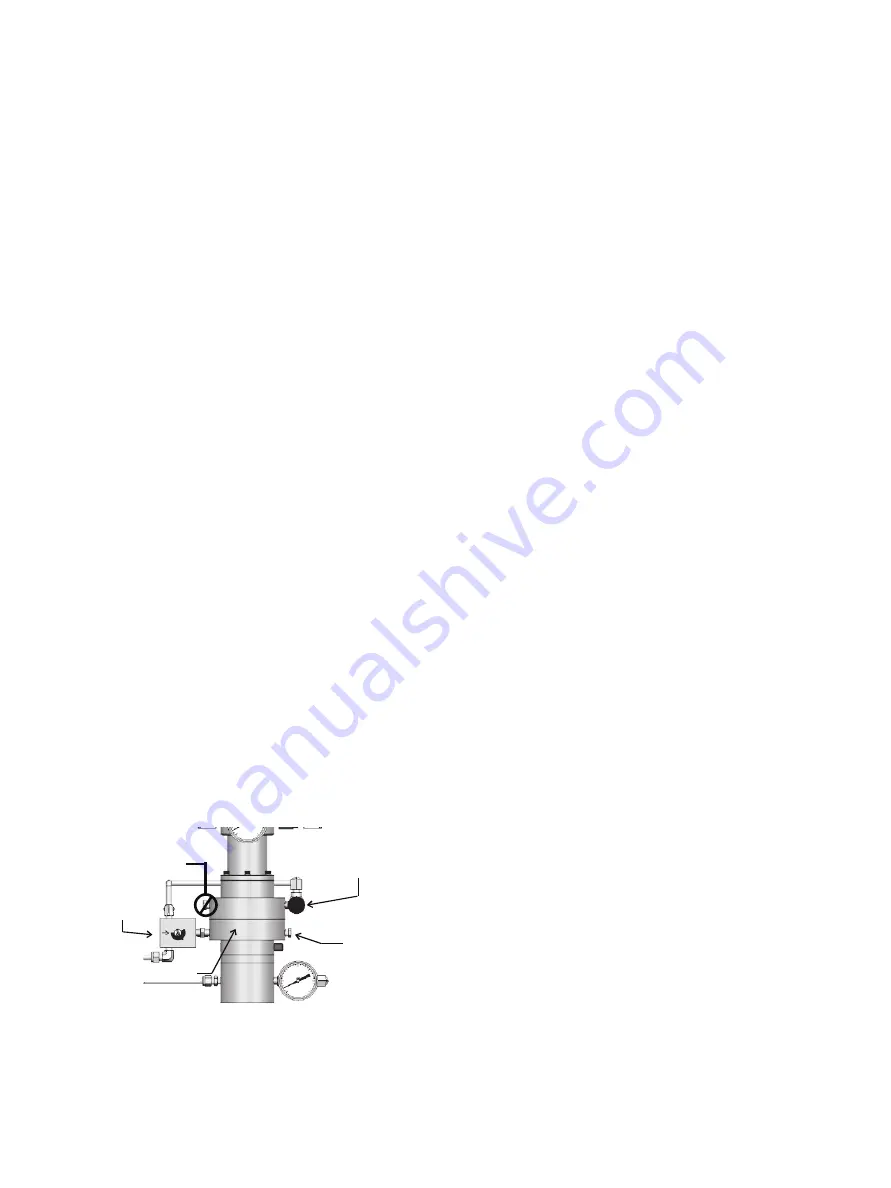
Becker VRP-SB-PID Series Natural Gas Controllers Instruction Manual | 12
© 2016 General Electric Company. All rights reserved.
In either case (reverse or direct acting), a quick response
of the output needle suggests the sensitivity of the PID
still needs tuning.
I. For a direct acting controller, turn the sensitivity drum
to the right until the pressure just increases again. For a
reverse acting controller, turn the sensitivity drum to the left
until the pressure just decreases again.
J. Repeat steps H and I until output pressure is stationary
between atmospheric pressure and maximum power
gas pressure.
K. When the controller output is stationary between atmospheric
and power gas pressure, and the sensitivity drum is adjusted
such that any movement to the right would vent gas, the
controller is approximately at “zero” dead band. “Zero” dead
band is defined when a slow growing bubble (10-30 seconds)
is detected from the exhaust port. Make small adjustments in
adjustment drum until “zero” dead band condition is met.
