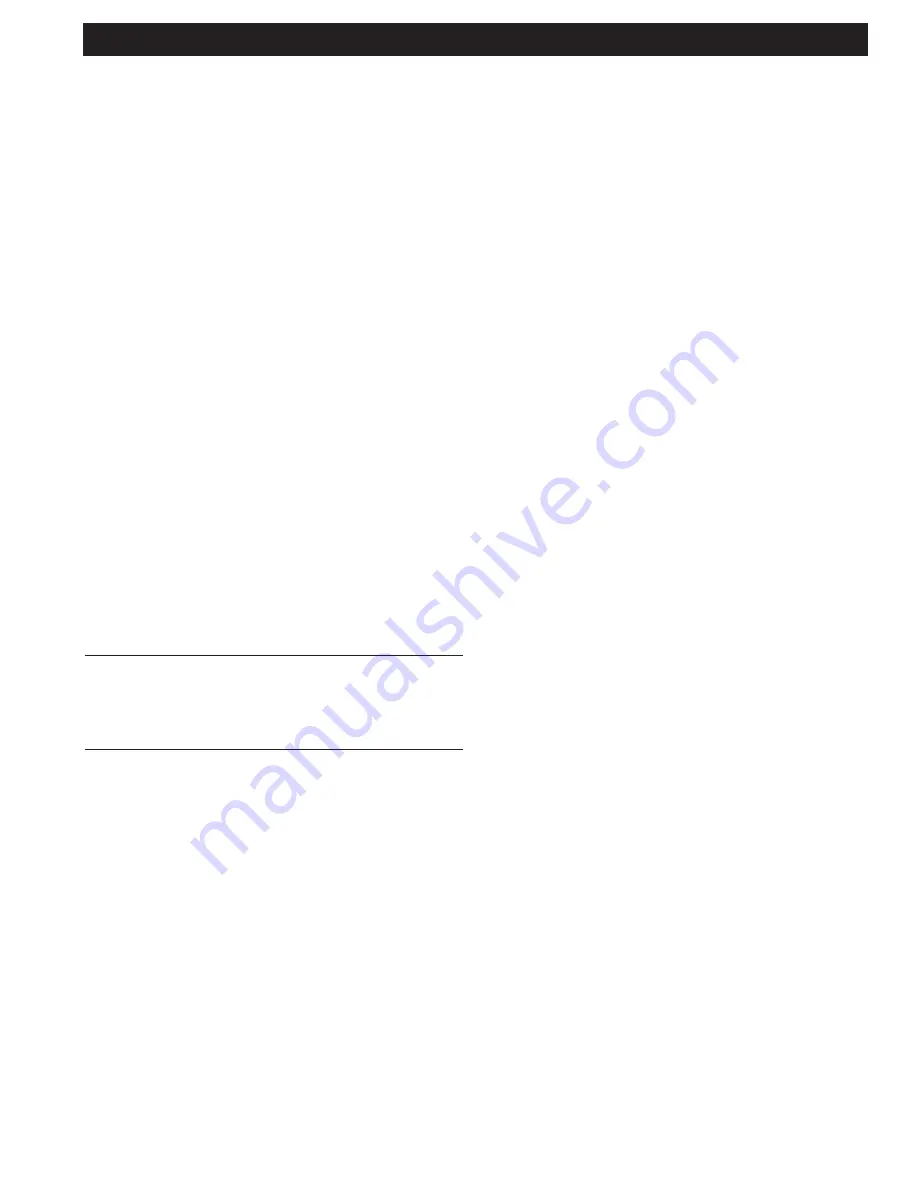
12
RECEIVING
Most ClearAir
TM
units are shipped in one piece. However,
some units, because of size or special jobsite conditions,
may be shipped in multiple sections. Follow the instruc-
tions provided with the unit to join sections back together.
If the unit includes media bed odor control, the KOR48/
carbon odor control media is packaged separately. Verify
against the shipping documents that you have received all
items and note any shipping damage, obvious or hidden, to
your carrier and on your Bill of Lading. If damage is found,
immediately file a claim with the transport company. All units
are thoroughly inspected and fully operation tested at the
factory prior to shipment.
Verify that the electrical and air flow ratings on the unit
nameplate agrees with jobsite requirements. If a contradiction
arises notify the factory prior to proceeding with installation.
