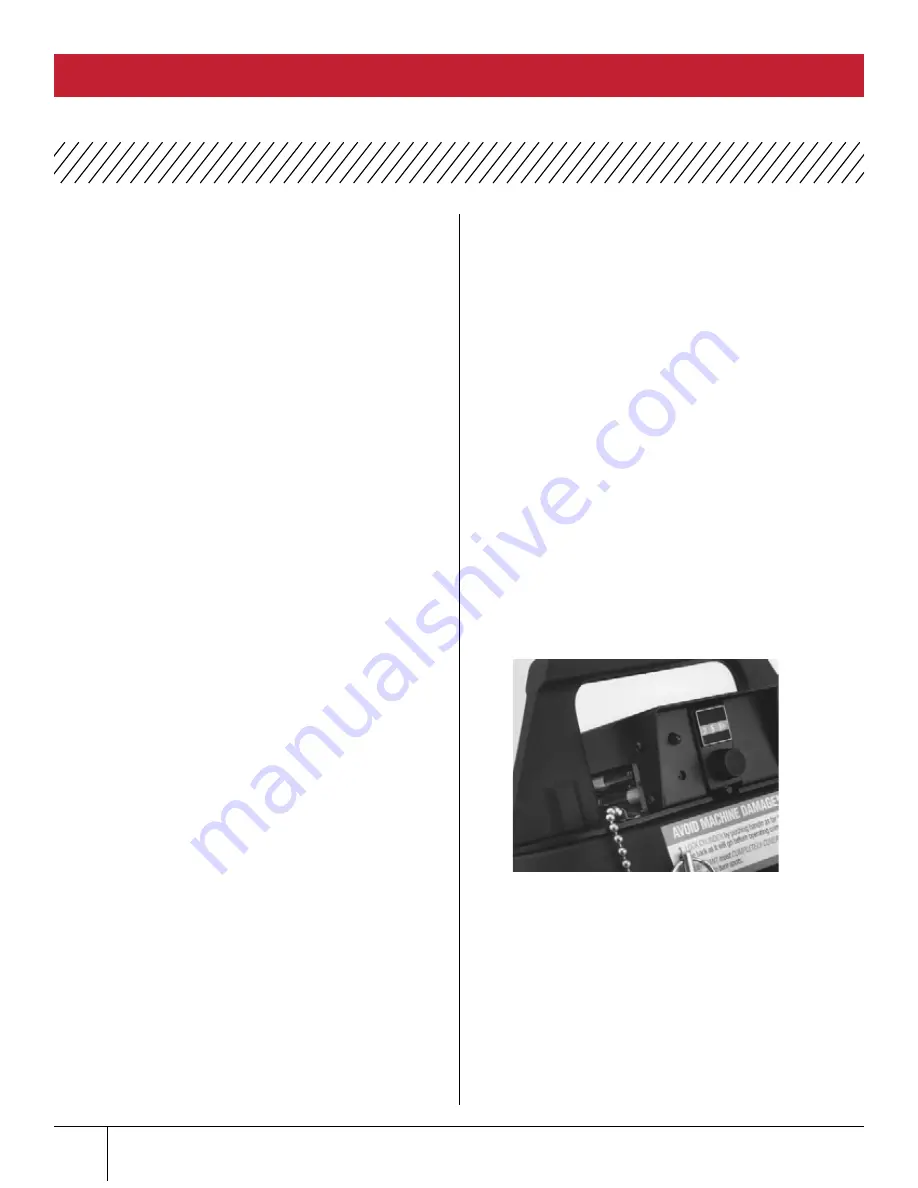
This crimper requires minimal maintenance.
However, the following practices are recommended to
ensure maximum reliability and service.
LUBRICATE
Using the small brush and Molykote, apply a
light coat to the inside surface of the die cone
whenever it becomes shiny.
CHECK OIL LEVEL
Check the hydraulic oil level in the pump reservoir
after each 10 hours of use (see pump operations
manual for instructions).
The oil is more than 1/2” below the top, add a high
grade hydraulic oil, such as Enerpac Oil, until
within 1/2” of the top of the reservoir.
CHANGE THE OIL
NOTE: Frequency depends on the pump’s general
working conditions, severity of use, and overall
cleanliness.
For general shop conditions, change oil every 300
hours. For field/mobile conditions, more frequent
changes are required.
Drain, clean, and refill the reservoir per pump
operating instructions with a high-grade hydraulic
oil, such as Mobil DTE 25 until within 1/2” of the top
of the reservoir.
IMPACT DIE SETS AND PRESSURE PLATE
Periodically inspect the surfaces of die sets and
pressure plate for debris (metal chips, dirt, etc.)
or damage.
If debris is present, clean and lightly lubricate. If
damaged, replacement is required (see parts list for
ordering information).
Inspect the die links, springs, and shoulder
screws monthly to see if they are broken, cracked,
or missing. These conditions may affect crimp quality
Replace if necessary.
INSPECT HOSE ASSEMBLY
Inspect hose assembly connecting the crimper and
pump monthly (more often with severe use).
Check nylon sleeve for cuts or abrasions. If sleeve
is damaged, check hose for damage. If hose
has signs of damage, replace immediately. A
damaged hose may rupture and cause serious injury.
If hydraulic oil is present on the hose assembly,
serious damage may exist. Replace immediately.
BATTERY REPLACEMENT
If light and buzzer become faint or do not work,
batteries may need replacement. The controller uses
AAA batteries. Remove the two screws located on the
lower left side of the controller. Remove the side
cover and the batteries from their holder.
Replace the batteries and position as shown on
holder. Replace and secure the side cover.
MAINTENANCE
MOBILE CRIMP 4-20 SAFETY AND OPERATING MANUAL
16