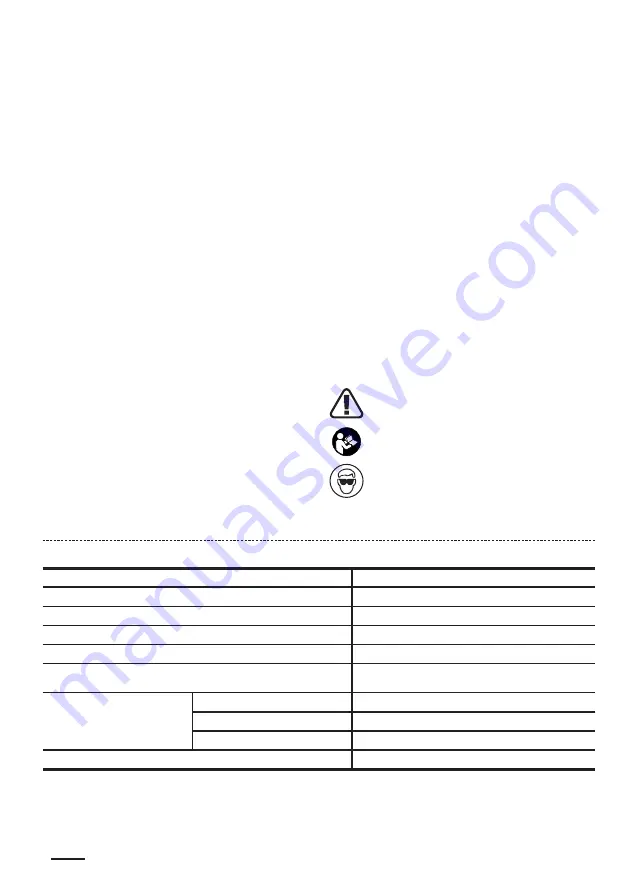
4
EN
f) Do not restart the cutting operation in the
workpiece . Let the wheel reach full speed and
carefully re - enter the cut .
The wheel may bind
, walk up or kickback if the power tool is restarted
in the workpiece .
g) Support any oversized workpiece to minimize
the risk of wheel pinching and kickback .
Large
workpieces tend to sag under their own weight .
Supports must be placed under the workpiece near
the line of cut and near the edge of the workpiace
on both sides of the wheel .
UK power plug warnings:
Your product is fitted with an BS 1363-1 approved
electric plug with internal fuse approved to BS 1362.
If the plug is not suitable for your socket, it should
beremoved and an appropriate plug should be
fitted inits place by an authorized customer service
agent.The replacement plug should have the same
fuserating as the original plug.The severed plug
must be disposed of to avoid apossible shock hazard
and should never be inserted into a mains socket
elsewhere.
Symbol
To reduce the risk of injury, user must
read instruction manual
WARNING
Always wear eye protection
Technical Data
Model
GM4535
Rated Power Input W
2000
No-load Speed /min
3800
Max. Cutting Angle °
45
Max. Opening Size mm
191
Wheel Size mm
355x3x25.4
Max. Cutting Capacity
Round Bar mm
65
Pipe mm
120
Profiled Bar mm
120x130
Net Weight kg
16
※
Due to the continuing program of research and development, the specifications herein are subject to change
without prior notice.
pinched by the workpiece , the edge of the wheel
that is entering into the pinch point can dig into the
surface of the material causing the wheel to climb out
or kick out . Abrasive wheels may also break under
these conditions .
Kickback is the result of power tool misuse and / or
incorrect operating procedures or conditions and can
be avoided by taking proper precautions as given
below .
a) Maintain a firm grip on the power tool and
position your body and arm to allow you to
resist kickback forces .
The operator can control
upward kickback forces , if proper precautions are
taken .
b)Do not position your body in line with the
rotating wheel .
If kickback occurs , It will propel
the cutting unit upwards toward the operator.
c) Do not attach a saw chain , woodcarving blade
. segmented diamond wheel with a peripheral
gap greater than 10 mm or toothed saw blade .
Such blades create frequent kickback and loss of
control.
d) Do not " jam " the wheel or apply excessive
pressure . Do not attempt to make an excessive
depth of cut .
Overstressing the wheel increases
the loading and susceptibility to twisting or binding
of the wheel in the cut and the possibility of
kickback or wheel breakage .
e) When the wheel is binding or when interrupting
a cut for any reason , switch off the power
tool and hold the cutting unit motionless until
the wheel comes to a complete stop . Never
attempt to remove the wheol from the cut while
the wheel is in motion otherwise kickback may
occur .
Investigate and take corrective acton to
eliminate the cause of wheel binding.