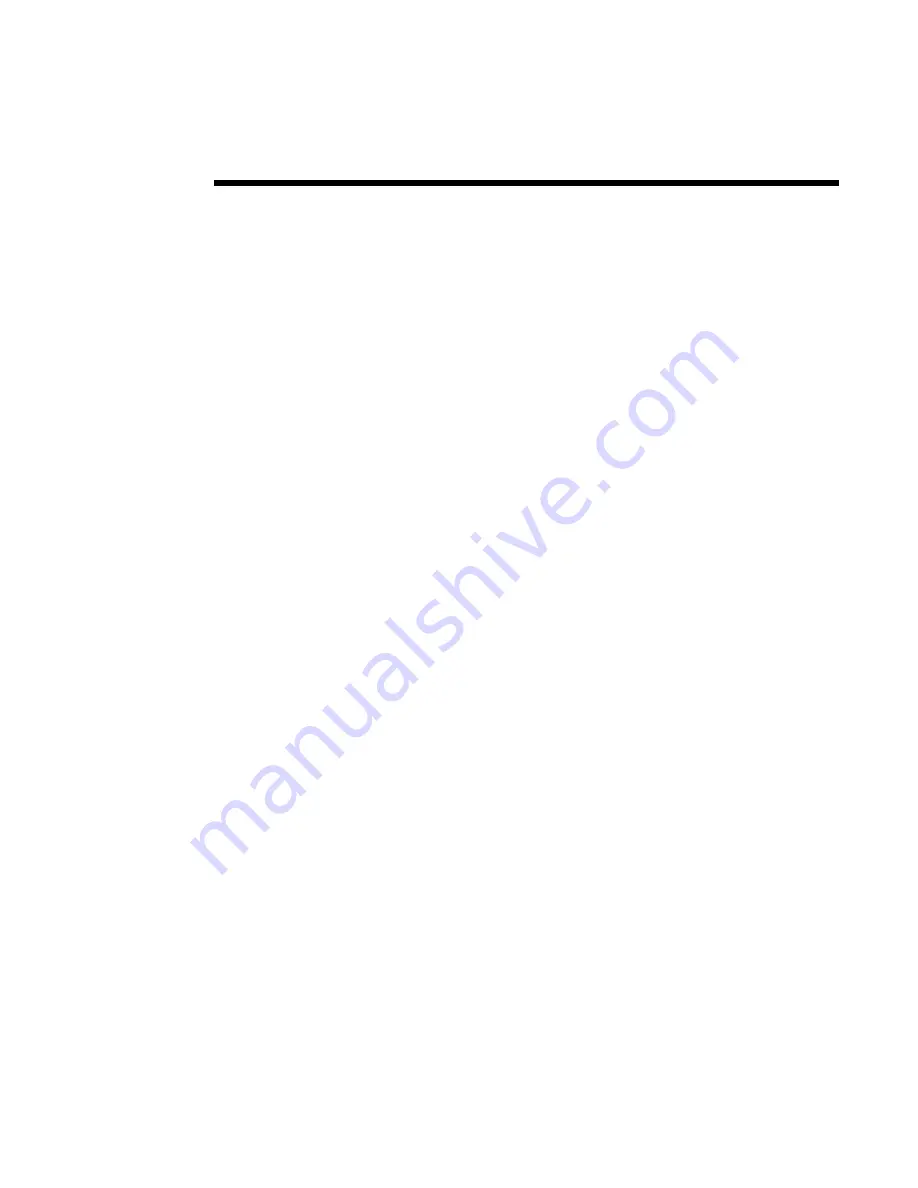
USER MANUAL
DMC-1500
Manual Rev. 2.0xf
By Galil Motion Control, Inc.
Galil Motion Control, Inc.
270 Technology Way
Rocklin, California 95765
Phone: (916) 626-0101
Fax: (916) 626-0102
Internet Address: [email protected]
URL: www.galilmc.com
Rev 05-06
Summary of Contents for DMC-1510
Page 6: ......
Page 18: ...6 Chapter 1 Overview DMC 1500 THIS PAGE LEFT BLANK INTENTIONALLY...
Page 88: ...76 Chapter 6 Programming Motion DMC 1500 Figure 6 7 Motion intervals in the Home sequence...
Page 90: ...78 Chapter 6 Programming Motion DMC 1500 THIS PAGE LEFT BLANK INTENTIONALLY...
Page 137: ...DMC 1500 Chapter 7 Application Programming 125 THIS PAGE LEFT BLANK INTENTIONALLY...
Page 157: ...DMC 1500 Chapter 10 Theory of Operation 145 THIS PAGE LEFT BLANK INTENTIONALLY...
Page 160: ...148 Appendices DMC 1500 Card Level Layout...
Page 180: ...168 Appendices DMC 1500...
Page 198: ...186 Appendices DMC 1500 THIS PAGE LEFT BLANK INTENTIONALLY...