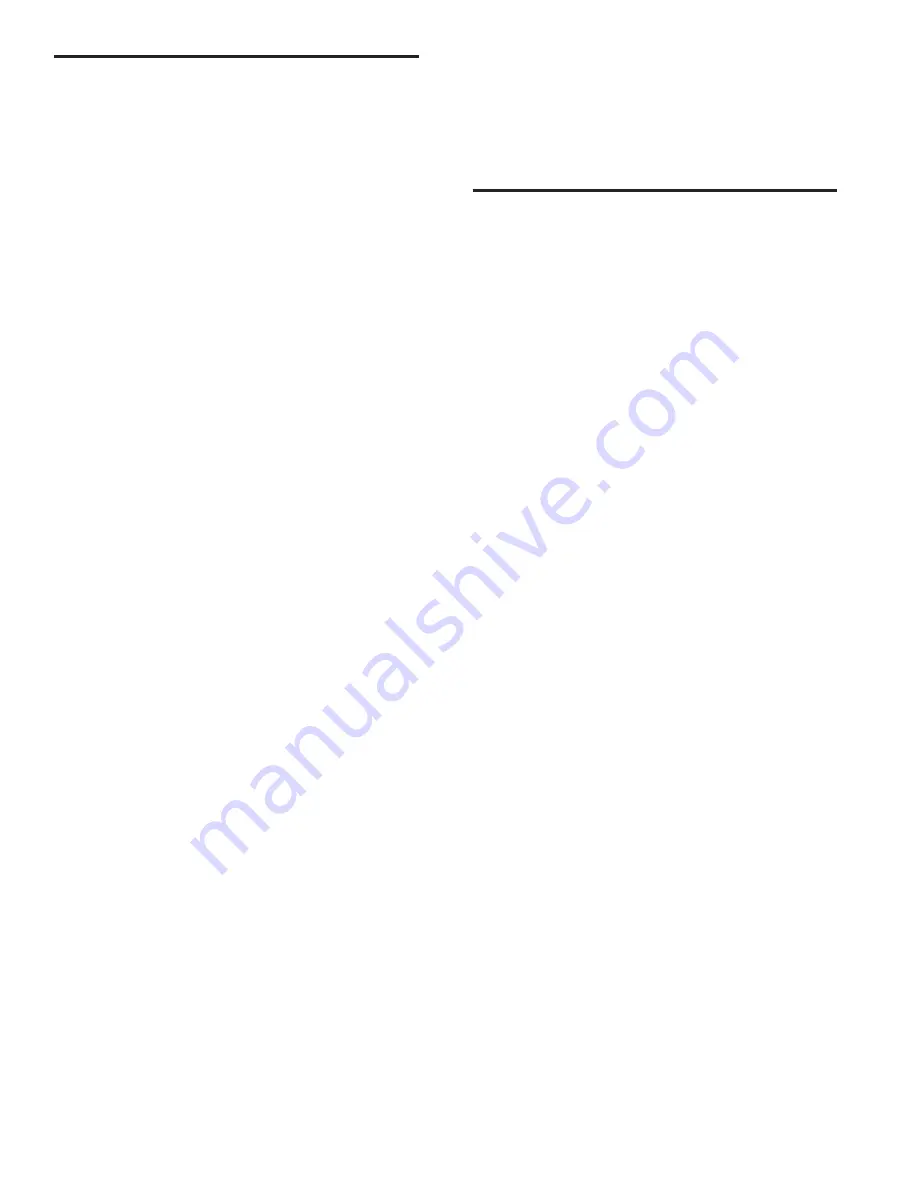
2
1.0 General Safety Information
This equipment is designed and built with safety as a prime
consideration; industry-accepted safety factors have been
used in the design. Each dryer is checked at the factory for
safety and operation. All pressure vessels which fall under
the scope of ASME Section VIII, are hydrostatically tested
in accordance with the latest addenda. A factory-installed
safety relief valve is standard on each dryer.
WARNING — The following safety rules must be
observed to ensure safe dryer operation. Failure to
follow these rules may void the warranty or result in
dryer damage or personal injury.
1. Never install or try to repair any dryer that has been
damaged in shipment. See the Receiving and Inspec-
tion instructions in this manual for appropriate action.
2. This equipment is a pressure-containing device.
Never operate the dryer at pressures or temperatures
above the maximum conditions shown on the data
plate.
Never dismantle or work on any component of the
dryer or compressed air system under pressure. Vent
internal air pressure to the atmosphere before servic-
ing.
3. This equipment requires electricity to operate. Install
equipment in compliance with national and local elec-
trical codes. Standard equipment is supplied with
NEMA 4,4X electrical enclosures and is not intended
for installation in hazardous environments.
Never perform electrical service on the dryer unless
the main power supply has been disconnected. Parts
of the control circuit may remain energized when the
power switch is turned off.
4. Air treated by this equipment may not be suitable for
breathing without further purification. Refer to OSHA
standard 1910.134 for the requirements for breathing
quality air.
5. Certain parts of the dryer are not insulated and may
become hot during normal operation of the dryer. Do
not touch any of these areas without first determining
the surface temperature.
6. Use only genuine replacement parts from the manu-
facturer. The manufacturer bears no responsibility for
hazards caused by the use of unauthorized parts.
Safety instructions in this manual are boldfaced for
emphasis. The signal words
DANGER
,
WARNING
and
CAUTION
are used to indicate hazard seriousness levels
as follows:
DANGER
—Immediate hazard which will result in severe
injury or death.
WARNING
—Hazard or unsafe practice which could result
in severe injury or death.
CAUTION
—Hazard or unsafe practice which could result
in minor injury or in product or property damage.
The dryer data plate, attached to the electrical control box,
contains critical safety and identification information. If the
data plate is missing or defaced, immediately contact your
local distributor for a replacement.
2.0 Receiving, Storing, and Moving
2.1 Receiving and Inspection
This shipment has been thoroughly checked, packed and
inspected before leaving our plant. It was received in
good condition by the carrier and was so acknowledged.
Immediately upon receipt, thoroughly inspect for visible
loss or damage that may have occurred during shipping.
If this shipment shows evidence of loss or damage at time
of delivery to you, insist that a notation of this loss or dam-
age be made on the delivery receipt by the carrier’s agent.
Otherwise no claim can be enforced against the carrier.
Also check for concealed loss or damage. When a ship-
ment has been delivered to you in apparent good order,
but concealed damage is found upon unpacking, notify
the carrier immediately and insist on his agent inspecting
the shipment. The carrier will not consider any claim for
loss or damage unless an inspection has been made. If
you give the carrier a clear receipt for goods that have
been damaged or lost in transit, you do so at your own
risk and expense. Concealed damage claims are not our
responsibility as our terms are F.O.B. point of shipment.
Shipping damage is not covered by the dryer warranty.
2.2 Storing
Store the dryer indoors to prevent damage to any electrical
or mechanical components. All packaging material should
be left in place until the dryer is in position.
2.3 Handling
The dryer is designed to be moved by means of the ship-
ping skid or the base channels. The dryer may also have
lifting lugs for use with an overhead crane. Be sure to
attach all of the lift points and use appropriate spreader
bars to prevent damage to the dryer.
CAUTION — Never lift the dryer by attaching hooks
or slings to the piping, or to any part other than the
lifting lugs. severe structural damage could occur.