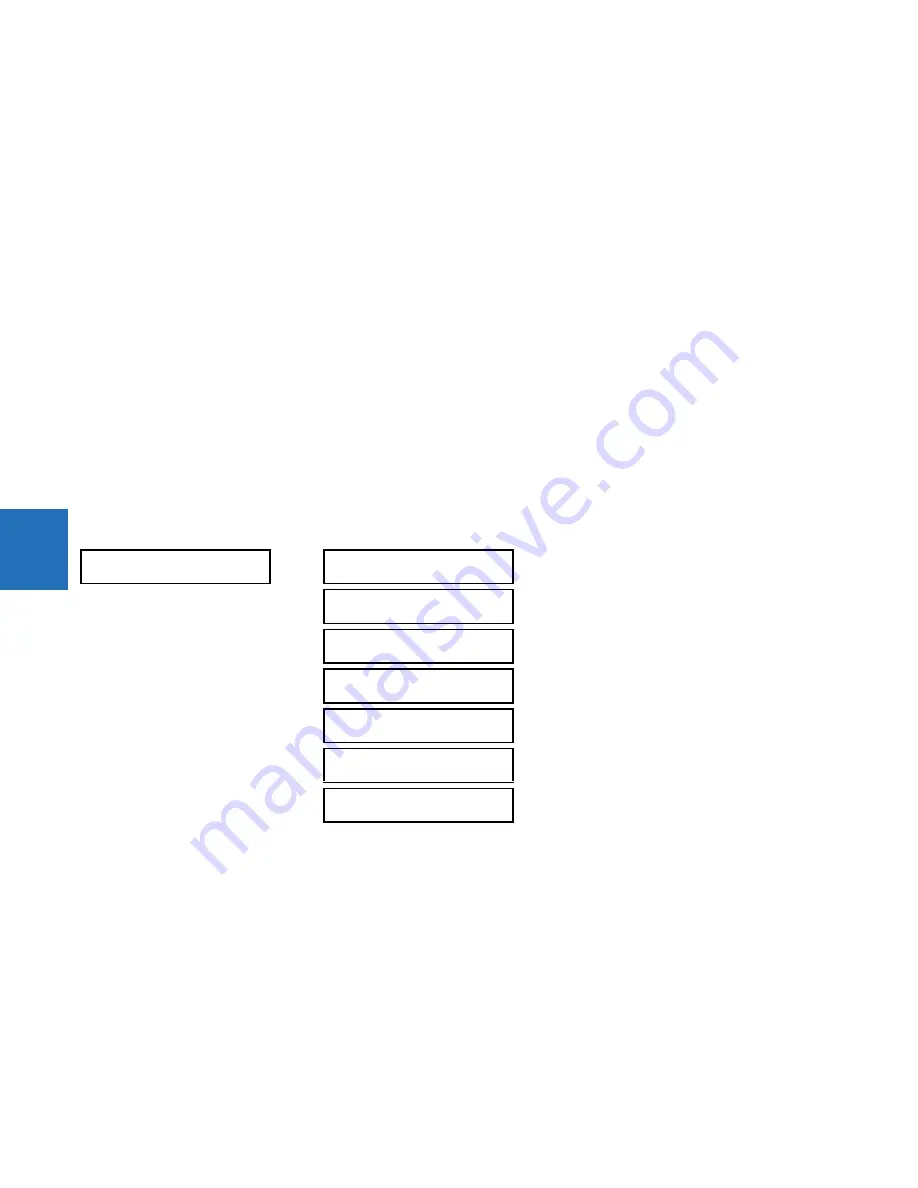
5-114
D30 LINE DISTANCE PROTECTION SYSTEM – INSTRUCTION MANUAL
PRODUCT SETUP
CHAPTER 5: SETTINGS
5
The
FAULT REPORT 1 VT SUBSTITUTION
setting is set to “None” if the relay is fed from wye-connected VTs. If delta-connected
VTs are used, and the relay is supplied with the neutral (3V0) voltage, this setting is set to “V0”. The method is still exact, as
the fault locator combines the line-to-line voltage measurements with the neutral voltage measurement to re-create the
line-to-ground voltages. See the
ACTUAL VALUES
RECORDS
FAULT REPORTS
menu for details. It is required to configure
the delta and neutral voltages under the source indicated as input for the fault report. Also, the relay checks if the auxiliary
signal configured is marked as “Vn” by the user (under VT setup) and inhibits the fault location if the auxiliary signal is
labeled differently.
