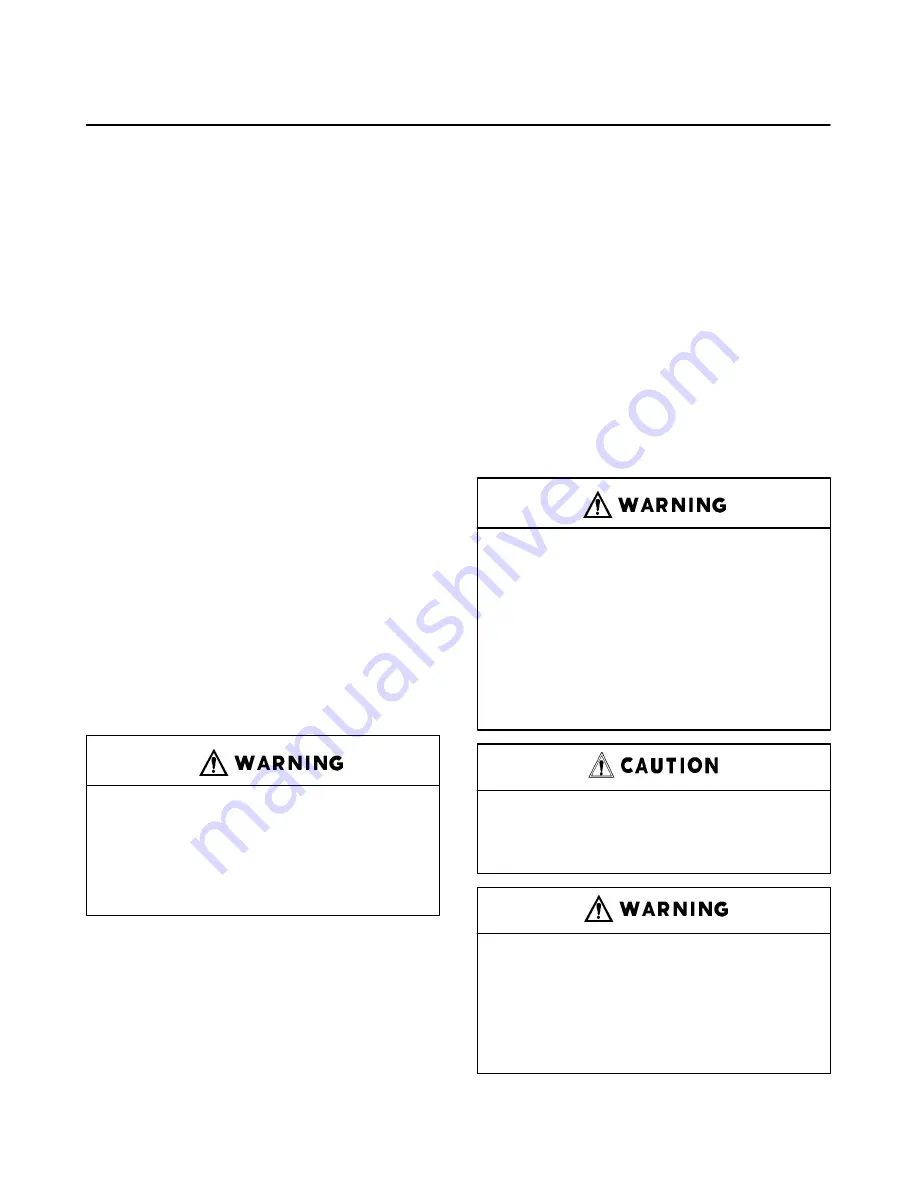
13–10–613 Page 18
SECTION 4
CONTROLS & INSTRUMENTATION
GENERAL DESCRIPTION – The Gardner Denver
rotary screw compressor is prewired with all controls
for the voltage and horsepower at the time of ordering.
It is necessary only to connect the motor to the custom-
er–supplied starters, the compressor unit to the correct
power supply and to the shop air line (and to the ap-
propriate water supply if water cooled). A standard
compressor unit consists of the compressor, oil reser-
voir, oil cooling system and filter, motor type as speci-
fied, NEMA 12 control box, and control components as
described below.
AUTO SENTRY
OPERATION
Operation of the “AUTO SENTRY
” controller is de-
pendent on selection of an operating mode from the
controller keypad. Prior to starting, the [STOP/RESET]
key must be pressed to place the controller into its
“READY” state (as indicated on the display). Compres-
sor operation may then be started by pressing an oper-
ating mode key.
AUTOMATIC is the most commonly selected mode of
operation, as it will operate the compressor unit auto-
matically in the most efficient manner for the demand
of the air system.
Once operating, the mode may be changed at any time
by pressing a key, and the selected mode will be dis-
played in the lower right corner of the message window.
Press the [STOP/RESET] key at any time to stop the
compressor under normal conditions.
Detailed instructions for the controller are found in the
manual 13–9/10–647.
Automatic restarting or electrical
shock can cause injury or death.
Open, tag and lockout main discon-
nect and any other circuits before
servicing the unit.
CONTROL DEVICES
Controller – This compressor unit features the “AUTO
SENTRY
” controller, which integrates all the control
functions under microprocessor control. Its functions
include safety and shutdown, compressor regulation,
operator control, and advisory/maintenance indicators.
The keypad and display provide the operator with a log-
ical and easily operated control of the compressor and
indication of its condition. The controller is factory ad-
justed for the compressor package, but allows tuning
for specific applications.
Relief Valve – A pressure relief valve(s) is (are)
installed in the final discharge line and set to approxi-
mately 120–125% of the unit’s full load operating pres-
sure for protection against over pressure. Periodic
checks should be made to ensure its (their) operation.
The relief valve should be tested for proper operation
at least once every year. To test the relief valve, raise
the system operating pressure to 75% of the relief valve
set pressure and manually open the valve with the hand
lever. Hold the valve open for a few seconds and allow
it to snap shut.
When the relief valve opens, a stream
of high velocity air is released, result-
ing in a high noise level and possible
discharge of accumulated dirt or oth-
er debris. Always wear eye and ear
protection and stand clear of the dis-
charge port when testing the relief
valve to prevent injury.
Never paint, lubricate or alter a relief
valve. Do not plug vent or restrict dis-
charge.
Operation of unit with improper relief
valve setting can result in severe per-
sonal injury or machine damage.
Insure properly set valves are in-
stalled and maintained.
Summary of Contents for ELECTRA-SAVER EAY
Page 14: ...13 10 613 Page 6 DECALS 206EAQ077 212EAQ077 218EAQ077 211EAQ077 207EAQ077...
Page 15: ...13 10 613 Page 7 DECALS 216EAQ077 217EAQ077 222EAQ077 221EAQ077 208EAQ077...
Page 32: ...13 10 613 Page 24 FIGURE 4 8 CONTROL SCHEMATIC COMPRESSOR AT FULL LOAD 204EAY797 B Ref Drawing...
Page 35: ...13 10 613 Page 27 FIGURE 4 11 WIRING DIAGRAM 202EAY546 Ref Drawing...
Page 55: ......