L. To lock the deadband setting in place, insert the locking
set screw into one of the radial holes in the adjustment
drum. Using a torque wrench, torque to 1-2 inlb. Care
should be taken not to exceed this level, as if the screw is
over-tightened it may affect the calibration of the pilot. If a
torque wrench is not available then torque the screw just
enough so that it provides a light grip on the inner shaft.
Recheck the vent port on the controller.
M. Reconnect all tubing disconnected in step E. Refer to
Table 8 on page 13 for correct derivative orifice and
metering valve settings. Open the measured variable valve.
Open the output block valve in order to begin control and
make fine adjustments.
2. Proportional Band Test
The purpose of this test is to check the proper operation of
the feedback chamber. Leaks, misalignments or wrong internal
parts can cause the PID to not function properly. The output
valve must stay open to allow output pressure to communicate
with the feedback chamber.
For a Direct Acting Controller:
The integral (top) chamber must be at atmospheric pressure.
A. Remove plug from integral chamber and close reset valve
(Figure 7). Tubing between derivative orifice and reset
metering valve should stay connected.
Close reset
valve
Plug
Feedback Module
Derivative
orifice
Remove this
plug
Figure 7 - Proportional Band Test
B. Change the sensing pressure until the output pressure is
approximately 30% away from the power gas. For example,
a VRP-PID- 40 needs the output adjusted to 30 psig, while a
VRP-PID-80 and VRP-PID-125 need outputs of 60 psig and
90 psig respectively.
C. Consult the appropriate table from pages 6-8 depending
on which model PID you have. Look at the left side of the
table for the correct model number. Associate that model
number with the corresponding control spring. Look at
the chart under “Proportional Band” and choose the
corresponding gain configuration of the PID. Look down for
the point where the model and control spring row intersects
with the proportional band/gain configuration column. This
number is the amount of sensing pressure that must be input
in order to see a 12 psig output change for a PID-40, 24 psig
output change for a PID-80, or 30 psig change for a PID-125.
Example of Step C:
VRP-600-SB-PID-40, direct acting, high gain, yellow control spring
1. Turn to page 6 and look in the left hand column to find
VRP-600-SB-PID-40.
2. The second column to the right shows the control spring
range, and the third column reads “yellow control spring,
25- 1306” for the model VRP-600-SB-PID-40.
3. “With Small Ring” for a high gain pilot.
4. Where the rows and columns intersect is “23 psig (159 kPa)”.
5. Take note of the initial sensing pressure and initial output
pressure. Change the sensing pressure 23 psig (159 kPa) from
the initial value. The output gauge should only have changed
12 psig (83 kPa) from its initial value.
D. Reinstall the top feedback chamber plug. Open the reset valve,
and check for leaks around the feedback module.
For a Reverse Acting Controller:
The integral (bottom) chamber must have full output pressure.
A. Adjust the sensing pressure such that the output is at full power
gas pressure. Wait a couple of minutes, and close the integral
valve. This locks full power gas pressure in the integral chamber.
B. Follow steps B and C for a direct acting controller.
C. Re-open the metering valve.
3. Controller Test in PID Mode
Isolate controller from the actuator by positioning MCV in manual
mode. The derivative orifice block should be set at 6. The power
gas should be the maximum allowed for your controller (i.e. a
PID-125 should have its power gas at 125 psig). The object of this
test is to make sure the output pressure reaches zero or max in
specified time.
This test is to be done once with the integral valve wide open, and
once with the integral valve at #7. This test requires a timer.
To check that the output pressure drops to zero in specified time:
Start the test with sensing pressure 20% above setpoint (i.e., if
the setpoint is 200 psig, raise it to 240 psig). The output pressure
should reach its maximum (equal to power gas). Allow the PID
chamber to become fully loaded by waiting 1-2 minutes. Lower
the sensing pressure to 3% of the maximum spring range below
the setpoint (i.e., if the setpoint is 200 psig, and the top of the
control spring’s range is 320 psig, set your pressure to 200 -
.03x320 = 190.4 pisg, approximately). Start your timer. The output
pressure should jump down a little and then continue to lower
steadily. Stop your timer when the output pressure has gone down
to approximately 10% of its full range (i.e., ˜12.5% for a PID-125).
This should take 10-20 seconds if the integral valve is wide open,
and 1-2 minutes if it is at #7.