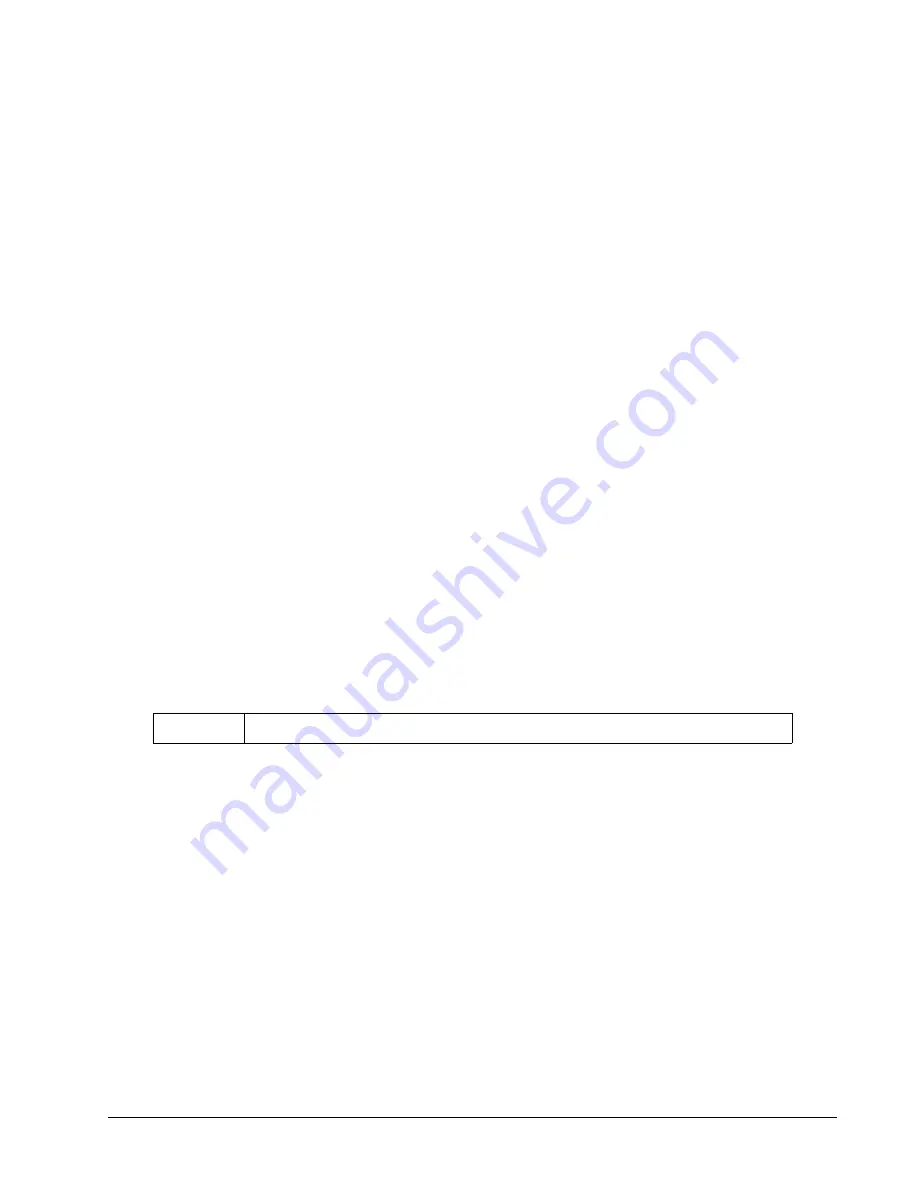
signal to the + input and leave the - input disconnected. For other signal levels, the - input should be connected to
a voltage that is ½ of the full voltage range (for example, connect the - input to 6 volts if the signal is a 0 - 12 volt
logic).
Example:
A DMC-4010 has one auxiliary encoder. This encoder has two inputs (channel A and channel B). Channel A input is
mapped to input 81 and Channel B input is mapped to input 82. To use this input for 2 TTL signals, the first signal
will be connected to AA+ and the second to AB+. AA- and AB- will be left unconnected. To access this input, use
the function @IN[81] and @IN[82].
NOTE:
The auxiliary encoder inputs are not available for any axis that is configured for stepper motor.
Electrical Specifications
Maximum Voltage
12 VDC
Minimum Voltage
-12 VDC
'+' inputs are internally pulled-up to 5V through a 4.7kΩ resistor
'-' inputs are internally biased to ~1.3V
pulled up to 5V through a 7.1kΩ resistor
pulled down to GND through a 2.5kΩ resistor
Output Compare
The output compare signal is a TTL ouput signal and is available on the I/O (A-D) D-Sub connector labeled as CMP.
An additional output compare signal is available for 5-8 axes controllers on the I/O (E-H) D-sub connector.
Output compare is controlled by the position of any of the main encoder inputs on the controller. The output can
be programmed to produce either a brief, active low pulse (250 nsec) based on an incremental encoder value or to
activate once (“one shot”) when an axis position has been passed. When setup for a one shot, the output will stay
low until the OC command is called again. For further information, see the command OC in the Command
Reference.
NOTE
Output compare is not valid with sampled feedback types such as: SSI, BiSS, Sin/Cos, and Analog
Electrical Specifications
Output Voltage
0 – 5 VDC
Current Output
20 mA Sink/Source
Error Output
The controller provides a TTL signal, ERR, to indicate a controller error condition. When an error condition occurs,
the ERR signal will go low and the controller LED will go on. An error occurs because of one of the following
conditions:
1. At least one axis has a position error greater than the error limit. The error limit is set by using the
command ER.
2. The reset line on the controller is held low or is being affected by noise.
3. There is a failure on the controller and the processor is resetting itself.
4. There is a failure with the output IC which drives the error signal.
The ERR signal is found on the I/O (A-D) D-Sub connector.
Chapter 3 Connecting Hardware ▫ 41
DMC-40x0 User Manual