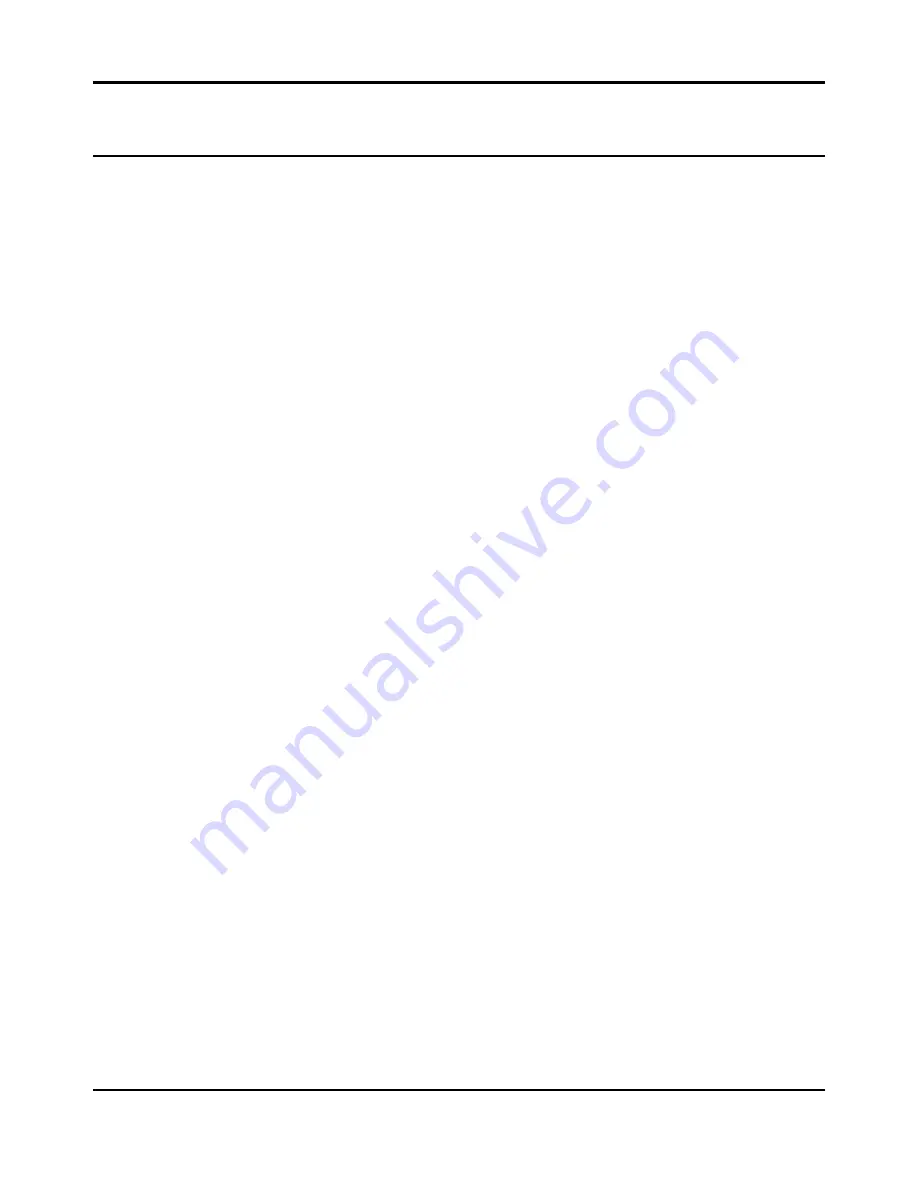
14 mm Proximity Transducer System 7200 Series Installation Manual
4
2. INSTALLATION
2.1 INTRODUCTION
This section covers inspection, storage, and installation of equipment as well as the actual
installation procedures for the probe and Proximitor.
2.2 RECEIVING INSPECTION AND STORAGE
All equipment should be removed from shipping containers and visually inspected to ensure there is
no shipping damage. If shipping damage is apparent, file a claim with the carrier and submit a copy
to Bently Nevada Corporation. Include part and serial numbers on all correspondence. If no
damage is apparent and the equipment is not going to be used immediately, Bently Nevada
Corporation recommends returning the equipment to the shipping container and resealing. The
equipment should be stored in an environment free from potentially damaging conditions such as
high temperature, excessive humidity, or a corrosive atmosphere. See Appendix B for
environmental specifications.
The equipment is durable; however, reasonable handling care should be exercised during
installation. When cable connectors are part of the equipment, they must be properly protected from
physical abuse or contamination by oil, water, or other substances by wrapping them with FEP tape
or another connection protective device.
CAUTION
Do not use adhesive electrical tape; oil mist will dissolve the adhesive
causing connector contamination.
2.3 INSTALLATION CONSIDERATIONS
Bently Nevada probes and Proximitors are calibrated to AISI E4140 series steel. Most AISI 1000
and AISI 4000 Series steel present a response curve similar to the AISI E4140 Series steel.
However, copper, aluminum, brass, tungsten, or other types of metals present a different response
curve. If the metal to be observed has significantly different magnetic and electrical properties than
AISI E4140 steel, follow the recalibration procedure in Section 3. If it is necessary for the probe to
observe a plated area, contact the nearest Bently Nevada Corporation office for assistance.
Proper installation requires the observed surface to be free of irregularities such as hammer marks,
scratches, holes, or keyways. Any type of plating (including chrome) normally results in a
nonuniform plating thickness. Residual magnetism, surface irregularities, and other conditions in
Summary of Contents for Bently Nevada 7200 Series
Page 22: ...APPENDIX A 17 Figure A 1 14 mm Probe Ordering Information ...
Page 24: ...APPENDIX B 19 Figure A 3 14mm Extension Cable Ordering Information ...
Page 34: ...APPENDIX C 29 6 APPENDIX C SCALE FACTORS AND SENSITIVITY CURVES ...
Page 36: ...APPENDIX C 31 Figure C 2 Probe and One Foot Cable at Temperature ...
Page 38: ...APPENDIX C 33 Figure C 4 9 Metres Cable at Temperature ...
Page 42: ...APPENDIX C 37 Figure C 8 Effects of Flat Surface Side Clearance ...