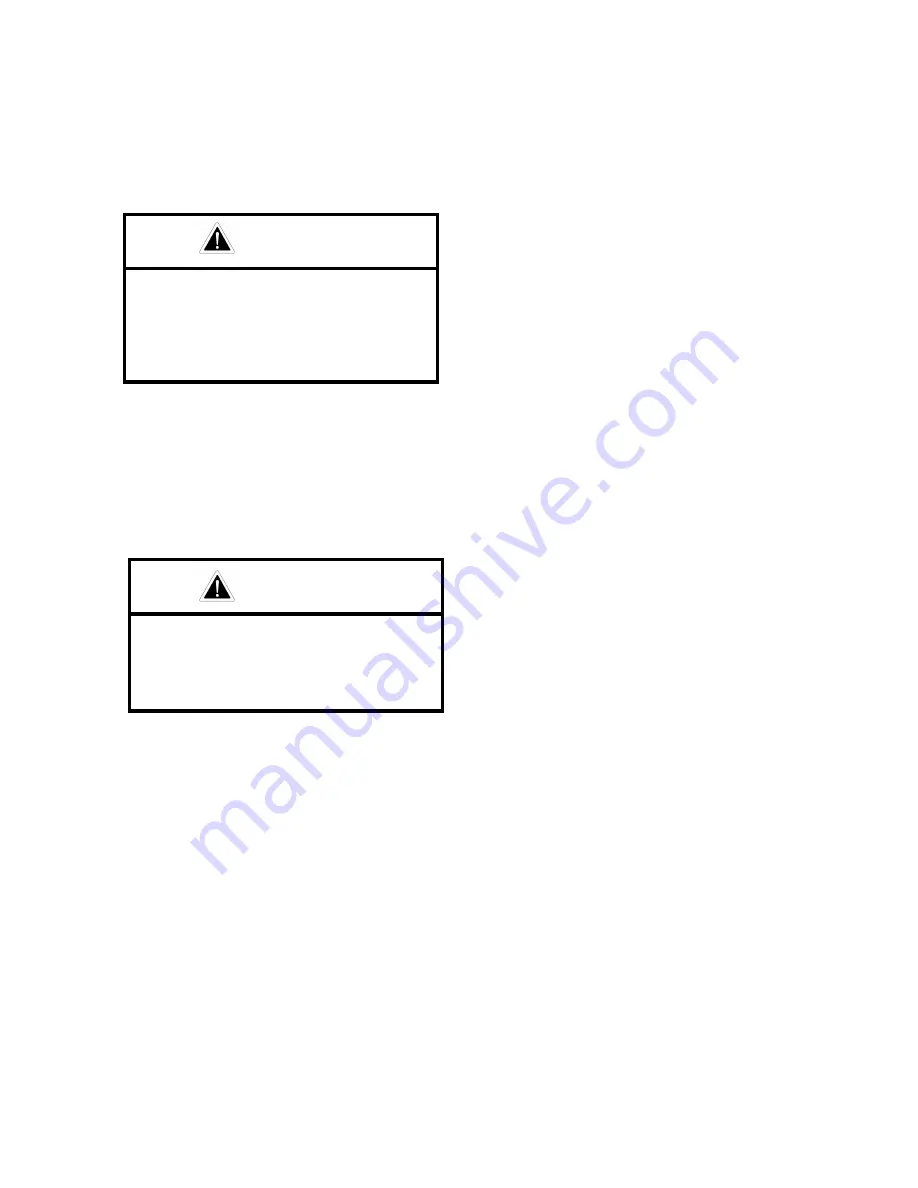
3-1-618 Page 4
Operating a pump against a blocked or
restricted discharge line can produce
excessive pressures in the entire discharge
system, which can damage or burst
discharge system components.
DANGER
Never operate a pump without a
properly sized pressure relief valve or
working overpressure shutdown in
the
discharge
line
immediately
adjacent to the pump discharge.
The relief valve should be placed in the
flowing discharge line and not at the
opposite end of the discharge manifold in a
dead end connection. The dead end may
become clogged with solid material carried
in the fluid, which could prevent proper
relief valve operation.
DANGER
Never place a shut-off valve or any
other component between the pump
discharge
connection
and
the
pressure relief valve.
Make sure the pressure relief valve is
installed so any pressurized relief discharge
from the valve is directed away from
possible contact with people or equipment.
The relief valve must be set to relieve at a
pressure equal to or below the maximum
pressure values shown on the pump data
plate. However, if a component is used in
the discharge system with a lower rated
pressure capability than that listed on the
pump data plate, the pressure relief valve
must be set to relieve at a pressure equal to
or below the rated capability of the lowest
rated component.
Before starting the pump every time,
check to insure:
•
The pressure relief valve is in good
operating condition and has been set to
the proper relief pressure.
•
Any pipe line used to direct pressurized
relief flow to another location, such as a
collecting tank, is not blocked.
•
The discharge system is not blocked
and all the discharge line valves are
open.
Check all fluid end discharge system
components including pipes, elbows
connections, threads, fasteners, hoses,
etc., at least once every six months to
confirm their structural adequacy. With
time, wear, corrosion and fatigue can
reduce the strength of all components.
Magnetic iron and steel components should
be checked with magnetic particle or dye
penetrant
crack
detection
equipment.
Nonmagnetic materials should be checked
for cracks with dye penetrants. All metallic
components
should
also
be
visually
checked during these inspections for signs
of corrosion. If a component shows
evidence of cracking or loss of material due
to corrosion it must be replaced with a new
part.
Continually monitor suction and discharge
hose assemblies when the pump is
operating for leakage, kinking, abrasion,
corrosion or any other signs of wear or
damage.
Worn or damaged hose assemblies
should be replaced immediately. At least
every six months examine hose assemblies
internally
for
cut
or
bulged
tube,
obstructions and cleanliness. For segment
style fittings, be sure that the hose butts up
against the nipple shoulder, the band and
retaining ring are properly set and tight and
the segments are properly spaced. Check
for proper gap between nut and socket or
hex and socket. Nuts should swivel freely.
Check the layline of the hose to be sure that
the assembly is not twisted. Cap the ends of
the hose with plastic covers to keep them
clean until they are tested or reinstalled on
the
pump
unit.