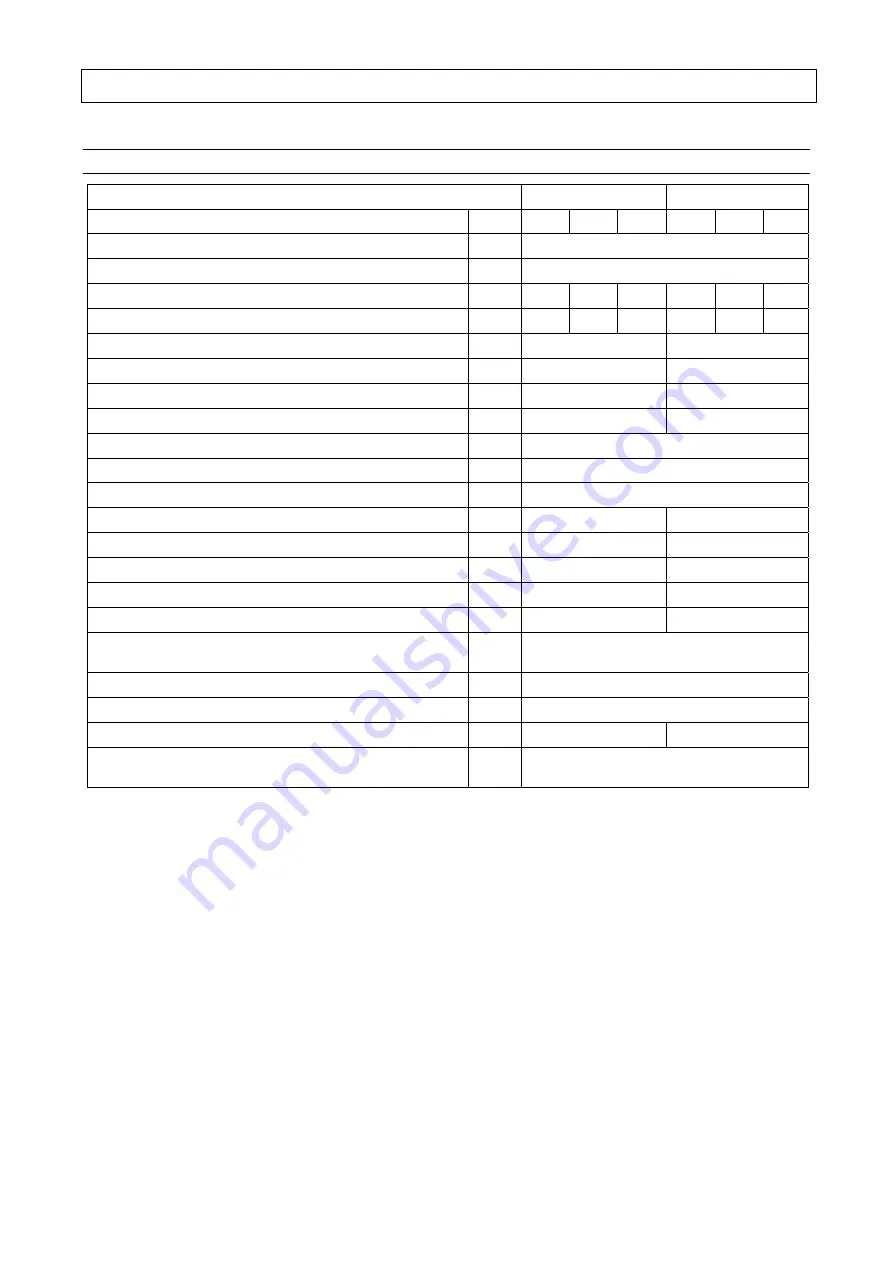
11. Annex
51
11 Annex
11.1 Technical data USA/Canada version L07-L11 60 Hz
Technical Data L07-L11 ; 60 Hz
L07
L11
Maximum operating pressure
psi g
110
130
190
110
130
190
Minimum operating pressure
psi g
73
Ambient temperature
°F
+ 34 / + 113
Flow cfm
44.8
39.5
27.2 65.0 59.0 45.5
After-cooler outlet temperature above ambient temp.
°F
18
18
18
22
22
20
Sound pressure level (to ISO 2151)
dB(A)
71
71
Nominal motor rating
hp(kW)
7.5 (10)
15 (11)
Full-load current max. 200V / 230V
Amps
33 / 29
47 / 42
Full-load current max. 460V / 575 V
Amps
15 / 12
21 / 17
Motor protection type
IP55, EPAct
Nominal speed
rpm
3600
Nominal fan motor power
no separate fan motor
Recommended cable size (200V/230V/460V/575V) @ 167°F
AWG
8 / 8 / 14 / 14
6 / 6 / 10 / 12
Recommended fuse size (200V/230V/460V/575V)
Amps
40 / 35 / 20 / 15
60 / 50 / 30 / 20
Ventilating fan capacity
cfm
1060
1200
Cooling air outlet temperature above ambient temp.
°F
29
36
max. allowable pressure drop in duct at ambient
Pa
100 / 80
110 / 90
Total oil volume
gal
(litres)
1.3
(5)
Approx. Oil carry over
ppm
3-5
Compressed air delivery connections
3/4" - 14 NPT
Weight
lbs (kg)
452 (205)
483 (219)
Dimensions L x W x T
inch
(mm)
26.5 x 24.8 x 41.3
(667 x 630 x 1050)
Summary of Contents for L07
Page 2: ......
Page 43: ...9 Service and maintenance 41...
Page 57: ...55...
Page 58: ......
Page 59: ......