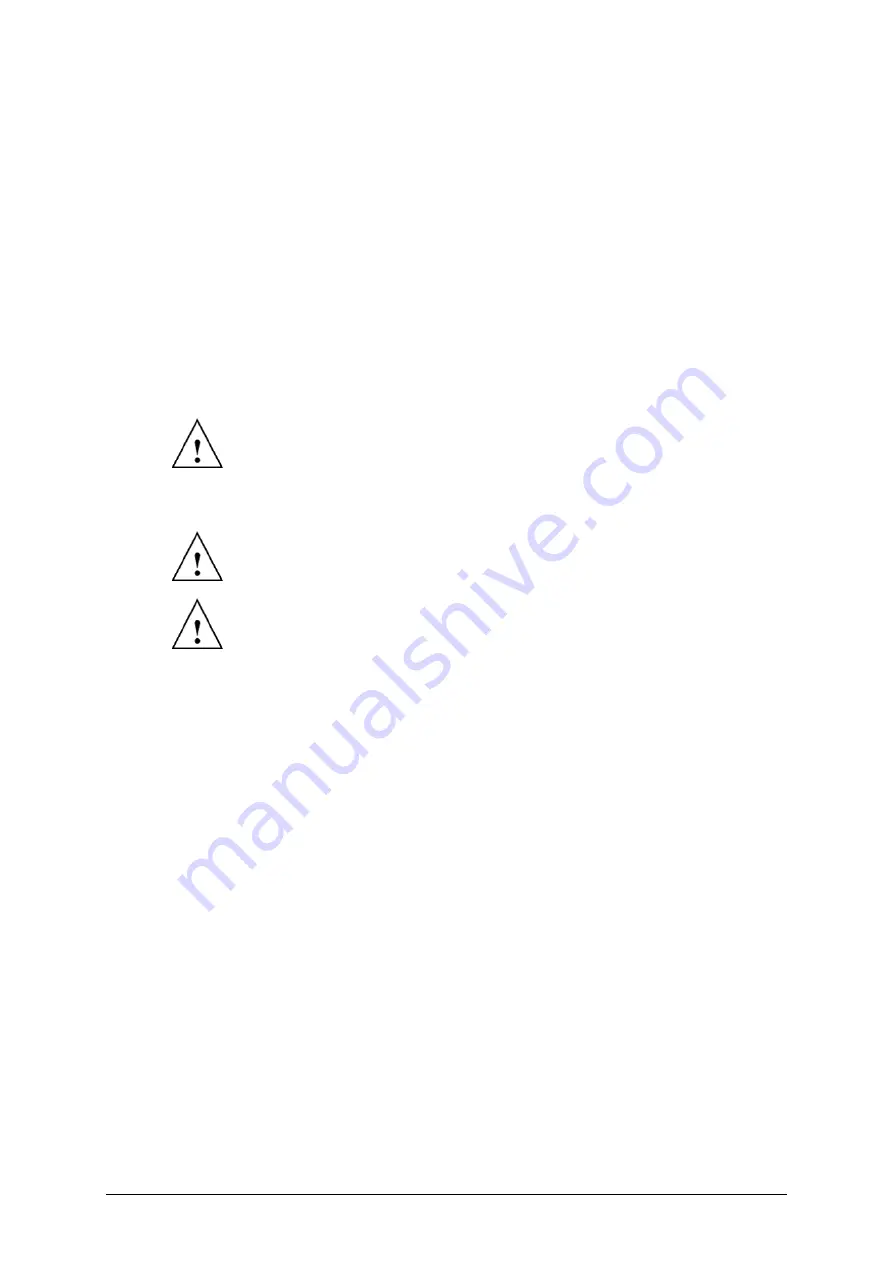
MA-005 - Minitrans Installation Manual - Rev 4.5
13-Aug-20
Page 14 of 86
6
TRANSFORMER CRITERIA
The transformer shall meet the following criteria:
▪
The transformer contains mineral type oils (paraffinic or naphthenic) that meet the
requirements of IEC 60296, BS EN 60296, VDE 0370 or ASTM D 3487.
▪
The transformer oil must be certified PCB free.
▪
The temperature of the oil at the outlet valve of the transformer should not fall below
−
10 °C nor exceed 100 °C.
▪
The transformer oil is at atmospheric pressure or above (see points below).
▪
There are separate return and supply valves available for connection.
▪
The ambient temperature in the area where the product resides should not fall below
−35
°C nor exceed 55 °C.
If the transformer is nitrogen blanketed, check the pressure/vacuum gauge. If
the pressure is positive, then the product can be installed. If the pressure is
negative, a vacuum exists within the transformer. Air will be drawn into the
transformer when a valve is opened. Air bubbles could be damaging to the
transformer if the transformer is energised.
Do not
install the product on an energised transformer that is under vacuum.
Dielectric fittings are a safety measure to prevent circulating currents from
flowing in the tubing circuits whenever a transformer is not grounded to the
same point as the monitoring product. Customers should consult with their
local tubing supplier to source suitable dielectric fittings if required.