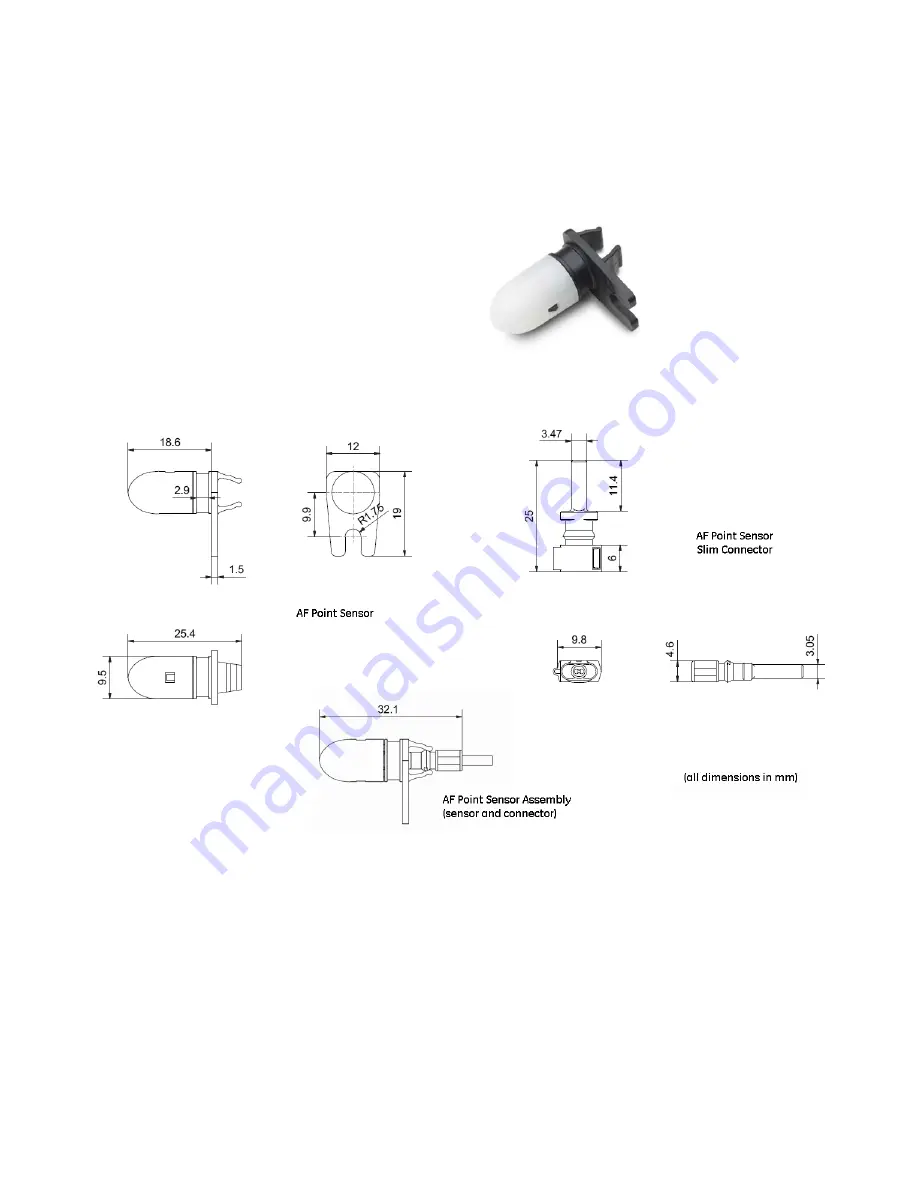
CHAPTER 2: INSTALLATION
MECHANICAL INSTALLATION
350 FEEDER PROTECTION SYSTEM – QUICKSTART GUIDE
39
•
Avoid surface temperatures above 70 °C or 158 °F to prolong the life of the fiber.
•
Secure all sensor fibers (loosely but securely) away from any moving parts.
Point sensor
installation
Figure 2-15: Arc flash point sensor without sensor fiber connected
Figure 2-16: Point sensor and slim connector dimensions