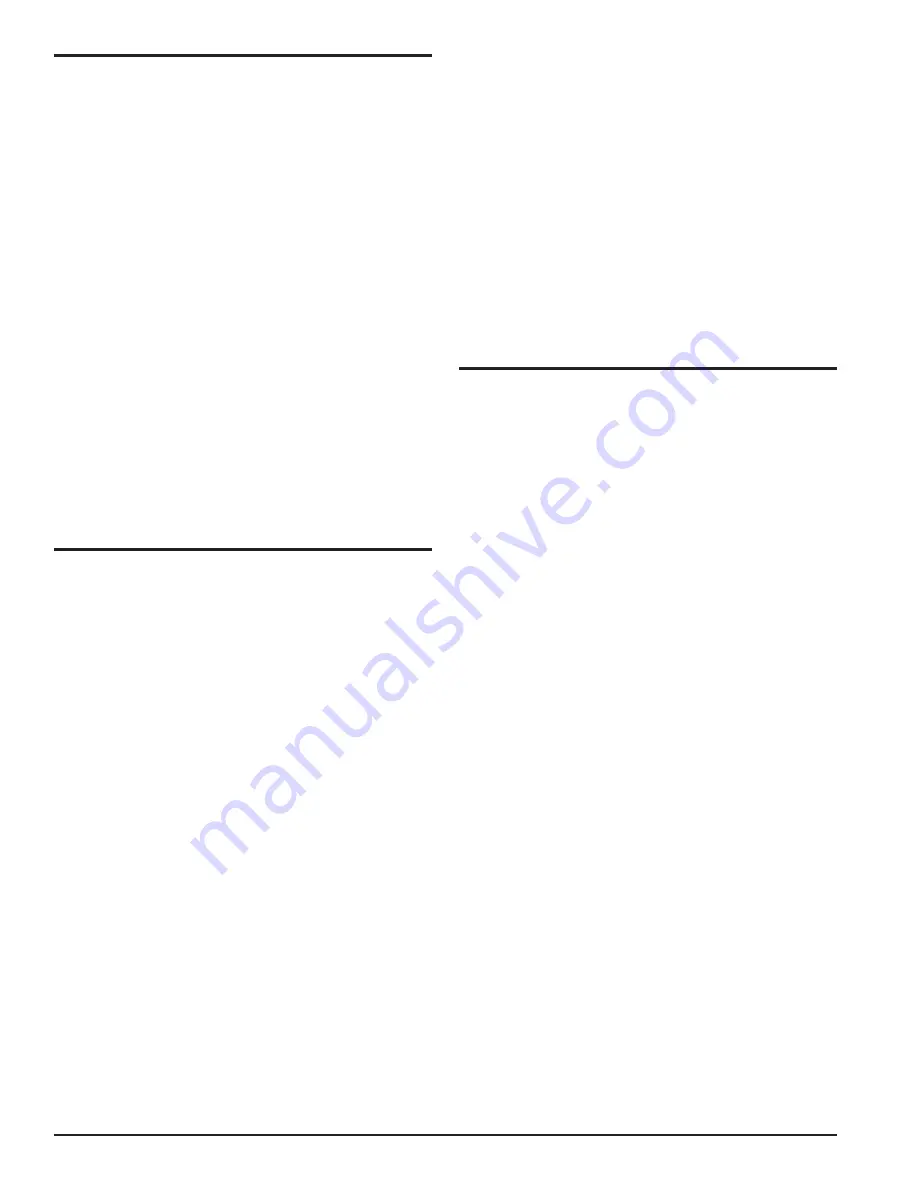
1 - 2
SAFETY INSTRUCTIONS
Safety instructions in this manual are boldfaced for em-
phasis. The signal words DANGER, WARNING and CAU-
TION are used to indicate hazard seriousness levels as
follows:
DANGER
—Immediate hazard which WILL result in severe
injury or death.
WARNING
—Hazard or unsafe practice which COULD re-
sult in sever injury or death.
CAUTION
—Hazard or unsafe practice which COULD re-
sult in minor injury or in product or property damage.
Safety Labels
Dryer labels provide important safety information. If any
label is damaged or comes off the dryer, contact your local
distributor to request a replacement.
Data Plate
The dryer data plate contains critical safety and identifica-
tion information. If the data plate is missing or damaged,
immediately contact your local distributor for a replacement.
RECEIVING AND INSPECTION
Inspect the dryer closely when it is received. Record any
indication of careless handling by the carrier on the deliv-
ery receipt, especially if the dryer will not be immediately
uncrated. Obtain the delivery person’s signed agreement
to recorded damages to facilitate future insurance claims.
Since the dryer is shipped F.O.B. point of shipment, the
manufacturer’s responsibility for the shipment ceases when
the carrier signs the bill of lading.
If goods are received short or in damaged condition, notify
the carrier and insist on a notation of the loss or damage
across the face of the freight bill. Otherwise no claim can
be enforced against the carrier.
If concealed loss or damage is discovered, notify your car-
rier at once and request an inspection. This is absolutely
necessary. Unless you do this the carrier will not consider
any claim for loss or damage. The carrier will make an
inspection and may grant a concealed damage notation. If
you give the carrier a clear receipt for goods that have been
damaged or lost in transit, you do so at your own risk and
expense.
The manufacturer is willing to assist you in collecting claims
for loss or damage. Willingness does not make the manu-
facturer responsible for collecting claims or replacing ma-
terial. Claim filing and processing is your responsibility.
Handling
The dryer is mounted on a base to facilitate moving the
dryer with a forklift. Forks should extend all the way through
the forklift channels provided, to reduce stress on the dryer
frame. If slings are used to move the dryer, use spreader
bars to prevent damage to the sides of the dryer.
Returns to Manufacturer
If the dryer or a component of the dryer must be returned
to the manufacturer, first call your local distributor for a re-
turn authorization number and shipping address. Your dis-
tributor will inform you whether the dryer or only a compo-
nent must be returned. Mark the package with the return
authorization number and ship freight prepaid as directed
by your local distributor.
INSTALLATION
Ambient Air Temperature
Locate the dryer indoors where the ambient air tempera-
ture will be between 40°F and 100°F. Intermittent opera-
tion at ambient temperatures up to 120°F will not damage
the dryer provided the dryer is derated. Failure to derate
the dryer may result in a higher dew point or dryer shut-
down due to high refrigerant discharge pressure (see Field
Service Guide). Call your local distributor if prolonged op-
eration at ambient temperatures above 100°F or below 40°F
is unavoidable.
Location
If the dryer is air cooled, install it in a clean, well ventilated
area to reduce fouling of the condenser coils with dirt and
dust. Vapors and contaminant corrosives to copper and
aluminum must not be in the area of the dryer or air com-
pressor intake. Allow at least 36 inches clearance on all
sides for adequate cooling airflow and service access. In-
stall the dryer with the frame level. Anchor bolts are not
required.
Storage
The dryer can be stored for a period of one year in a clean,
dry, temperature-controlled environment. Consult factory if
storage requirement is longer than one year.
System Arrangement
Liquid water adversely affects dryer performance. To pre-
vent “slugging” the dryer with liquid water, locate the dryer
downstream of an aftercooler and a mechanical separator.
Install drain valves to discharge condensate that collects in
these areas.
For safety and convenience, install inlet and outlet shutoff
valves and depressurization valves at the locations indi-
cated (see Typical Compressed Air System drawings on
page 1-14). These valves allow the dryer to be isolated