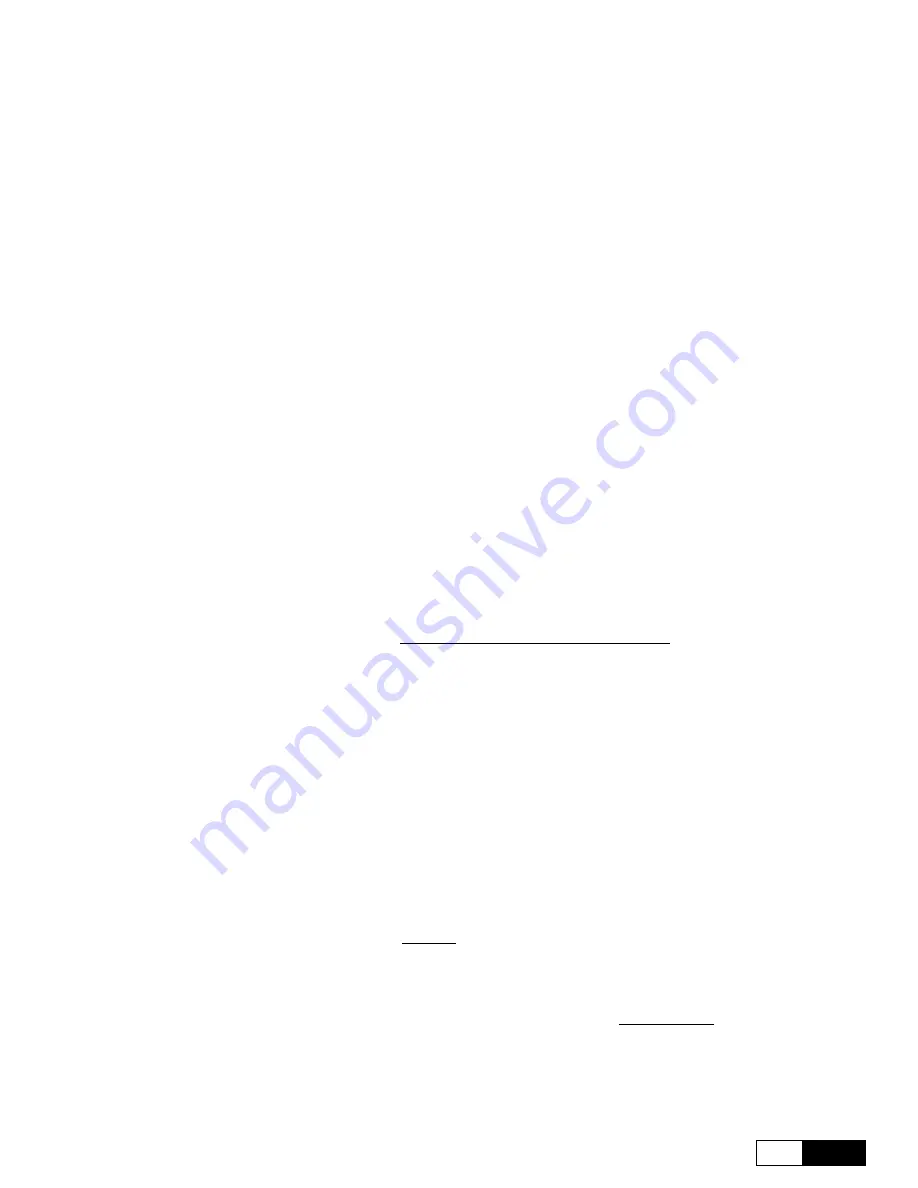
AV-300i Version 2 User’s Guide
—————— Function Description ——————
Ch.1
145
PID input cfg
Int PID fbk
Internal value of the PID section reaction
Int PID draw
Draw internal value
Int PID set 0
Setpoint 0 internal value
Int PID set 1
Setpoint 1 internal value
PID gain draw
Value of the Setpoint adapting gain (feedback)
PID acc time
Acceleration time from 0 to 16384 (Normalized internal value)
PID dec time
Deceleration time from 16384 to 0 (Normalized internal value)
PID clamp bot
Lower clamp value (see dynamic clamp)
PID clamp top
Upper clamp value (see dynamic clamp)
PID input mon
PID fbk mon
Monitor for the feedback value (reaction)
PID draw mon
Monitor for the active Draw value
PID set 0 mon
Monitor for the Setpoint 0 value
PID set 1 mon
Monitor for the Setpoint 1 value
PID input
Monitor for the Block output value
1.15.3.1 Dynamic Clamp Function
The Clamp value is active only till the error value becomes lower then the set Clamp range. The function is
useful, for example, during starting with dancer which is completely sealed. In this case, the limiting of the
maximum error limits the system reaction speed thus allowing a dancer smooth positioning. After positioning
the dancer, the Clamp stops being active allowing a normal system control.
1.15.4 Integer Proportional Control (PI control)
The Function of this Block is performed by three strictly combined different Blocks. In order to obtain a better
working homogeneity, they have been grouped into the same menu.
The three Blocks are:
PI control block
By starting from the line speed reference it states the error sign for the PI Block. It allows to
invert the line direction without performing any operation, controls the signals for the
temporary gain increase at the starting and controls the Integral section Block.
PI Gain scheduler
It allows to adapt the PI section gains according, for example, to the coil Diameter.
PI section
It is the Block where the PI regulator is performed. The feature of this regulator is a
signal on the output oscillating between two values (Top and Bottom) which can be set.
The output is multiplied by the Feed Forward value. In case of winders/unwinders, as
stated before, the Top limit and Bot limit (Clamp) values are set in order to let this
output represent the Minimum_Ray/Present_Ray ratio.
The PID PI enab src and PID I freeze src sources allow to select the origin of the enabling signals (enable/
disable) of the PI function and of the freezing signals of the regulator Integral section.
PIGP ref src selects the input signal of the gain Adaptive; the Block function allows to set a three-segment Profile.
In the Block it is possible to select, via an internal selector, three starting multiplication values: Int PID Mtl PI
1, Int PID Mtl PI 2, Int PID Mtl PI 3, internal values which can be set in the configurations.
The PID Mtl PI 3 src source connects standard the value of Int PID Mtl PI 3.
PID Mtl PI sel 0 and PID Mtl PI sel 1 are the sources selecting the command signals of the internal selector.
According to their condition, it is possible to state a combination determining the equivalent output factor.
Summary of Contents for AV-300i
Page 1: ...GEH 6641E Supersedes GEH 6641D GE Industrial Systems AV 300i TM Version 2 User s Guide ...
Page 2: ......
Page 12: ...GEH 6641E TABLE OF CONTENTS 12 ...
Page 44: ...GEH 6641E Function Description 44 Ch 1 ...
Page 174: ...GEH 6641E Function Description 174 Ch 1 ...
Page 295: ......