If the broken-delta neutral voltage is not available to the relay, an approximation is possible by assuming the missing zero-
sequence voltage to be an inverted voltage drop produced by the zero-sequence current and the user-specified
equivalent zero-sequence system impedance behind the relay: V0 = –Z0
×
I0. In order to enable this mode of operation, the
FAULT REPORT 1 VT SUBSTITUTION
setting is set to “I0”.
The
FAULT REP 1 SYSTEM Z0 MAG
and
FAULT REP 1 SYSTEM Z0 ANGLE
settings are used only when the
VT SUBSTITUTION
setting
value is “I0”. The magnitude is to be entered in secondary ohms. This impedance is an average system equivalent behind
the relay. It can be calculated as zero-sequence Thevenin impedance at the local bus with the protected line/feeder
disconnected. The method is accurate only if this setting matches perfectly the actual system impedance during the fault.
If the system exhibits too much variability, this approach is questionable and the fault location results for single-line-to-
ground faults is trusted accordingly. Keep in mind that grounding points in the vicinity of the installation impact the system
zero-sequence impedance (grounded loads, reactors, zig-zag transformers, shunt capacitor banks, and so on).
5.3.9 Oscillography
5.3.9.1 Menu
SETTINGS
PRODUCT SETUP
OSCILLOGRAPHY
Oscillography records contain waveforms captured at the sampling rate as well as other relay data at the point of trigger.
Oscillography records are triggered by a programmable FlexLogic operand. Multiple oscillography records can be captured
simultaneously.
When EnerVista UR Setup creates a new settings file, a Smart defaults feature automatically enters a basic oscillography
configuration. The basic configuration changes the factory default values to make the number of samples per cycle 32,
adds a selection of digital and analog channels that are often of interest, and adds a FlexLogic equation to trigger
oscillography. Review and update this basic configuration as required for the application at hand.
The
NUMBER OF RECORDS
is selectable, but the number of cycles captured in a single record varies considerably based on
other factors, such as sample rate and the number of operational modules. There is a fixed amount of data storage for
oscillography; the more data captured, the less the number of cycles captured per record. See the
ACTUAL VALUES
RECORDS
OSCILLOGRAPHY
menu to view the number of cycles captured per record. The following table provides sample
configurations with corresponding cycles/record. The minimum number of oscillographic records is three.
OSCILLOGRAPHY
NUMBER OF RECORDS:
5
Range: 1 to 64 in steps of 1
TRIGGER MODE:
Automatic Overwrite
Range: Automatic Overwrite, Protected
TRIGGER POSITION:
50%
Range: 0 to 100% in steps of 1
TRIGGER SOURCE:
Off
Range: FlexLogic operand
AC INPUT WAVEFORMS:
16 samples/cycle
Range: Off; 8, 16, 32, 64 samples/cycle
DIGITAL CHANNELS
See below
ANALOG CHANNELS
See below
Summary of Contents for D30 series
Page 10: ...x D30 LINE DISTANCE PROTECTION SYSTEM INSTRUCTION MANUAL TABLE OF CONTENTS ...
Page 534: ...5 324 D30 LINE DISTANCE PROTECTION SYSTEM INSTRUCTION MANUAL TESTING CHAPTER 5 SETTINGS 5 ...
Page 670: ...iv D30 LINE DISTANCE PROTECTION SYSTEM INSTRUCTION MANUAL ABBREVIATIONS ...
Page 686: ...xvi D30 LINE DISTANCE PROTECTION SYSTEM INSTRUCTION MANUAL INDEX ...