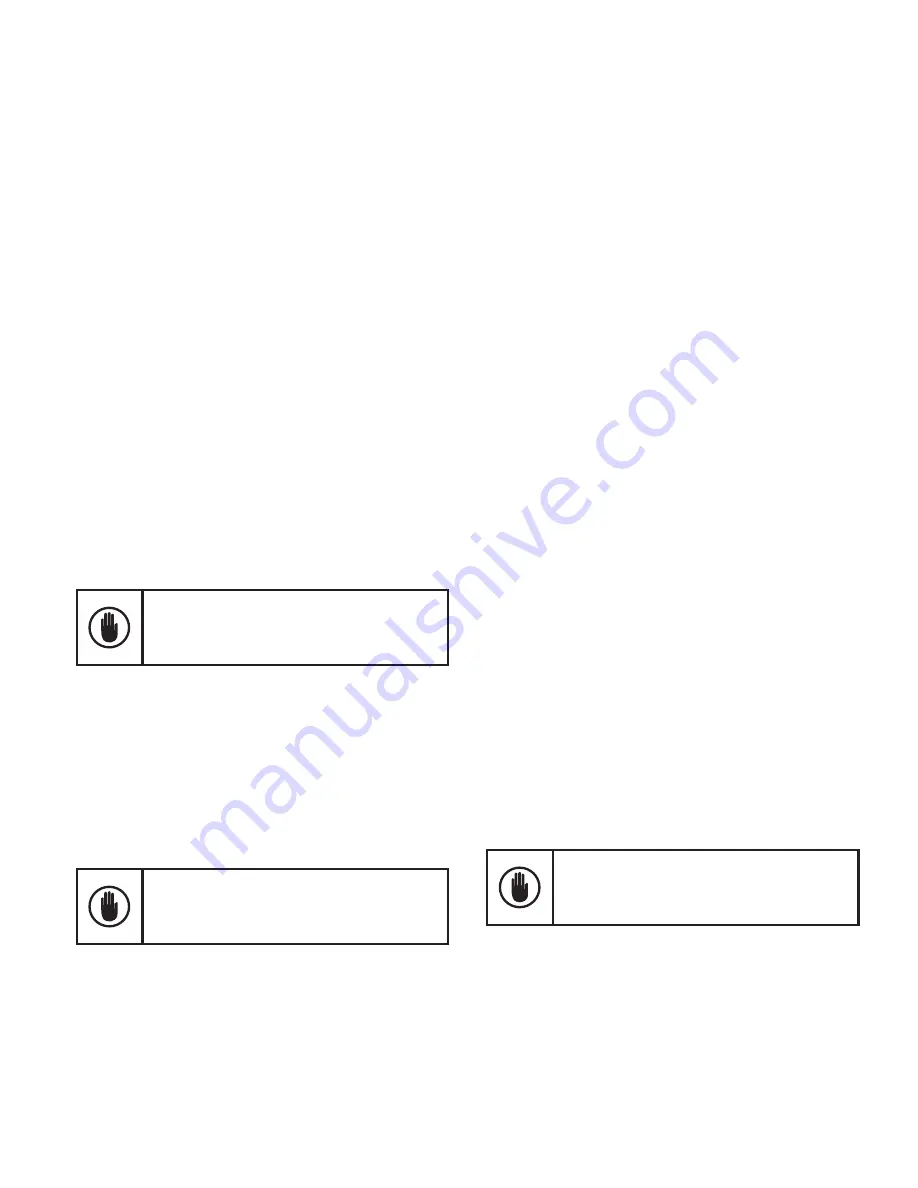
Evolution Series E9000 User Manual
Chapter 4 – Operation
22
Preparing for Initial Operation
In addition to the normal circuit checking after wiring
is completed, the following specific actions should be
taken before energizing the equipment:
1. Check and tighten any electrical connections, such as
lugs and bus splices that may have loosened during
shipment, handling and installation. Torque values are
provided on or adjacent to components or lugs. See torque
labels in MCC vertical wireway door. Visually check
that all latches on Arc Resistant enclosures are engaged.
2. Operate each magnetic device by hand to verify that
all moving parts operate freely. Check all electrical
contacts for proper operation.
3. Current transformers are shipped with a shunt
across the secondary if the circuit is not complete.
Remove the shunt after completing the connections
to the transformer secondary.
4. Verify that the horsepower and voltage rating of the
motor agree with the rating stamped on the starter
unit to which it is connected.
5. Check each overload heater or electronic overload
relay setting against the motor full-load current.
Check current transformer-operated overload
relays to be certain that overload heaters are
in place. Do not operate starters without
overload protection.
6. Check all circuit breaker trip settings and fuse ratings
against the drawings supplied with the equipment.
a. If trip settings must be changed, use the GE rating
plug extractor tool (catalog number TRTOOL) to
remove rating plugs from Spectra circuit breakers.
b. See the startup procedure following information
regarding instantaneous trip settings on magnetic-
only circuit breakers.
Do not exceed the long-time and/or instanta-
neous trip settings stipulated in the National
Electrical Code and as identified in the overload
heater selection tables in this manual.
7. Check all pneumatic or motor-driven timers for
proper time-interval settings.
8. Manually operate all branch-circuit disconnects and
verify proper operation of disconnects and door
interlocks.
9. Where applicable, manually trip all circuit breakers
to verify that operating handles move freely to the
TRIP indicating position. With the door closed and
latched, reset each tripped circuit breaker by pushing
the operating handle down beyond the OFF position.
The operating handle should move upward to the
OFF position after the breaker has been reset. After
the reset, turn the circuit breaker ON and then OFF
to confirm proper operation.
10. Visually check all units and enclosures to ensure
that electrical spacings have not been reduced
because of shipping and handling actions.
11. Verify that the motor control center enclosure and
units are grounded.
12. Replace all protection barriers and panels that have
been removed during installation.
13. Carefully clean the equipment interior with a clean
cloth, soft brush or vacuum cleaner to remove all
metal chips, dust, wire and other debris.
14. After taking precautions to prevent accidental contact
with the motor control center buswork, conduct the
following insulation-resistance test with a 1000 Vdc
(Megger) tester. With all disconnects in the OFF position,
• Apply voltage between all phase pairs.
• Apply voltage between each phase and ground.
All readings should be 1 megohm minimum; typical
values will be 50–100 megohm but may vary based
on humidity.
Similarly, test individual feeder and motor circuit
wiring (field wiring) as each set of conductors is pulled
into the motor control center, before terminating
the conductors at either end.
15. With all disconnects OFF, close and latch all doors
and secure all external covers.
16. For AFM Units, ensure that all visual indicators are
showing “RED” to indicate “ENGAGED” stab position
and “OPEN” shutter position.
Initial Operation of the Motor Control Center
Because of problems that may occur during
the initial energizing of the motor control
equipment, only qualified personnel should
carry out this startup procedure.
Use the following procedure for initial startup of the
motor control equipment. Be sure that the steps in the
previous section, Preparing for Initial Operation, have
been completed.
1. Ensure that all doors are closed and latched and all
external covers on the motor control center are
secured. Visually check that all latches on Arc Resistant
enclosures are engaged.
2. Verify that all main and branch disconnects within
the motor control center are OFF.