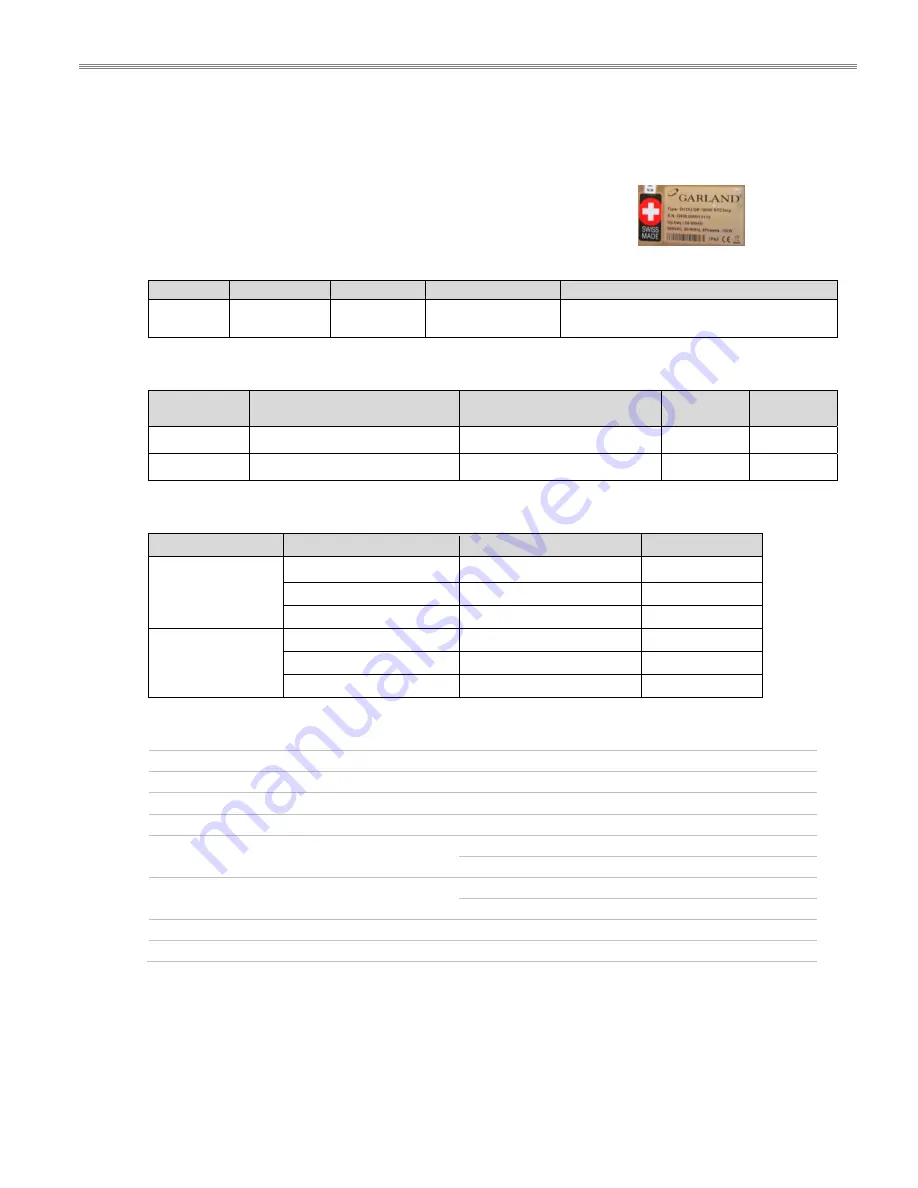
Dimensions and Technical Specifications
RTCSmp Induction Built-In Line Dual Zone Cookers
Part # 4532285 Rev 4 (4/29/14)
7
3
Dimensions and Technical Specifications
3.1
Rating Plate
The rating plate specifies important information such as the model number,
serial number, and electrical specifications. The rating plate is affixed to the
unit’s housing, close to the mains power connection on the unit.
3.2
Nomenclature and Models
Series
Dual Hobs
Built-In
Power (Watt)
Models
SH
=
Slim Hob
DU
IN
=
Built-In Line
7000 (2x 3500)
10000 (2x 5000)
SH DU IN 7000 (2x 3500 / 7kW)
SH DU IN 10000 (2x 5000 / 10kW)
3.3
Dimensions and Weights
Glass Area Only
(width x depth)
Glass-Top with Frame
(width x depth)
Shipping
Weight
Net
Weight
7kW Model
12.60” x 22.83” (320 x 580 mm)
15.12” x 25.35” (384 x 644 mm) 25kg/55.1lb 23kg/50.7lb
10kW Model
12.60” x 22.83” (320 x 580 mm)
15.12” x 25.35” (384 x 644 mm) 27kg/59.5lb 25kg/55.1lb
3.4
Electrical Specifications
Voltage
Power
Conductor Size
7kW Model
208 V AC / 3Ph / 60Hz
7000 W (2x 3500W) / 22A
AWG 10
400 V AC / 3Ph / 50Hz
7000 W (2x 3500W) / 11A
1.5mm
2
440 V AC / 3Ph / 50Hz
7000 W (2x 3500W) / 10A
1.5mm
2
10kW Model
208 V AC / 3Ph / 60Hz
10000 W (2x 5000W) / 30A
AWG 8
400 V AC / 3Ph / 50Hz
10000 W (2x 5000W) / 16A
2.5mm
2
440 V AC / 3Ph / 50Hz
10000 W (2x 5000W) / 15A
2.5mm
2
3.5
Operating Conditions
Max. Tolerance of Nominal Supply Voltage
+6 /-10 %
Supply frequency
50/60 Hz
Ingress Protection class
IP X0
Minimal Diameter of Induction Pan
5” (12cm)
Maximum Ambient Temperature
In Storage > -4°F to +158°F (-20°C to +70°C)
In Operation >+ 41°F to +104°F (+5°C to +40°C)
Maximum Relative Air Humidity
In Storage > 10% to 90%
In Operation > 30% to 90%
Clearance from Materials
Min. 1.18” / 30mm
Maximum air flow: 70.63cfm/120m
3
per hour and min. opening: 10.075in
2
/6500mm
2
is required.
3.6
Compliances
North American models
:
ETL listed in compliance with UL 197, CSA C22.2 No.109, NSF-4. Complies with FCC part 18, ICES-001
CE models
comply with the latest European Norms:
EN 60335-1, EN 60335-2-36, EN 62233 (EMC/EMV)