SAFETY CONSIDERATIONS
Installing and servicing the ClearAir
TM
unit can be hazardous
due to the presence of electrical components. Only trained
and qualified service personnel should install or service
this equipment.
Untrained personnel can perform basic maintenance, such
as cleaning and replacing filters. All other operations should
be performed by trained service personnel. When installing
or servicing, observe precautions in literature and on tags
and labels attached to unit.
Follow all safety codes. Wear safety glasses and work
gloves. Use quenching cloth for brazing operations. Have
fire extinguisher available. Read these instructions thor-
oughly.
WARNING
Before installing or servicing system, always turn off main
power to system. There may be more than one disconnect
switch. Electrical shock can cause personal injury or death.
RIGGING
All units are provided with a minimum of four (4) lifting points
for rigging attachment. WARNING: Use all lifting points
provided. (Refer to Page 13) Spreader bars are mandatory
to prevent contact and damage to the unit by lifting hooks,
straps, cables, or chains. Consult the mechanical or struc-
tural engineer before moving the unit across the roof deck.
INSTALLATION CODES
This unit requires external plumbing and electrical connections
to be made in the field. It is recommended that the Author-
ity Having Jurisdiction (AHJ) be consulted regarding local
codes and installation procedures. Gaylord Industries is not
responsible for obtaining necessary approvals and permits
which may be required for installation, nor is it responsible
for verifying that the unit has been installed in accordance
with national, state, and local codes. In the absence of locally
adopted codes use the current editions of the National Elec-
trical Code and the Uniform Mechanical Code. Connections
of the exhaust duct to the inlet and outlet of the ClearAir
TM
unit must be fully welded to comply with NFPA-96.
INSTALLATION PRECAUTIONS
1. The services of qualified contractors are essential for
safe and proper installation of this equipment.
2. The air volumes and external static pressures that are
listed on the unit are for the middle of the operating range
of the filters. The initial air volume should be at least 10%
higher than the listed CFM. As the filters load up the air
volume will drop. This is inherent to this type of unit. If the
unit is set up at or below the design CFM, as the filters load
up, the kitchen hood may experience smoke loss problems.
Please consult the factory if you have questions.
3. The unit is designed for installation on a level surface.
4. When installed in an enclosed space a fire rated enclo-
sure may be required for the unit and associated duct work.
Consult the Authority Having Jurisdiction.
5. Consult the Authority Having Jurisdiction regarding re-
quirements covering the point of termination of the exhaust
outlet of this unit. Minimum distances must usually be
maintained between the exhaust outlet and any outside air
intakes and/or adjacent structures or property lines.
6. Do not apply power to the unit until all electrical con-
nections have been made and a pre-start-up preliminary
inspection has been completed.
7. Allow a minimum of 36 inches clearance in front of the
filter access door and electrical compartment door for ser-
vice and routine maintenance per NEC.
SHORT TERM STORAGE
Units that include media bed odor control are provided with
KOR48/carbon media which is shipped separate from the
unit. KOR48/carbon media must be stored in a dry place
with less than 95% relative humidity.
EXHAUST FAN RECEIVING AND STORAGE
If the unit is equipped with an exhaust fan it must be re-
lubricated as soon as it arrives. To prevent corrosion all
bearings should receive grease and be rotated the first of
every month. Rotate the wheel several revolutions every
three to five days to keep a coating of grease on all internal
bearing parts. Turn the wheel by hand while greasing bear-
ings. A clean 1/16" bead of grease must appear on each
side of each bearing. Refer to specific bearing lubricating
instructions on the fan. Also, refer to bearing lubricating
instructions found in the exhaust fan section of this manual.
Bearings which are to be stored or idle for an extended
period of time should be wrapped in a neutral grease-proof
paper, foil, or plastic film. Compounds can be recommended
by the bearing manufacturer to provide protection for sev-
eral months to several years.
After long-term storage, grease should be purged from the
bearings and fresh grease injected prior to start-up.
RECEIVING & INSTALLATION
Summary of Contents for ClearAir RSPC-ESP SERIES
Page 9: ...9 TYPICAL INSTALLATION ...
Page 46: ...46 PARTS DETERGENT PUMP 45 PARTS DETERGENT PUMP ...
Page 53: ...53 C 6000 ESP INTERNAL WIRING DIAGRAM ...
Page 56: ...56 RSPC ESP DRAIN ...
Page 57: ...57 SPRAY ODOR WIRING ...
Page 68: ...INTENTIONALLY LEFT BLANK ...