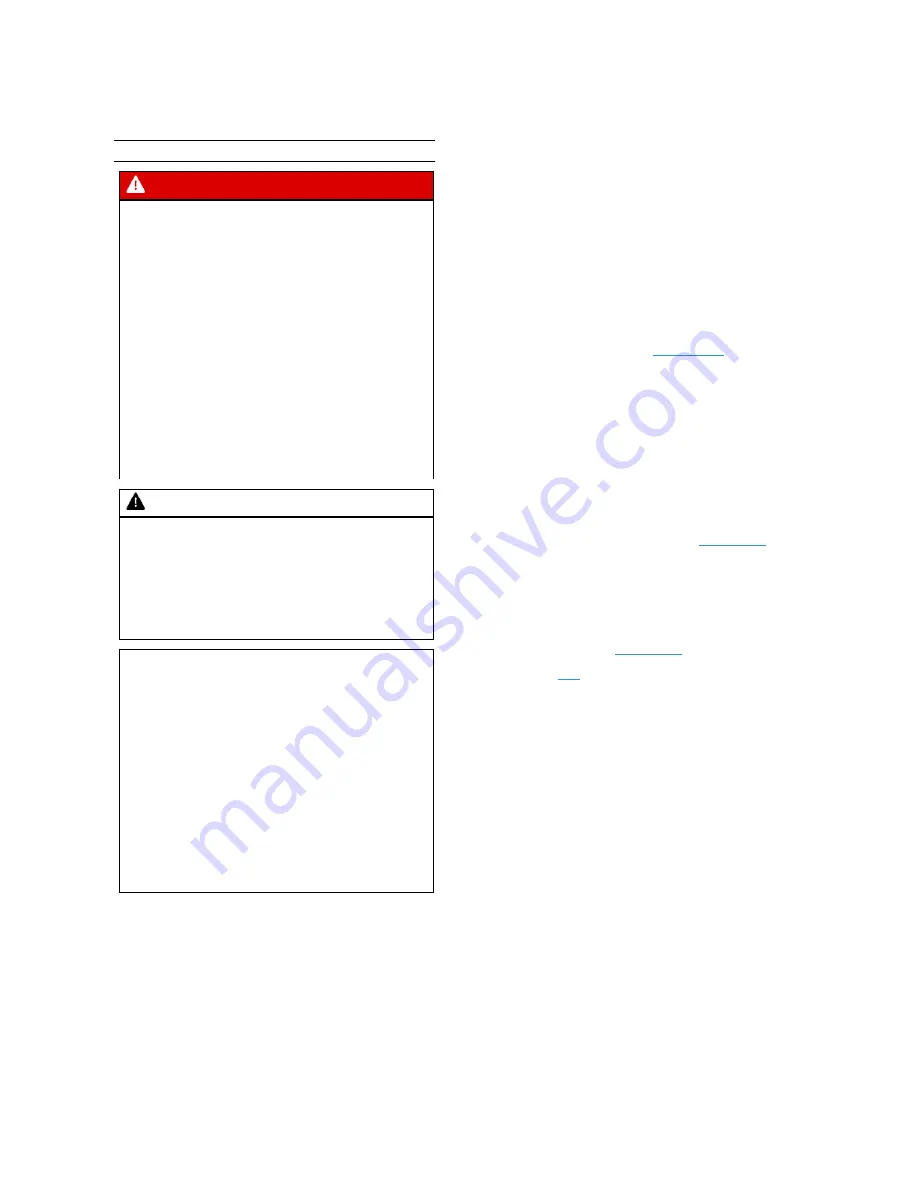
August 20, 2018
35
8
Commissioning
8.1 First commissioning
DANGER
The rotational direction of the motor can
only be checked with the casing open.
Rotating parts may lead to injuries,
e.g., cutting of finger or hand.
·
Before commissioning make sure that no
one is located in the danger zone of the
screw compressor!
·
Be careful of rotating parts!
·
Keep a sufficient distance from rotating
machine parts!
·
Wear ear protectors
·
Always operate system with the casing
closed except when performing this test.
CAUTION
Damages during transport may impair
safety!
·
Before commissioning, every screw
compressor should be checked again
for damage and should be watched
during the first hour of operation.
NOTICE
When the compressor system is connected to a
power source for the first time, always check
the drive direction of the drive motor! With a
wrong direction of rotation, shut down the unit
immediately by pressing the emergency STOP
button (-7- Fig. 16) (not the [O] ), otherwise the
compressor may be seriously damaged, even
during short periods of operation.
When storing the screw compressor system or
in the event of a longer period of downtime, if
there is the risk of frost ( t < 33.8°F) the cooling
water should be completely discharged.
The screw compressor unit is completely factory-
assembled. It can be directly connected to the com-
pressed air mains by means of a flexible connection.
First commissioning is carried out as follows:
·
Remove transport guards, if fitted.
·
Check the oil level in the pressure reservoir
(also see Section 7.5 Fig. 14)
·
Check settings of the fan motor protection switch
(only L55RS-L75RS) (see Section 7.4.1)
·
Check the setting of the control-power transformer
(see also chapter 7.4.2).
·
Check and re-tighten all connecting terminals of the
electrical control.
·
Open isolator valves between the screw
compressor, reservoir and pipe.
·
Ensure cooling water supply in accordance with
Chapter 7.3. (only water-cooled units).
·
Turn on the main power supply switch.
·
After the power supply was switched on, all LEDs
on the compressor control
GD Pilot TS
light up for
a display test. The fault shown on the display [power
supply fault] must be acknowledged in the fault
memory menu item prior to starting the unit. (The
display language can be set in the start screen
using the "globe icon".)
·
After the acknowledgement, the message [READY
TO START] appears on the display, unless another
fault is present.
·
The factory setting of the setpoint value for the
network pressure (upper and lower switching point)
is saved in the compressor control
GD Pilot TS
and
depends on the relevant pressure variant of the
compressor (see nameplate fig. 1, stage pressures
= maximum operating pressure). These settings can
be checked or changed in the compressor control
menu [Settings; Pressure range, p1] (further
information can be found in Section 5 of the
compressor control
GD Pilot TS
operating manual).
·
Only L55-
L80
: Temporarily remove the panel in order
to check the direction of rotation. See (-1- Fig. 15) for
the prescribed direction of rotation of the drive motor
of the geared compressor. See (-1 Fig. 15 a) for the
prescribed direction of rotation of the drive motor with
direct drive. For the prescribed direction of rotation of
the fan, see direction of rotation arrow on the fan (-3-
Fig. 15 b and c). The direction of rotation of the fan
can also be checked on the basis of the direction of
the cooling air flow (- 1-, - 2 - Fig. 15 c and d)
·
Press the START button [ I ] (-2- Fig. 16) and
immediately
check the direction of rotation.
·
With a wrong direction of rotation,
immediately
press the emergency STOP button (-7- Fig. 16),
and correct the direction of rotation.
·
Next, check the control transformer output voltages
while operating under load (see Section 10.9).
Summary of Contents for L55
Page 2: ......
Page 27: ...August 20 2018 25 Fig 5...
Page 62: ...60 August 20 2018 Fig 29 all dimensions in mm...
Page 63: ......