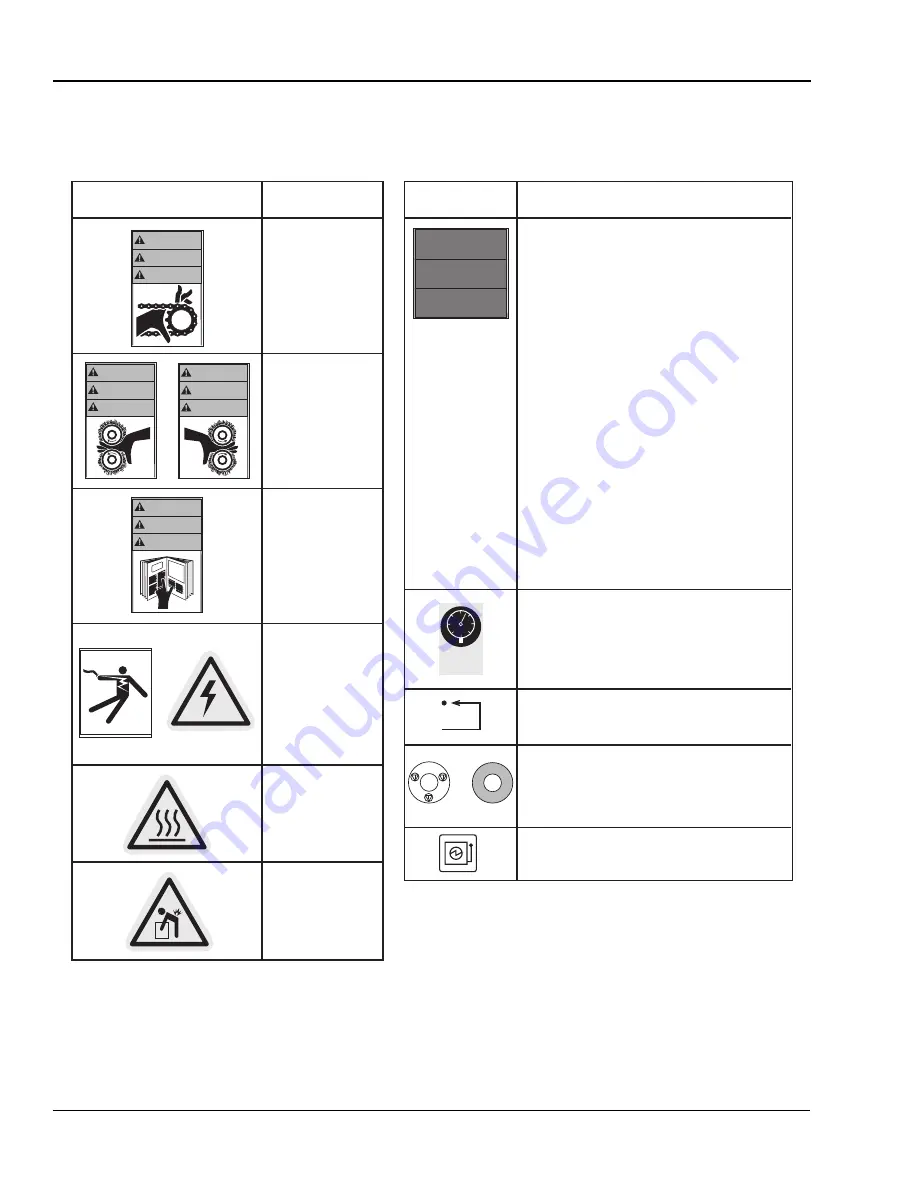
Safety
F-36 PRO Laminator Operation Manual
1-6
© GBC Pro-Tech 1999 January
The following are typical safety hazard decals used on GBC Pro-Tech machines, with a brief description (“Mean-
ing” column) of each decal.
WARNING!
Moving parts can
crush and cut.
Do not operate with
guard or door open.
WARNING!
Crush and burn
hazard. Stay clear of
moving rollers. Stop
machine and raise roll
before cleaning.
WARNING!
Carefully read
Operator's Manual
before handling this
machine. Observe
instructions and safety
rules when operating.
WARNING!
HAZARDOUS
VOLTAGE.
To be serviced only by
trained and authorized
personnel.
Lockout power before
servicing.
Reset.
CAUTION!
Surface is hot.
A burn hazard exists.
WARNING!
1.
Read and understand the Operation Manual and
all safety labels before operating this machine.
2.
Only a trained person is to be permitted to operate
this machine. Training should include instruction
in operation under normal conditions and
emergency situations.
3.
This machine is to be serviced only by trained and
authorized personnel. Follow lockout procedures
before servicing.
4.
Never reach into the machine for any reason unless
the machine is at a COMPLETE STOP.
5.
Never leave the machine stopped in such a manner
that another worker can start the machine while
you are working on or within the machine.
6.
Never change or defeat the function of electrical
interlocks or other machine "shutdown" switches.
7.
Before starting this machine, check that:
- All persons are clear of the machine.
- No maintenance work is being performed on
the machine.
- All guards are in place.
- All parent rolls are well chucked in the unwind
stands.
- The machine is free of paper scraps, wraps and
jams.
8.
There is a potential hazard of entanglement in this
machine caused by items such as long hair, loose
clothing, and jewelry. Make sure your clothing and
hair fit closely to your body and that all jewelry,
rings and watches are removed.
Decal
Meaning
Decal
Meaning
or
WARNING
ACHTUNG
MISE EN GARDE
WARNING
ACHTUNG
MISE EN GARDE
or
≤
100 PSI
≥
700 KPa
©1997 HCS, Inc. 800-748-0241 No. 6101-52BVPK
CAUTION!
Rolls are heavy.
Use proper lifting
techniques to prevent
injury.
CAUTION!
Air pressure must be less than 100 PSI (700 kPa) to
avoid damaging the machine.
or
NO
T
A
U
S
E
M
E
R
G
EN
CY
STOP
A
R
R
E
T
D
'U
R
G
EN
CE
WARNING!
EMERGENCY STOP BUTTON
Press this button to stop the machine cycle, remove
electric power, and separate (open) rolls to eliminate a
pinch point (on some machines).
Electric power disconnect and lock out location.
WARNING
ACHTUNG
MISE EN GARDE
WARNING
ACHTUNG
MISE EN GARDE
SAFETY
INSTRUCTIONS
SICHERHEITS-
RICHTLINIEN
CONSIGNES DE
SÉCURITÉ
©1994 Hazard Communication Systems, Inc. 800-748-0241