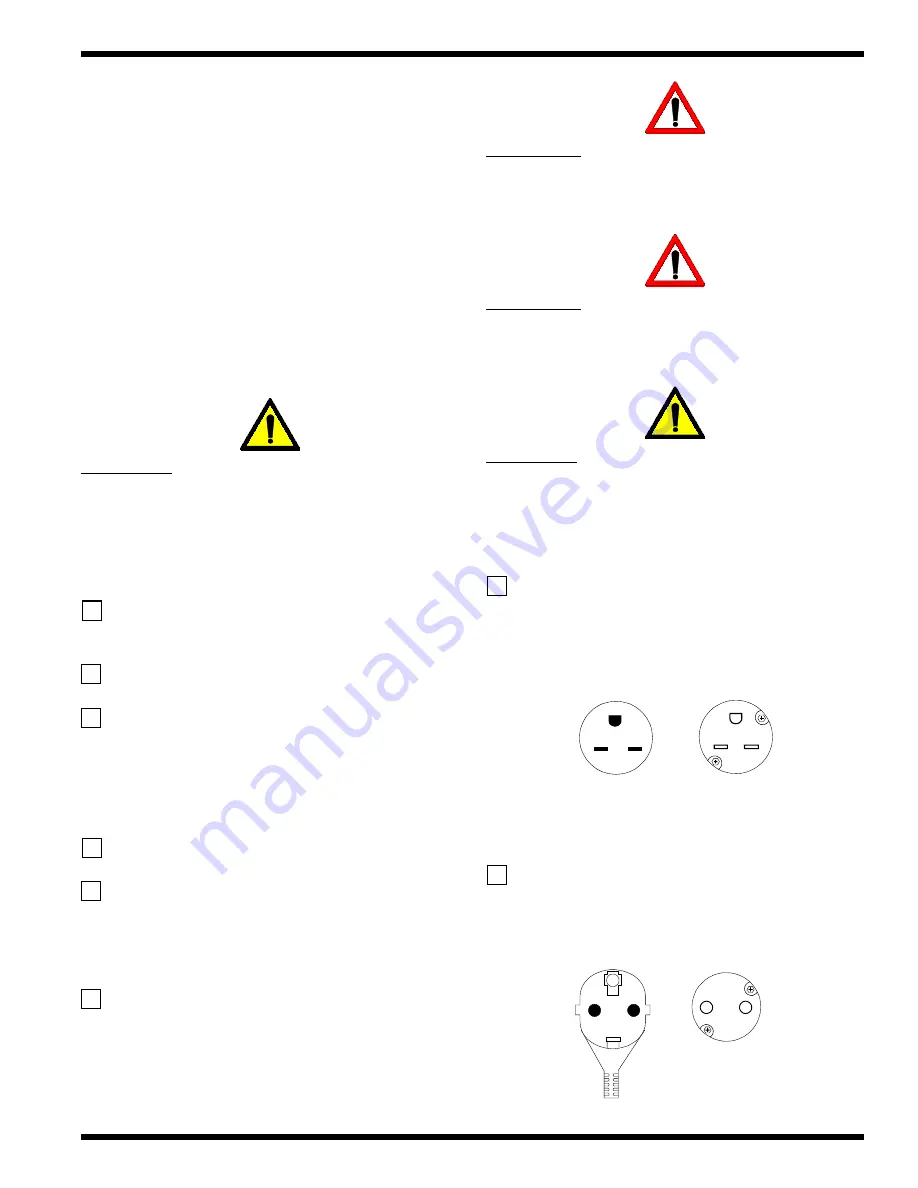
© 2004 General Binding Corporation
Spartan Operation and Maintenance Manual
Page 4-1
4.0 Installation
GBC Films Group is committed to a program of ongoing
product improvement. As a result, we are providing these
instructions so that you can insure that your new Spartan
Laminator is properly and securely unpacked, moved and
installed.
Before a Spartan Laminator can be installed, there are a
few requirements that must be met. Make certain that
each of the requirements listed in the following pre-
installation checklist are met before beginning installation.
CAUTION: Failure to follow the pre-installation
check list can result in damage to the laminator.
4.1 Pre-installation
Are the doorways and hallways wide enough for
the laminator to be moved to the installation site?
Is there ample room for the laminator?
A work area must be established that allows for
unrestricted movement around the laminator and
provides space for efficient material flow. Figure
4.1.4 and Figure 4.1.5 illustrates a typical machine
area layout.
Is the environment appropriate for the laminator?
The laminator requires a clean, dust and vapor
free environment to operate properly. It must not
be located where there is air blowing directly on
the machine.
Have you contacted a certified electrician to install
a receptacle for the laminator ensuring that
adequate power is being supplied and correct
circuit breaker?
WARNING: The operating environment must be
free of dust, flammable liquids and vapors. You can
be injured by inhaling chemical vapors.
WARNING: Vapor build up or stored flammable
liquids can cause a fire. Excessive dust can damage
the laminator.
CAUTION: Do not locate the laminator where air
can blow directly on the machine. The air flow can
cool the rollers unevenly and result in poor quality
output.
US and Canada: The laminator requires 230-
240 vac, 60 Hz, 15 amps, single phase
Figure 4.1.1 Connections-Spartan US
N E M A 6 - 1 5 R
N E M A 6 - 1 5 P
Europe: The laminator requires 230-240, 50 Hz
16 amps, single phase
Figure 4.1.2 Connections-Spartan Europe
1 6 re c e p ta c le
1 6 p lu g