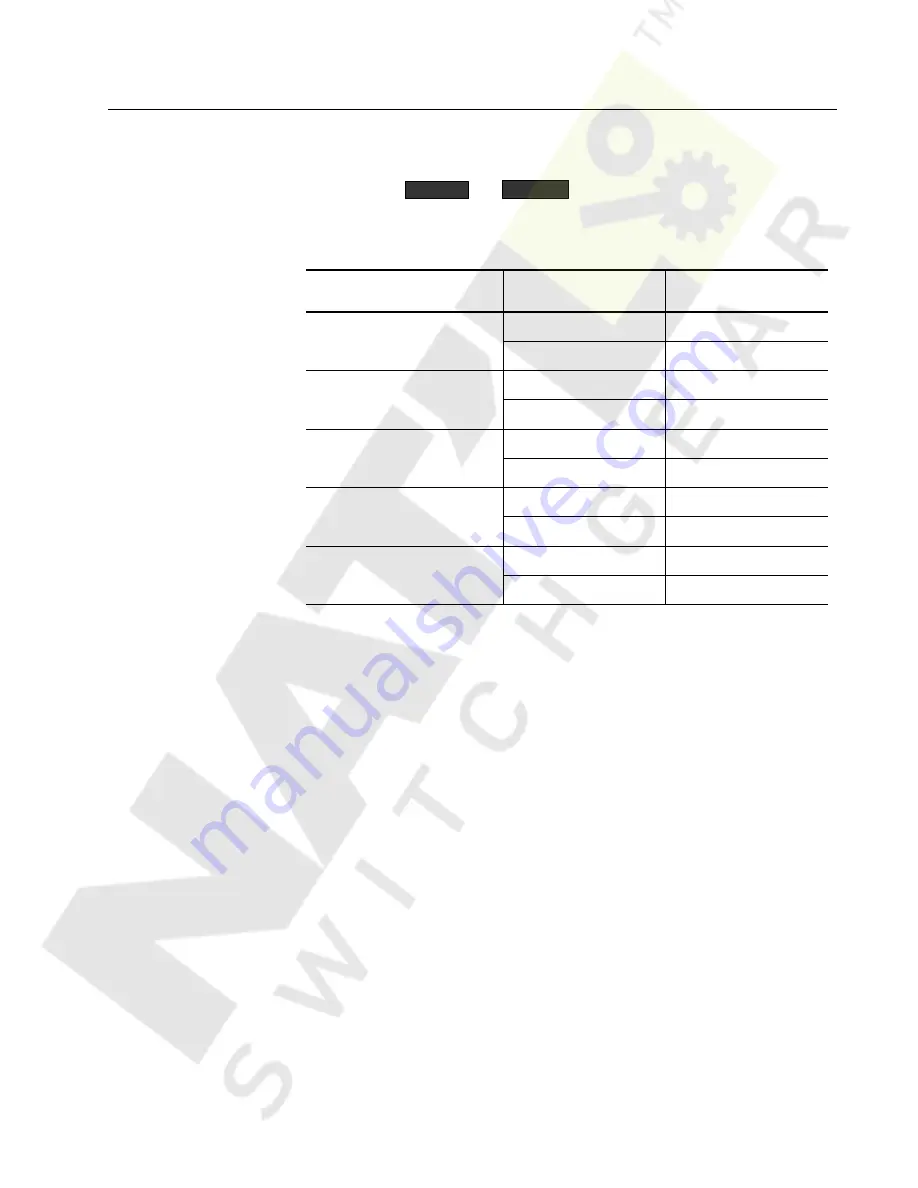
CHAPTER 7: TESTING
239 MOTOR PROTECTION RELAY – INSTRUCTION MANUAL
7–105
7.7
Switch Input
1.
To verify the operation of each 239 switch input, go to
A1: STATUS\SWITCH STATUS
and with the
and
keys, view the status of each switch input
one at a time. Open and close each switch input and note that the display reflects the
present status of the input terminals. Verify the results with the table below.
Table 7–6: Switch Input Test
SWITCH NAME
INPUT TERMINAL
STATUS
EXPECTED DISPLAY
READING
SW.1 ACCESS
OPEN
OPEN
SHORTED
CLOSED
SW2. EMERG RESTART
OPEN
OPEN
SHORTED
CLOSED
SW3. EXTERNAL RESET
OPEN
OPEN
SHORTED
CLOSED
SW4. OPTION 1
OPEN
OPEN
SHORTED
CLOSED
SW5. OPTION 2
OPEN
OPEN
SHORTED
CLOSED
MESSAGE
MESSAGE
Summary of Contents for Multilin 239
Page 6: ...TOC 4 369 MOTOR MANAGEMENT RELAY INSTRUCTION MANUAL TABLE OF CONTENTS ...
Page 20: ...1 14 239 MOTOR PROTECTION RELAY INSTRUCTION MANUAL CHAPTER 1 OVERVIEW ...
Page 48: ...3 10 239 MOTOR PROTECTION RELAY INSTRUCTION MANUAL CHAPTER 3 OPERATION ...
Page 96: ...4 58 239 MOTOR PROTECTION RELAY INSTRUCTION MANUAL CHAPTER 4 PROGRAMMING ...
Page 108: ...5 70 239 MOTOR PROTECTION RELAY INSTRUCTION MANUAL CHAPTER 5 MONITORING ...
Page 150: ...7 112 239 MOTOR PROTECTION RELAY INSTRUCTION MANUAL CHAPTER 7 TESTING ...
Page 152: ...A 2 239 MOTOR PROTECTION RELAY INSTRUCTION MANUAL CHAPTER A ...