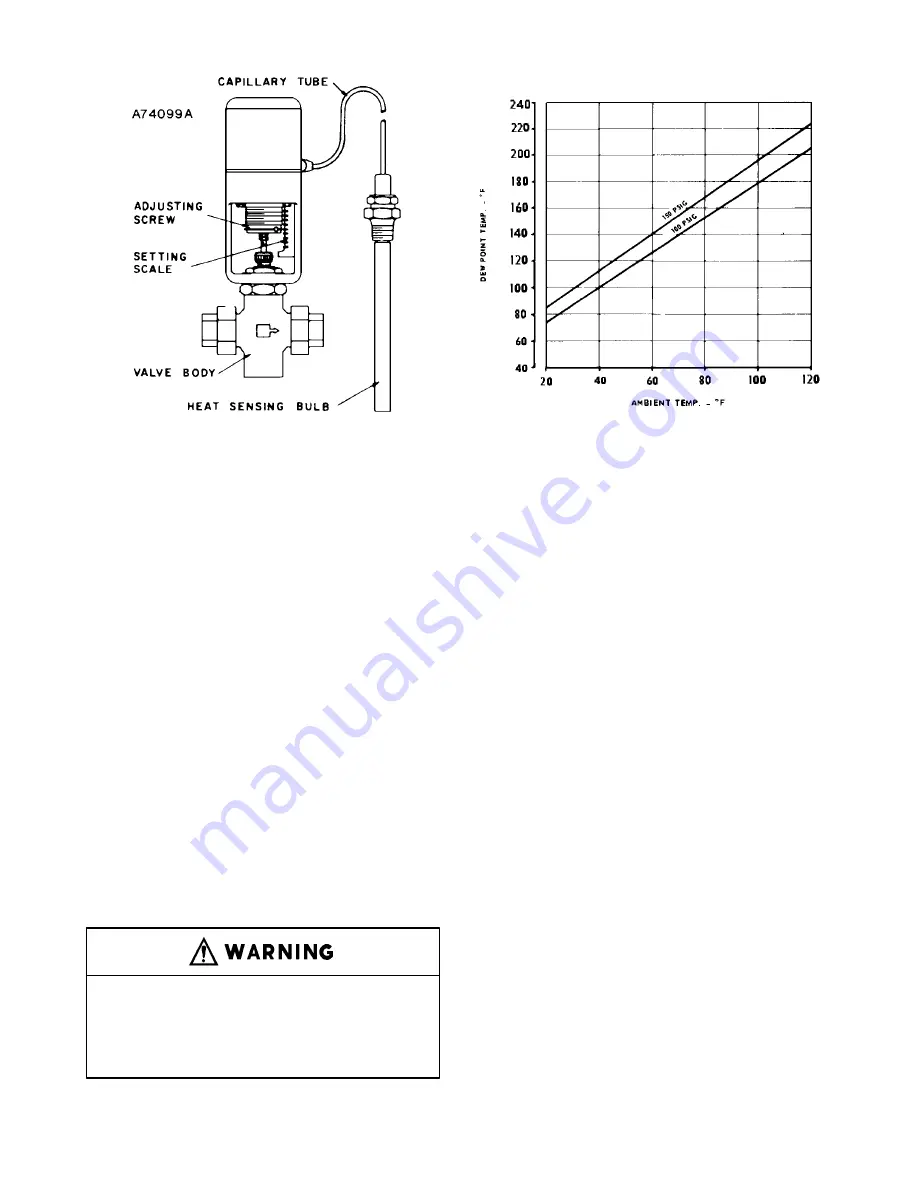
13–10–613 Page 35
FIGURE 5–7 – WATER CONTROL VALVE
FIGURE 5–8 – DEW POINT TEMPERATURE VS. AMBIENT
TEMPERATURE (100% RELATIVE HUMIDITY)
the oil from the cooler to mix with oil from the bypass.
After the unit is warmed up, the mixing valve maintains
oil injection temperature into the compressor at a mini-
mum of 150
_
F (66
_
C). This system provides proper
compressor warm–up and helps prevent moisture con-
tamination of oil.
To check element, heat in oil – it should be fully
extended at 150
_
F (66
_
C). If unit shuts down due to
high air discharge temperature, the cause may be that
the element is stuck open to the bypass, in which case
lines 1 and 2 (FIGURE 5–1, page 28) will be hot to
touch and lines 3 and 4 much cooler. When flushing the
oil system, remove mixing valve and clean all parts
thoroughly.
COMPRESSOR OIL COOLER – WATER–COOLED
HEAT EXCHANGER (FIGURE 1–2, page 2) – The
heat exchanger oil cooler is a multiple pass type, with
water in the tubes and oil in the shell. The oil tempera-
ture is controlled by the thermal (thermostatic mixing)
valve. The optional water control valve may be used to
conserve water.
It is mandatory that any water cooled
unit be installed in a shelter heated to
temperatures above freezing (32
_
F.,
0
_
C).
Oil cooler malfunction may be traced by checking pres-
sure at oil inlet and outlet. At normal operating air ser-
vice pressure (65 to 150 psig) with the unit warm, a
pressure drop of 3 to 15 psi can be expected between
the oil inlet and the oil outlet.
Water pressure drop from water inlet to outlet will vary
with the inlet pressure and amount of water flowing. A
normal pressure drop may range from 5 to 10 psi. Any
change in the pressure drop from that normally held
may indicate tube leakage or fouling and should be in-
vestigated.
In many instances, the cooling water supply for the heat
exchanger will contain impurities in solution and/or sus-
pension. These substances can cause scale forma-
tion, corrosion and plugging of any water–cooled heat
exchanger equipment. Disregarding the possibility that
one or more of these conditions exist may result in in-
creased maintenance and operation expense, reduced
equipment life and emergency shutdown. It is strongly
recommended that a reputable, local water treatment
concern be engaged to establish the corrosion, scale
forming and fouling tendency of the cooling water and
take steps necessary to remedy the situation if a
problem does exist. The need for water treatment may
involve only filtration (screening) to remove debris,
sand and/or salt in the cooling water supply. However,
chemical treatment methods may be necessary in cer-
tain instances to inhibit corrosion and/or remove dis-
solved solids, to alter the water’s tendency to form
scale deposits, or prevent the growth of microorgan-
isms. The normal maintenance program for the unit
should also include periodic cleaning of the tubes (wa-
Summary of Contents for ELECTRA-SAVER EAY
Page 14: ...13 10 613 Page 6 DECALS 206EAQ077 212EAQ077 218EAQ077 211EAQ077 207EAQ077...
Page 15: ...13 10 613 Page 7 DECALS 216EAQ077 217EAQ077 222EAQ077 221EAQ077 208EAQ077...
Page 32: ...13 10 613 Page 24 FIGURE 4 8 CONTROL SCHEMATIC COMPRESSOR AT FULL LOAD 204EAY797 B Ref Drawing...
Page 35: ...13 10 613 Page 27 FIGURE 4 11 WIRING DIAGRAM 202EAY546 Ref Drawing...
Page 55: ......